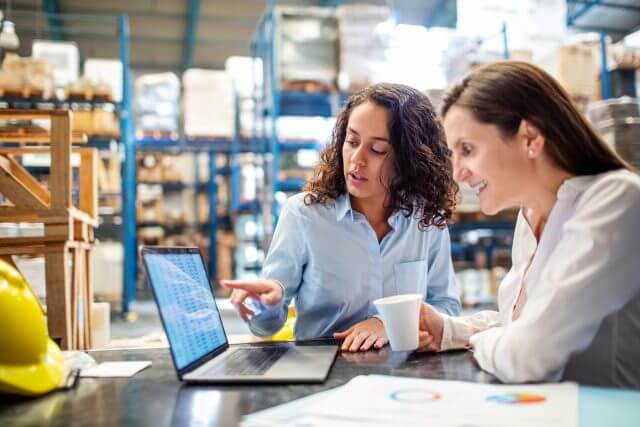
A suply chain em 2025: O que esperar
Em 2025, a supply chain continua sua evolução rumo à “Logística 4.0”, inspirada na Indústria 4.0. Duas características principais definem…
Generix faz parceria com a VISEO para ajudar clientes a lidar com regulamentações complexas de faturamento eletrônico e otimizar suas jornadas de transformação digital. Veja o comunicado de imprensa
Após o recebimento, os produtos, sejam quais forem, podem ser armazenados em múltiplos locais do armazém. Geralmente existem vários tipos de áreas de armazenamento: racks para paletes completos de diferentes dimensões e tolerâncias de peso, locais para armazenagem de caixas, compartimentos para armazenagem de itens individuais para picking… Tudo em modo manual ou mecanizado e disponível em múltiplas variantes.
Para cada uma das categorias acima presentes em um armazém, há uma distribuição geográfica das localizações, que é mais ou menos fácil de acessar.
Ao implementar um WMS, pode-se atribuir critérios a cada local que definirão sua acessibilidade, os tipos de preparação autorizados e sua inclusão nos circuitos de preparação. Ao mesmo tempo, trabalharemos na categorização dos produtos em função das muitas características disponíveis no repositório (dados básicos ou “Master Data”): características físicas, tipo de embalagem, família de produtos, taxa de rotação, etc.
O papel do WMS será processar todas essas informações e depois calcular a melhor forma de armazená-la. Para isso, utilizaremos uma estratégia de armazenamento que utiliza um algoritmo – esta é a estratégia de busca de localização (SRE).
Este algoritmo otimiza a forma de armazenar os produtos conforme critérios escolhidos dentre os mencionados anteriormente. Uma parametrização permitirá então utilizar um critério em vez de outro, e priorizar alguns deles em função dos objetivos.
Resumindo, a otimização significa armazenar os produtos em um local conveniente para a preparação do pedido, a parte mais demorada do processo. Portanto, os produtos de alta rotação serão colocados o mais próximo possível das estações de embalagem ou das docas de embarque, conforme o caso.
Isto se baseia frequentemente na taxa de rotação dos estoques (a velocidade com que é renovado um produto no armazém). Isso é conhecido como “estratégia ABC“: onde A corresponde aos produtos com uma alta rotatividade, e C aos produtos que acumulam pó, também conhecidos como “slow mover“. O armazenamento pode ser feito de acordo com a classificação ABC como prioridade, e depois ser acoplado com outros critérios conforme a parametrização escolhida.
O WMS também oferece a possibilidade de trabalhar com um algoritmo de aspersão, que permite que os produtos sejam distribuídos em vez de preencher a mesma zona com uma única referência.
Outra opção utilizada frequentemente é o armazenamento o mais próximo possível do picking. No caso de picking na parte inferior da prateleira de paletes, um algoritmo pode ser configurado para armazenar preferencialmente os paletes de reserva logo acima e depois ao lado dos locais de picking para esta mesma referência. Isso resulta em missões de reabastecimento mais curtas.
A lógica da fase de armazenamento também se aplica à fase de preparação. Nos armazéns ou áreas de armazenamento tradicionais, a preparação é realizada na parte inferior da prateleira de paletes: os paletes completos estão localizados na parte superior da área de armazenamento, enquanto as áreas de armazenamento inferior são utilizadas para o picking pela unidade ou pela embalagem.
