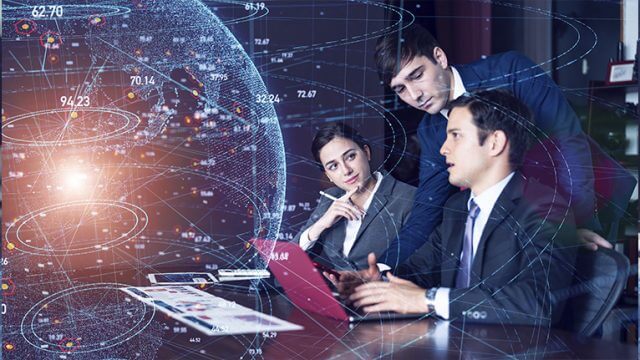
E-Invoicing and Its Geopolitical Stakes
France’s electronic invoicing reform relies on a Y-architecture, where Partner Dematerialization Providers (PDPs) play a central role in issuing and…
Generix Announces the Appointment of Olivier Vaillancourt as General Manager for North America View the press release
A recent DataLab Generix Group assignment with one of the group’s clients demonstrated that disruptions in preparation were the primary factor in decreased productivity. It is therefore essential that preparers never find themselves in a position of having an empty or under-stocked warehouse, unable to meet order demands.
In such a case, they should make an urgent resupply request (which is always possible) and wait for a pallet to be brought down from the reserve in order to finalize the order. If the preparer can switch to another order, the process is not ideal.
To avoid this type of situation, two types of preventive strategies will be used: setting resupply thresholds and anticipating upstream calculations (e.g. from the day before).
Resupply thresholds help to prevent product shortages. A specific setting will trigger a resupply action as soon as a minimum quantity or “resupply threshold” is reached in a picking location.
This is a specific action, which must take into account the capacity of the storage location. Clearly, it is impossible to place two pallets in a location sized for a pallet, but you can probably fit a pallet and a layer of cardboard boxes for example. Because the sizes of the locations, pallets and boxes are saved in the system, calculations are done automatically using simple algorithms that add up the dimensions of objects with a certain margin.
When preparing for upcoming orders, a simulation tool can be used, which is also based on an algorithm. Its role is to simulate a wave of preparation from the order portfolio to be met. It deducts the total quantity needed for each item, verifies the remaining amount in the picking location, and automatically triggers a flurry of resupply missions, targeting orders to be met as quickly as possible.
This transaction can be calculated from the portfolio of orders already received in the WMS, but it can also be based on the forecast data sent by the ERP to the WMS in the form of a dedicated message. For example, warehouse consumption from the last week of a reference period deemed relevant can be used to take into account seasonality or any cyclical business model.
It is also possible to complete picking a day in advance. However, such a strategy can only work if you have time and resources. When operating in a tense flow, selecting truly useful stock replenishments is by far the best approach.
When faced with tense and very high-load periods, WMS algorithms allow for even greater accuracy on the initiation of emergency resupply missions. This will ensure the optimal use of resources, focused on critical needs in real time.
This tool automates resupply management by letting the system trigger replenishments at the most appropriate time, as needed. The system is, of course, based on the theoretical data specific to each warehouse and the type of preparation management present. This algorithmic computational feature will take into account many parameters:
Based on these criteria, which can be prioritized by settings, the system will recalculate the needs of current preparations and set precise timing to initiate resupply. To illustrate the depth of this calculation, we can cite the consideration of elements such as time spent processing orders, changing products, changing aisles, preparing future actions in advance and even time spent on break!
The decision can be made to combine compliance of expiration dates and “date contracts.” In this case, a customizable safety margin is added to the expiration date in order to honor a customer commitment. It is a widespread technique in the field of mass distribution to ensure a certain shelf life, particularly critical for perishable foodstuffs.
This date compliance algorithm can also be applied to all warehouse operations, and is one of Generix Group’s WMS greatest strengths.
This is an essential step in optimizing work planning from a portfolio of orders to be processed. We select orders, or certain elements of an order, and choose a way to effectively manage their processing.
In order to make this selection automatically, we set up “waves” of orders. A wave is a selection from a portfolio, chosen based on several criteria. The primary planning obstacles here are:
As a result, we can put procedures in place that have been inspired by TMS. In this case, we’re referring to “TMS-drawn preparation”.
The manager’s talent lies in his ability to adjust their tools to orchestrate this work according to manageable and adjustable time slots based on the workload of the day and the resources available. Traditionally, planning is done according to a daily or half-day schedule. However, anything is possible depending on the organizational model chosen by the manager. Moreover, it is also possible to choose wave models according to the needs of the given day.
The wave, of which the result represents a list of products to be prepared (or “queue”), is only the first step in the algorithmic calculation. This first calculation is not so much focused on the productivity of operations as on the priority of the orders to be served.
From this list, the system will calculate successive workflows of order groups: generating so-called “missions.” A mission is a to-do list that will be proposed to operators. This raises the question of how to arrange these tasks in a logical way to improve productivity in warehouses. It thus includes numerous parameters, including optimizing preparation routes or triangulation.
France’s electronic invoicing reform relies on a Y-architecture, where Partner Dematerialization Providers (PDPs) play a central role in issuing and…
The B2B mandate in Germany, set to take effect on January 1, 2025, marks a crucial step in the European…
Following the October 15 announcement regarding the abandonment of the PPF development, the DGFIP and its partner AIFE are ramping…
Work with our team to build your ideal supply chain software stack and tailor it to your unique business needs.