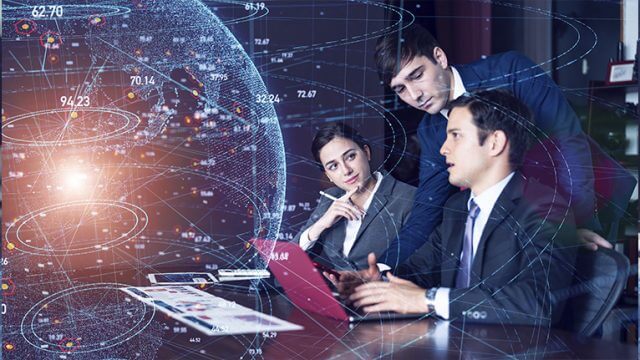
E-Invoicing and Its Geopolitical Stakes
France’s electronic invoicing reform relies on a Y-architecture, where Partner Dematerialization Providers (PDPs) play a central role in issuing and…
Generix Launches Solochain Now – Packaged Solution to Deploy a Complete SaaS WMS in as Little as 16 weeks View the press release
In this blog, we take a quick look at five scenarios that illustrate how the SOLOCHAIN WMS not only improves daily operations on the floor, but also provides management crucial information to help leaders make better decisions. Find out how SOLOCHAIN concretely enables more efficient and cost-effective activities in the warehouse and paves the way to better client experience, sustained growth, and higher margins.
Supply chain operators know the impacts of inventory inaccuracies on profitability. Short of accurate information to manage their stocks and stay ahead of the demand signal, companies are doomed to make poor use of their capacity, suffer from losses, and lose the ability to fulfill orders on time.
A grocer operates a multichannel operation from his distribution center. Employees must deal with replenishment orders for a dozen brick-and-mortar groceries, manage cross-dock transfers, and fulfill and ship customer orders made through the grocer’s eCommerce platform (D2C).
With real time updates that give precise information on every item’s location, and rates of inventory accuracy above 99%, SOLOCHAIN ensures that inventory is easily located and properly handled by employees.
Thanks to automated data exchanges between their ERP system and SOLOCHAIN, handheld scanners that are integrated with the WMS, and a 2D digitized map of their distribution center, the grocer’s employees can rely on accurate inventory data across their entire network and intelligent replenishment suggestions that anticipate on the demand signal.
Businesses in the Food & Beverage industry have to deal with expiration dates, customer specific shelf-life requirements, and traditionally thin margins. Failure to manage fresh and frozen inventory properly can rapidly melt a grocer’s profits.
Take our grocer from the previous scenario: their distribution center has three different temp zones, one of which is a cold storage area. Employees at the dock affected to receiving and transfer tasks must therefore contend with items that must be handled efficiently and expediently to avoid losses. SOLOCHAIN supports employees receiving frozen goods of the environmental conditions that must prevail in every section of a truck before they accept the delivery. Thanks to that information, they can rapidly make sure that all items meet quality standards, which enables them to come to quick and efficient decisions regarding their reception.
In the eventuality that items do not meet the standards, SOLOCHAIN also tells them what steps must be taken to refuse a shipment and inform the system of any and all changes to inventory. Thanks to the WMS, frozen goods are properly handled on the dock and congestions are avoided, preventing operational penalties and costly losses.
Food processing requires that operators pay attention to a variety of details: FIFO across different temp zones, items consumed in a batch, customer shelf-life requirements, etc. To ensure its commercial success, a candy bar processing facility must be able to rely on the right data so that items are consumed at the right time and processed products are efficiently picked and shipped that meet the client’s standards.
SOLOCHAIN supports all activities in the processing facility, from the reception of ingredients to the production of processed goods to shipping the candy. At every step, adaptable mobile workflow and graphical tools are accessible to employees on intuitive, easy to read interfaces. Dashboards provide them the right information to ensure that items are handled properly and efficiently. SOLOCHAIN will, for example, communicate FIFO data to employees picking ingredients, guaranteeing that stocks are efficiently consumed and losses are avoided. It will also inform employees of a client’s shelf-life requirements, making sure that picked items meet their standards and are not returned, which avoids costly penalties.
Meanwhile, SOLOCHAIN affords management granular visibility on crucial information: who is performing what task, details regarding production progress, all inventory modifications in real time, and the status of orders fulfilment. Thanks to intuitive dashboards and detailed reporting capabilities, the SOLOCHAIN WMS enables faster order fulfillment, improved customer satisfaction, and, ultimately, higher margins.
Download WMS SOLOCHAIN Product Sheet Here
While all food manufacturers do their best to steer clear of having to perform recalls, they remain a part of the game. The real differentiator between competing companies is how well recalls are managed. The key, of course, is to achieve recalls that are precise and expedient. By doing so, operators avoid crippling financial penalties and maintain the high service levels that have allowed them to build strong customer confidence over time.
Thanks to its powerful traceability capabilities, SOLOCHAIN informs an ice cream maker of all the items that were consumed in a batch. Moreover, it allows the ice cream maker to rigorously trace each and every one of these items, from vendor to customer. And if that wasn’t enough, the WMS also contains a visual tool that makes it easy for employees on the floor to verify, understand, and comply with FDA regulations.
SOLOCHAIN therefore makes it easy for the ice cream maker to precisely identify which lot of cream was problematic, which batches of ice cream consumed that cream, and which must consequently be recalled. SOLOCHAIN let management know of the exact location of every unit from these batches, enabling them to make precise and efficient recalls. Thanks to SOLOCHAIN, no good ice cream goes wasted!
A brewer delivers its beers across the United States and Canada. From state to state, province to province, the rules relevant to what information must appear on labels are different. Employees must therefore ensure that every shipped case of beer complies with regulations and requirements in the client’s location. When a brewing operation endeavours to deliver efficiently on such a large territory, clerical operations are no longer an option.
SOLOCHAIN is easily integrated with the brewer’s ERP system and labeling software & equipment to support labeling and shipping activities in the warehouse. The WMS acts as hub that automatically relays information to the brewer’s systems and employees regarding a client’s requirements and the laws prevalent in their state or province. The data is thus fed to the labeling software and available on easy-to-read interfaces, which expedites the work of employees fulfilling orders on the floor.
Thanks to significant efficiency gains and a drastically reduced error ratio in their shipments, the brewer achieves higher service levels, which attracts more clients and enables growth.
Generix Group North America provides a series of solutions within our Supply Chain Hub product suite to create efficiencies across an entire supply chain. Our solutions are in use around the world and our experience is second-to-none. We invite you to contact us to learn more.
France’s electronic invoicing reform relies on a Y-architecture, where Partner Dematerialization Providers (PDPs) play a central role in issuing and…
The B2B mandate in Germany, set to take effect on January 1, 2025, marks a crucial step in the European…
Following the October 15 announcement regarding the abandonment of the PPF development, the DGFIP and its partner AIFE are ramping…
Work with our team to build your ideal supply chain software stack and tailor it to your unique business needs.