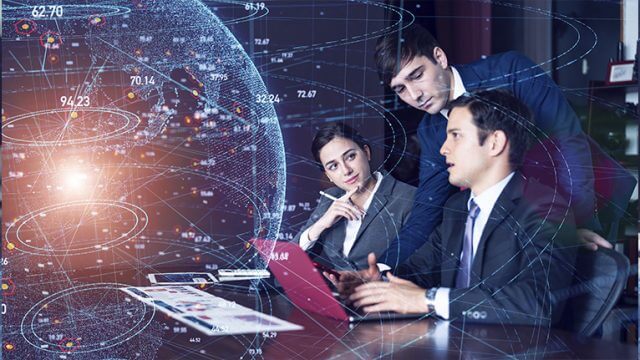
E-Invoicing and Its Geopolitical Stakes
France’s electronic invoicing reform relies on a Y-architecture, where Partner Dematerialization Providers (PDPs) play a central role in issuing and…
Generix Announces the Appointment of Olivier Vaillancourt as General Manager for North America View the press release
SaaS solutions like the SOLOCHAIN WMS have made efficient technology solutions far more affordable than ever before. Nevertheless, a WMS still remains a significant investment to smaller manufacturing companies. However, it’s important to keep in mind that a WMS or ERP’s TOC is not indicative of the system’s actual value – at least, not in and of itself.
Any investment in supply chain infrastructure must be evaluated by relating the TOC to the ROI an operator stands to achieve. It is therefore essential that operators rigorously understand the kinds of savings and gains a given technology solution can yield to make an informed decision regarding its value.
In this paper, we look at five ways manufacturing companies achieve tangible and intangible savings and gains thanks to the SOLOCHAIN WMS.
A coffee roasting, packaging, and distribution company is putting out a great product and garnering the attention of major players the likes of Walmart, Target, and Menards. To benefit from these new revenue streams, the manufacturer must comply with distinct customer requirements, from packaging to labeling to shipping.
With the SOLOCHAIN WMS integrated with its ERP system, the manufacturer can rely on automated compliance processes and ensure that all shipments meet their customers’ requirements. At all stages of the production and distribution cycle, employees are informed of the customer’s requirements through intuitive interfaces on handheld devices or computer stations.
Thanks to these efficiency gains, the manufacturer is able to achieve a throughput that meets the increased demand instead of having to invest in new real estate, new material handling equipment, and a larger labor force.
Some savings generated by the SOLOCHAIN WMS are easily quantified. Others are more intangible, but nevertheless very real.
Most manufacturers these days have trouble attracting and retaining qualified warehouse workers. For a cosmetics manufacturer, this was true before the pandemic hit and it has become a real thorn in their foot today. Labor shortages are now affecting manufacturing and distribution activities to the point where they cannot meet productivity targets. Delays in shipments are having an impact on service levels. Meanwhile, a high turnover rate leads to significant training fees and further operational penalties.
The SOLOCHAIN WMS supports workflows from production processes all the way to shipping. Thanks to clear instructions on intuitive interfaces, activities in the warehouse are more efficient and the cosmetics maker can meet its productivity targets with fewer employees.
Implementing the WMS on handheld devices similar to iPhones and Android platforms, the younger generation of workers find their work environment much more pleasant. This helps the cosmetic maker achieve a higher retention rate, which in turn reduces the training budgets.
By relying on a smaller workforce and retaining more of its employees thanks to an improved work environment, the company can meet its productivity targets and ensure customer satisfaction while saving on labor costs.
The benefits of traceability might be more obvious in the Food & Beverage industry, but the truth is that all manufacturers stand to make important savings by keeping track of the items that go into making what they produce.
Through SOLOCHAIN’s traceability and automated order cycles capabilities, a baseball equipment manufacturer can keep an eye on quantities produced as well as every item consumed in the process. Management can configure the WMS so that it automatically generates POs to procure items once a certain quantity threshold is reached. In that way, SOLOCHAIN ensures that production is never halted because items are missing on the shelves.
With management in charge of determining thresholds, the system also bypasses the risk of human errors, avoiding that too many, or to few items are ordered. This leads to an optimal use of the warehouse’s storage capacity, which saves the baseball equipment manufacturer from having to make unnecessary investments in their physical infrastructure.
Weekly inventory cycle counts force a manufacturer of audio-visual equipment to close areas in the warehouse. This slows down productivity and cuts into the manufacturer’s margins. Thanks to SOLOCHAIN’s inventory management capabilities, the company can save on the costs of long weekly cycle counts.
Once implemented on handheld scanning devices, SOLOCHAIN enables the manufacturer to keep track, in real time, of the quantity and location of every item in the warehouse. While they perform cycle counts, employees are continuously supported in their activities with clear instructions, which drastically cuts down on the time required to complete their tasks.
Today, the manufacturer is attaining inventory accuracy levels of 99.6% and working on eliminating weekly shutdown periods altogether. Thanks to SOLOCHAIN’s support, annual counts can be performed in a single weekend, ensuring that their production of a5. Thinking Ahead: Intelligent Manufacturing audio-visual equipment never misses a beat.
A food processing facility specialises in the production of organic packaged meals that are delivered daily to various organic grocers in the region. Their products are gaining in popularity and demand is on the rise. The number and complexity of customer orders are quickly overwhelming their pen & paper fulfilment processes. The resulting production and shipping errors are now eating at the manufacturer’s profits and affecting customer satisfaction levels.
The SOLOCHAIN WMS facilitates Just-In-Time Delivery through automated full cycle order management. Thanks to the system’s support, order fulfillment at the food service manufacturer is now virtually errorless. Clients are satisfied and demand is on the rise again. Meanwhile, lesser returns lead to lesser losses, which in turn saves the organic meal maker from welting margins.
Generix Group North America provides a series of solutions within our Supply Chain Hub product suite to create efficiencies across an entire supply chain. Our solutions are in use around the world and our experience is second-to-none. We invite you to contact us to learn more.
France’s electronic invoicing reform relies on a Y-architecture, where Partner Dematerialization Providers (PDPs) play a central role in issuing and…
The B2B mandate in Germany, set to take effect on January 1, 2025, marks a crucial step in the European…
Following the October 15 announcement regarding the abandonment of the PPF development, the DGFIP and its partner AIFE are ramping…
Work with our team to build your ideal supply chain software stack and tailor it to your unique business needs.