A correlação entre demanda e organização é fundamental no WMS para maximizar o desempenho da preparação. Por sua vez, a gestão dos pickings deve ser totalmente adaptada ao tipo de vendas. Para isso, o WMS irá propor a gestão dos locais de preparação picking de forma “fixa” ou “efêmera”. Em todos os casos, estes métodos de gestão são complementares a fim de adaptar as operações às necessidades do mercado. Por isso o picking “efêmero” pode se tornar “fixo”, quando a demanda associada ao produto diminui ao longo dos dias ou temporadas.
O picking fixo, que é ainda mais relevante numa organização dita linear, está associado a um percurso de preparação que corresponde à lógica da circulação nos corredores. O objetivo é otimizar os movimentos ou a constituição do suporte de preparação, ou a disposição na caixa ou pacote. Isso evita uma ruptura da carga no final da preparação ou na chegada às instalações do cliente. Claramente, priorizamos desde o início a preparação de um pedido em um único pacote, sempre que possível. Isso evita ter que reembalá-los no final da preparação ou enviá-los em dois pacotes, quando um poderia ser suficiente.
A criação de rotas é definida pelo responsável dos estoques conforme as necessidades do cliente. Respeita as normas relacionadas ao produto: categoria, família, peso/volume, rotação etc. No entanto, existem inúmeras combinações possíveis para otimizar a sua constituição e promover a sua complementariedade. Os algoritmos são então importantes no WMS para dar ao responsável visibilidade sobre a dupla estratégica carga/capacidade.
Último passo: um caminho é estabelecido com base na análise dos dados relativos à vida do armazém combinando o espaço disponível e os tipos de produto, conforme a demanda. No momento do armazenamento dos produtos no recebimento, são utilizados outros cálculos para propor localizações de reserva o mais perto possível dos pickings correspondentes a cada referência.
Com o picking temporário ou “restrito”, recalculamos a implementação dos pickings dinamicamente durante o processamento da onda de preparação de acordo com as restrições:
Os algoritmos serão então configurados para implementar pickings correspondentes a cada referência da maneira mais relevante. Essa abordagem é muito eficaz para lidar com grupos de referência relativamente pequenos, que têm uma demanda muito alta por um período limitado de tempo. É o caso, por exemplo, do lançamento de uma nova coleção ou de uma promoção.
É possível decidir combinar o respeito dos “contratos-data” com as datas de vencimento. Nesse caso, uma margem de segurança configurável é adicionada à data de vencimento para honrar o compromisso do cliente. Esta é uma técnica muito comum no setor de varejo para garantir uma certa vida útil, que é particularmente crítica para produtos perecíveis.
Este algoritmo de respeito dos “contratos-data” também pode ser aplicado a todas as operações do armazém, e é um dos pontos fortes do WMS da Generix Group.
Este é um passo fundamental para otimizar o planejamento do trabalho com base em um portfólio de pedidos a serem processados. Selecionaremos pedidos, ou determinados elementos de um pedido, e escolheremos uma forma de gerenciar com eficiência seu processamento.
Para fazer essa seleção automaticamente, vamos configurar “ondas” de pedidos. Uma onda é uma seleção no portfólio de produtos, feita a partir de vários critérios. As questões mais representativas do planejamento são:
Portanto, também é possível injetar pedidos provenientes do TMS. Neste caso, falamos de “preparação elaborada pelo TMS”.
O talento do gestor está em sua capacidade de ajustar suas ferramentas para coordenar esse trabalho em função dos horários gerenciáveis e ajustáveis de acordo com a carga do dia e os recursos disponíveis. Tradicionalmente, o planejamento é feito com base em meio dia ou dia inteiro. Entretanto, tudo permanece viável, de acordo com o modelo organizacional escolhido pelo gestor. Além disso, também é possível escolher os modelos de ondas de acordo com as necessidades do dia.
A onda, cujo resultado representa uma lista de produtos a serem preparados (ou “fila”), é apenas a primeira etapa do cálculo algorítmico. Esse primeiro cálculo não está tanto focado na produtividade das operações quanto na prioridade dos pedidos a serem atendidos.
A partir desta lista, o sistema calculará fluxos de trabalho sucessivos em grupos de pedidos: irá gerar as chamadas “missões”. Uma missão é uma lista de tarefas que serão oferecidas aos operadores. Isso levanta a questão de como organizar essas tarefas de maneira lógica para melhorar a produtividade no armazém. Muitos parâmetros, portanto, entram em jogo, incluindo a otimização de rotas de preparação ou triangulação.
