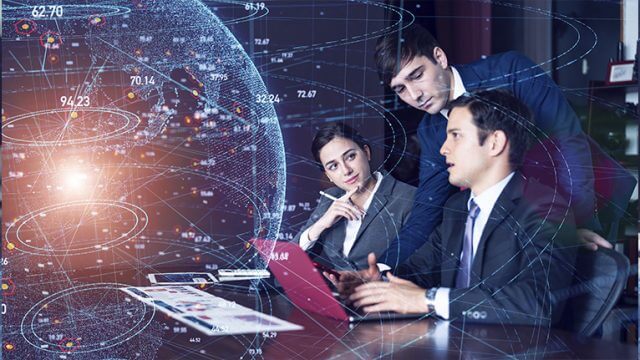
E-Invoicing and Its Geopolitical Stakes
France’s electronic invoicing reform relies on a Y-architecture, where Partner Dematerialization Providers (PDPs) play a central role in issuing and…
Generix Launches Solochain Now – Packaged Solution to Deploy a Complete SaaS WMS in as Little as 16 weeks View the press release
The coronavirus has left no corner of the global economy untouched. The transportation industry in the United States, one of the most accurate leading economic indicators there is, has felt the impact in a major way. For example, in the early going, the impact on long-haul drivers was significant: they faced an acute shortage of washrooms along their routes. Medical scientists and epidemiologists state that the virus can linger on hard surfaces for hours at a time, making public washrooms potential sources of spread and making a tough job even harder.
In other instances, the transportation industry has felt the effects of already-existing trends. Globalization of trade, beginning in the 1990s with the signing of world trade and tariff agreements, has, over the years since, led to extensive off-shore production of raw materials and finished or partially-finished goods. The trucking industry, in particular, has seen a steady drop in volumes and reduced shipments of goods and materials, according to McKinsey.
At the same time, there has been a rise in e-commerce. The ability for consumers to research, select and purchase online has driven online retailers to dramatically improve delivery times, sharply reducing them from weeks to mere days. To make that happen, companies like Amazon, Wal-Mart, and others have built more, smaller, warehouses closer to consumer destinations. This has created another impact on the trucking business; McKinsey’s report on the future of transportation after Covid-19 states that retail shipments under 50 pounds have increased by 5% a year while shipments over 1000 pounds have dropped dramatically along with the average length of haul which has dropped 25% over the last ten years. Of course, the pandemic has caused a huge surge in online shopping; those who have been using the internet to buy what they need and want will continue to do so; those who have discovered online shopping through necessity, are not likely to revert to traveling to bricks and mortar stores to shop, especially with the uncertain timeline regarding the virus. In other words, freight transportation companies will likely see the trends mentioned above continuing.
However, there is a silver lining for the trucking industry. The nature of the virus has meant that social distancing is critical. This, in turn, has led many companies to discover that a large part of their office workforce can perform just as well remotely. Will these office workers return to their offices, post-pandemic (whenever that might be)? Not necessarily. As John Smith, editorial director of Truck News argues in a recent post, “fleets could perform some of the related tasks with less real estate, and recruit personnel who might otherwise look elsewhere because of office locations.” Smith goes on to say that, in order to make such remote work a mainstay of a trucking organization, “managers need to commit to a greater level of communication than ever before.” This is where software technology plays such a critical role. Companies have been traveling at varying rates down a digital path for several years. Covid-19 has made that journey urgent, now, and the need to digitize data is paramount. Digitized data eliminates errors that often occur in spreadsheets, provides the opportunity for everyone in a company to access that data and ensures that updated data is visible to everyone immediately. So, from a need for social distancing, comes the ability to drive efficiencies in an organization that may not have existed before, says Smith.
Transportation is a critical link in the supply chain and the global consultancy firm, Bain and Company, believes that digital transformation is vital today to maintain supply chain resilience. Bain argues that the shock to supply chains created by Covid-19 is far from an isolated event. In a recent report on the pandemic’s impact on supply chains, the firm points to the trade tensions between the U.S. and China, Brexit in Europe, and natural disasters like Hurricane Sandy as indicators of the need for resilience in the supply chain. “Bain analysis shows that companies with resilient supply chains grow faster because they can move rapidly to meet customers’ needs when market demand shifts. They increase their perfect order rate by 20% to 40% and customer satisfaction by as much as 30%. Importantly, flexible supply chains cut costs and improve cash flow, in part through a 10% to 40% increase in inventory turns. Finally, leaders reduce disruption by building buffers throughout the supply network and invest in advanced analytics to improve planning and forecasting accuracy,” says their report. So, once again, the key to regaining and retaining business during and after the pandemic lies with technology. The transportation industry is key to efficient supply chain management and cannot afford to exclude digital technologies without becoming the “weak link” in the chain but, as we’ve seen, transportation companies have plenty to gain, themselves. Generix Group North America has created a digital solution tailored for the transportation industry. Its Transportation Management System is designed to provide that critical, centralized view throughout an organization. The software platform contains features like automatic load consolidation and carrier chartering and provides a complete management system that can deliver efficiencies otherwise unattainable without the use of such digital technology. While the pandemic continues to suppress both global demand and supply for the time being, transportation companies are not without the ability to sustain their business and be positioned and ready to take advantage when economic conditions begin to improve. As Bain concludes in its study, “cloud-based supply chain applications and collaborative platforms and tools enhance information sharing. They also improve the quality and speed of decision making within an organization and with suppliers and other external partners in a secure environment.”
France’s electronic invoicing reform relies on a Y-architecture, where Partner Dematerialization Providers (PDPs) play a central role in issuing and…
The B2B mandate in Germany, set to take effect on January 1, 2025, marks a crucial step in the European…
Following the October 15 announcement regarding the abandonment of the PPF development, the DGFIP and its partner AIFE are ramping…
Work with our team to build your ideal supply chain software stack and tailor it to your unique business needs.