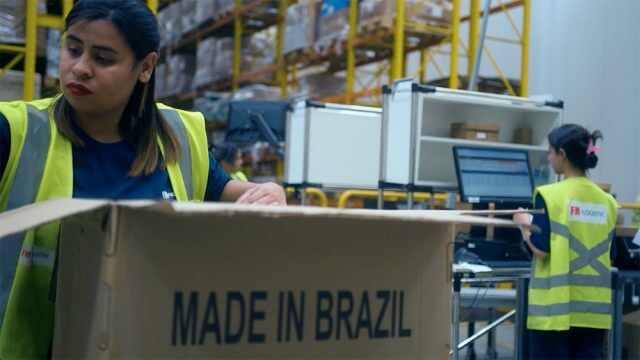
Generix WMS and FM Logistic Brazil simplify processes and increase efficiency in their 70,000 square meters of warehouses.
Transformation and Efficiency with Generix WMS Solution
Generix Announces the Appointment of Olivier Vaillancourt as General Manager for North America View the press release
Novexco was founded in 1996 and is now the largest national distributor of Canadian-owned office supplies and services. The company has 8 distribution centers located across Canada, the largest and most sophisticated of which is in Laval, Quebec. They offer computer supplies, printer cartridges and ribbons, office equipment, writing products, stationery and office accessories, furniture, games, and gifts. All of their items can be found through their Hamster sales division. In 2015, Novexco had approximately 18,000 UPC codes and generated approximately 4,500 orders per day and 22,500 pick lines for their Laval DC alone. Novexco has implemented the Solochain WMS in more than 6 distribution centers with 2 more to come before the end of 2021.
Novexco is able to compete with online retail giants such as Amazon thanks to its unique and creative business model, based on its strategically placed warehouses in major urban centers and over 100 Hamster stores. This system is designed to offset high transportation costs and optimize last mile logistics, the biggest challenge for all Canadian retailers. The ability to offer quality products at a competitive price thanks to robust logistics is a major selling point in competing with e-commerce giants. Novexco can now guarantee next-business-day delivery in most regions of Canada.
Challenges
…The implementation has been a complete success, and we are seeing positive results less than a year after the introduction of the WMS and the intelligent conveyor technology. We have seen a 30% increase in productivity, a significant reduction in backlogs and an improvement in the quality of order picking with these two technology systems. François Milette VP Supply Chain and Customer Service Novexco
…The implementation has been a complete success, and we are seeing positive results less than a year after the introduction of the WMS and the intelligent conveyor technology. We have seen a 30% increase in productivity, a significant reduction in backlogs and an improvement in the quality of order picking with these two technology systems.
François Milette
VP Supply Chain and Customer Service, Novexco
Transformation and Efficiency with Generix WMS Solution
Since 1922, Shorr Packaging Corp. has established itself as a major player in packaging in the United States. Faced with…
Emballages Carrousel, a leader in packaging solutions, embarked on an ambitious project to modernize its operations and meet the growing…
Work with our team to build your ideal supply chain software stack and tailor it to your unique business needs.