Uma missão recente do DataLab da Generix Group a um dos clientes do grupo demonstrou que as rupturas durante a preparação foram o principal fator de menor produtividade. Portanto, é fundamental que o preparador nunca se encontre diante de um espaço vazio ou insuficientemente abastecido para que o pedido seja atendido. Nesse caso, ele teria que fazer um pedido urgente de reabastecimento (o que sempre é possível) e esperar que um palete seja “baixado” da reserva para que ele possa concluir sua missão. Embora o preparador sempre possa alternar para outro pedido, o processo não é o ideal.
Para evitar este tipo de situação, recorreremos a dois tipos de estratégia preventiva: o ajuste dos limites de reabastecimento e antecipação com base em cálculos feitos previamente (na véspera, por exemplo).
Os limites de reabastecimento permitem evitar as rupturas. Estabelece-se uma configuração para colocar em funcionamento uma missão de reabastecimento assim que é atingida uma quantidade mínima ou um “limite de reabastecimento” em um local de picking. Esta é uma tarefa precisa, que deve levar em conta a capacidade do local de armazenamento. Obviamente, é impossível colocar dois paletes em um local dimensionado para um palete, mas provavelmente podemos colocar um palete e uma camada de caixas. As dimensões dos locais, dos paletes e das caixas são inseridas no sistema, e o cálculo é feito automaticamente graças a algoritmos simples que somam as dimensões dos objetos com uma certa tolerância.
Para antecipação, podemos usar uma ferramenta de simulação, que também é baseada em um algoritmo. Sua função é simular a onda de preparação com base na carteira de pedidos a serem atendidos. Ele deduz a quantidade total necessária para cada uma das referências, verifica a quantidade restante no local de picking e aciona automaticamente uma enxurrada de missões de reabastecimento, direcionadas aos pedidos a serem atendidos o mais rápido possível.
Esta operação pode ser calculada a partir da carteira de pedidos já recebidos no WMS, mas também pode ser baseada em dados de previsão transmitidos pelo ERP ao WMS na forma de uma mensagem específica. Por exemplo, podemos usar o consumo do armazém da última semana de um período de referência considerado relevante para levar em consideração a sazonalidade ou qualquer modelo de negócios cíclico.
Para evitar isto, também é possível pré-preencher todos os pickings do dia anterior. O problema é que essa estratégia só pode funcionar se você tiver tempo e recursos. Ao operar em uma base just-in-time, selecionar os reabastecimentos realmente úteis é de longe a melhor abordagem.
Diante de períodos tensos com cargas muito elevadas, os algoritmos do WMS permitem ainda mais precisão no acionamento de tarefas de reabastecimento com base nas urgências. Isso garantirá o uso ideal dos recursos, com foco nas necessidades críticas em tempo real.
Esta ferramenta automatiza o gerenciamento dos reabastecimentos, permitindo que o sistema os acione no momento mais adequado, como e quando necessário. O sistema é obviamente baseado em dados teóricos específicos para cada warehouse e o tipo de gestão de preparação. Este recurso ganancioso em cálculos algorítmicos levará em consideração muitos parâmetros:
Com base nestes critérios, que podem ser priorizados pela parametrização, o sistema recalculará as necessidades da preparação em andamento e definirá um momento preciso para o acionamento de uma missão de reabastecimento. Para ilustrar a profundidade deste cálculo, podemos citar a consideração de elementos como tempo de coleta, tempo de troca de produto, tempo de troca de corredor, tempo de antecipação e até tempos de pausa!
Dependendo se são empilhadeiras que movimentam paletes ou preparadores trabalhando no picking, o trabalho será feito de forma diferente.
O “batch picking”, ou “massificação”, é um método de preparação de pedidos que se caracteriza pelo picking simultâneo de várias unidades do mesmo código SKU.
Em termos concretos, o preparador utiliza um carrinho de preparação no qual serão colocados “N” recipientes correspondentes a “N” pedidos diferentes. Ele poderá então distribuir a mesma referência em vários pedidos no mesmo ponto de picking, minimizando assim seus movimentos. Para ajudar o preparador, um algoritmo calculará a divisão das tarefas para agrupá-las de forma otimizada.
