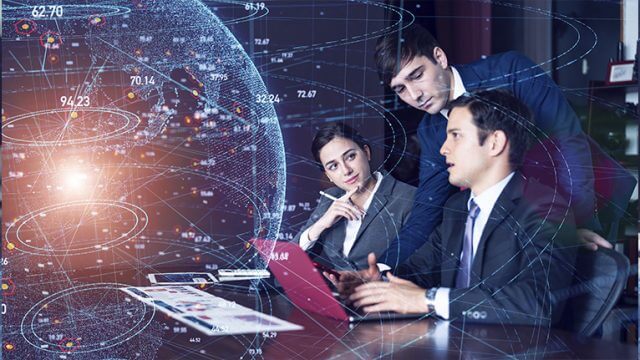
E-Invoicing and Its Geopolitical Stakes
France’s electronic invoicing reform relies on a Y-architecture, where Partner Dematerialization Providers (PDPs) play a central role in issuing and…
Generix Delivers Schematron for Electronic Invoicing to AFNOR to Ensure Interoperability Between PDPs Read the press release
One of the primary benefits of Warehouse Management Systems (WMS) is the significant improvement in operational efficiency. This enhancement is achieved through several key features:
WMS automates many routine tasks such as data entry, inventory management, and order processing. Automation reduces the need for manual labor and minimizes errors. For example, barcode scanning and RFID technology enable real-time data capture, eliminating manual entry and ensuring data accuracy. This automation extends to various warehouse processes, including:
Efficient workflows enabled by WMS streamline various warehouse processes. For instance, the system can prioritize tasks based on urgency and optimize the sequence of operations to avoid bottlenecks. By providing a structured approach to warehouse management, WMS ensures that each task is completed in the most efficient manner possible, reducing idle time and increasing overall productivity.
Accurate inventory management is crucial for maintaining optimal stock levels and meeting customer demand effectively. WMS provides several features to enhance inventory accuracy:
WMS offers real-time visibility into inventory levels, locations, and movements within the warehouse. This capability ensures that inventory records are always up to date, reducing the likelihood of stock discrepancies. Real-time tracking allows for:
By automating data entry and validation processes, WMS minimizes human errors that can lead to inaccurate inventory records. Standardized data formats ensure consistency and reliability, enabling better decision-making and efficient inventory management.
Implementing a WMS can lead to substantial cost savings across various aspects of warehouse operations:
Automation reduces labor costs by minimizing the need for manual data entry and order processing. Employees can focus on more strategic tasks, increasing their productivity and reducing the overall labor required to manage warehouse operations.
Efficient space utilization through optimized storage solutions lowers storage costs and reduces the need for additional warehouse space. WMS helps in organizing inventory in a way that maximizes the use of available space, facilitating easy access and retrieval.
Accurate inventory management helps prevent costly mistakes such as overstocking or stockouts, thus saving on inventory holding costs. By maintaining optimal inventory levels, businesses can avoid the costs associated with excess inventory and reduce wastage due to obsolescence.
Timely and accurate information exchange facilitated by WMS strengthens relationships with suppliers. Real-time updates on order status, inventory levels, and shipment details enable better coordination and communication with suppliers. This improved communication helps build trust and collaboration, leading to more reliable supply chain operations and enhanced supplier performance.
WMS provides real-time updates and acknowledgments, ensuring that all parties are informed and can make timely decisions. This transparency fosters trust and reliability between trading partners, improving the overall efficiency of the supply chain.
Accurate and timely information exchange ensures that suppliers are aware of inventory levels and demand patterns, enabling them to plan their production and deliveries more effectively. This coordination reduces lead times and improves the reliability of supply chain operations.
A WMS significantly enhances customer satisfaction by ensuring accurate and timely order fulfillment. With real-time inventory visibility and efficient order processing, businesses can provide customers with reliable delivery times and accurate order information. Reduced errors in order picking and packing result in fewer returns and complaints, further improving customer satisfaction and loyalty.
WMS ensures that orders are processed and shipped on time, providing customers with accurate delivery estimates and improving their overall experience. Timely deliveries enhance customer satisfaction and build trust in the business.
By reducing errors in order picking and packing, WMS minimizes the occurrence of incorrect or damaged orders. This accuracy leads to fewer returns and complaints, enhancing customer loyalty and satisfaction.
A robust WMS is scalable and can adapt to the changing needs of a business. Whether expanding to new locations, increasing inventory volumes, or managing seasonal order spikes, a scalable WMS can support these changes without compromising performance. This flexibility ensures that the system can grow with the business, providing consistent and reliable support regardless of size or complexity.
WMS can easily accommodate business growth by scaling operations to handle increased volumes and complexities. This scalability allows businesses to expand their operations without the need for significant additional investment in warehouse management infrastructure.
A flexible WMS can adapt to changing business requirements and market conditions. Whether it’s integrating new technologies or adjusting workflows to meet evolving customer demands, a flexible WMS ensures that the business remains agile and competitive.
WMS provides powerful analytics and reporting tools that offer insights into various aspects of warehouse operations. These tools track key performance indicators (KPIs) such as order accuracy, inventory levels, and labor productivity. By analyzing this data, managers can identify bottlenecks, optimize workflows, and make >Labor Cost Reduction: Automation reduces the need for manual data entry and order processing, lowering labor costs.
Yes, a robust WMS is highly scalable and can adapt to the changing needs of a business. It can support the expansion to new locations, increased inventory volumes, and seasonal order spikes without compromising performance. This scalability ensures that the WMS continues to provide consistent and reliable support as the business grows and evolves.
A WMS enhances customer satisfaction by ensuring accurate and timely order fulfillment. Real-time inventory visibility and efficient order processing enable businesses to provide reliable delivery times and accurate order information. By reducing errors in order picking and packing, WMS minimizes returns and complaints, further improving customer loyalty and satisfaction.
France’s electronic invoicing reform relies on a Y-architecture, where Partner Dematerialization Providers (PDPs) play a central role in issuing and…
The B2B mandate in Germany, set to take effect on January 1, 2025, marks a crucial step in the European…
Following the October 15 announcement regarding the abandonment of the PPF development, the DGFIP and its partner AIFE are ramping…
Work with our team to build your ideal supply chain software stack and tailor it to your unique business needs.