Este princípio é particularmente utilizado nos setores de e-commerce e têxtil, que lidam com um grande número de pequenas encomendas (geralmente entre 1 e 3 peças).
Também é possível calcular a constituição das tarefas de acordo com um algoritmo de cálculo de distâncias. Essa funcionalidade é implementada mediante a configuração de uma calculadora de distâncias. Isso consiste em estabelecer pontos de referência e ligações entre os corredores de armazenagem para calcular a duração do percurso entre dois pontos de armazenagem, que podem estar localizados em corredores diferentes.
Podemos distinguir quatro tipos principais de missões para um operador de empilhadeira:
Essas missões podem ser combinadas ou cruzadas. Utilizamos o termo em inglês “interleaving“.
Uma grande fonte de produtividade reside na combinação de missões de armazenamento com missões de desestocagem. Na maioria das vezes, combinaremos duas missões cujos pontos de entrega e retirada estão no mesmo corredor. Essas estratégias são particularmente eficazes nas chamadas áreas de armazenamento de “corredor estreito” (VNA para very narrow aisle) porque as empilhadeiras “tridi” (turret truck) são mais lentas. Também são cruciais ao usar carrinhos do tipo AGVs (Automated Guided Vehicle), que têm velocidades de viagem particularmente lentas.
A triangulação é um método utilizado para medir distâncias em uma escala humana. É um processo para determinar uma distância calculando o comprimento de um dos lados de um triângulo e medindo dois ângulos deste triângulo usando entidades trigonométricas. O WMS utiliza este processo para aplicá-lo à gestão de armazéns e, assim, otimizar os deslocamentos aplicando os caminhos mais diretos possíveis.
A triangulação é ideal em um contexto de radiofrequência. Na verdade, os cenários garantem a geração automática de missões por triangulação para operadores de empilhadeiras ou transportadores. Nesse caso, os algoritmos WMS trabalharão a partir de vários elementos:
O WMS também pode calcular uma alocação inteligente de docas em dois momentos-chave.
Dependendo de onde a massa crítica de uma remessa é armazenada, a doca de descarga será atribuída o mais próximo possível do local de armazenamento de destino preferido.
Será possível escolher a doca de carregamento mais próxima do local de coleta, mas também podemos usar um recurso de alocação dinâmica.
Com este modo de operação, o WMS poderá sincronizar fluxos de diferentes tipos (mono ou multipedidos, etc). Isso permitirá alocar dinamicamente uma doca de carregamento final ao validar os suportes no final da preparação. O algoritmo levará então em conta o estado de congestionamento das docas enquanto verifica os critérios de consistência (cliente, data de entrega, pedido).
Métodos baseados em algoritmos também são usados para encher os caminhões o máximo possível. Este trabalho é feito principalmente em colaboração com o TMS.
O conceito de cross-docking consiste em redistribuir os suportes em recebimeneto diretamente para uma doca de embarque sem passar por um estágio de armazenamento. Os algoritmos do WMS podem trabalhar em dois níveis. No caso de armazéns muito longos que não são projetados como plataformas de cross-docking, será favorecida uma alocação inteligente de docas de recepção e/ou expedição, de modo a aproximá-los e, assim, minimizar as distâncias de deslocamento.
No caso de referências em recebimento que também estão em estoque, o WMS pode implementar algoritmos mais sofisticados que levarão em consideração diversos parâmetros. Ou seja: podemos atender uma necessidade “em onda” com um palete recebido na doca. O sistema também está autorizado para uso na doca para evitar transferências sucessivas (o objetivo é minimizar as “rupturas de carga”). Neste caso, pode-se decidir não respeitar o FIFO (First In First Out). O sistema verifica o cumprimento das datas de vencimento e dos “contratos-data”.
Em 2025, a supply chain continua sua evolução rumo à “Logística 4.0”, inspirada na Indústria 4.0. Duas características principais definem…
Você deseja modernizar profundamente sua tecnologia de colaboração sem interrupções? Para ajudar a conectar empresas, temos o prazer de anunciar…
Quando as operações de logística ganham escala e/ou se tornam mais complexas, o software WMS (Warehouse Management System) torna-se indispensável.…
Trabalhe com nossa equipe para criar sua pilha ideal de software de cadeia de suprimentos e adaptá-la às suas necessidades comerciais exclusivas.