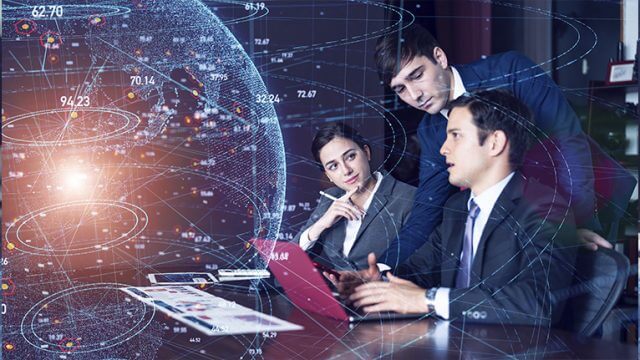
E-Invoicing and Its Geopolitical Stakes
France’s electronic invoicing reform relies on a Y-architecture, where Partner Dematerialization Providers (PDPs) play a central role in issuing and…
Generix Delivers Schematron for Electronic Invoicing to AFNOR to Ensure Interoperability Between PDPs Read the press release
“Of the many structural changes that have happened within the logistics industry during the COVID-19 pandemic, strict adherence to social distancing has become one of crucial significance,” Freightwaves reports, noting that social distancing is “easier said than done” within supply chains, where logistics workers tend to work in crowded spaces. “But with isolated working conditions becoming necessary, businesses are looking to introduce a variety of measures, including staggered work schedules and greater automation.”
Busy spaces that have grown in complexity over the last few years, warehouses and distribution centers (DCs) are vital arteries that manufacturers, retailers, distributors, and end customers all rely on to get products from point A to point B. As we saw during the early weeks of the global pandemic—when companies were caught off guard by huge upticks in demand for essential goods—warehouses transformed into “front-line workers” to help ensure continuity of supply.
“As an operations or facilities manager,” Kardex Remstar states, “you are now faced with the task of assessing your current processes, reducing employee contact and interaction, and adjusting to the changing guidelines from the Centers for Disease Controls and Prevention (CDC) to reduce the threat of exposure to COVID-19.”
Adjusting a facility to accommodate these changes can be quite an undertaking, with social distancing being just one of the long-term effects of COVID on manufacturing, distribution, logistics, and supply chains globally.
“If you haven’t already, now is the time to start thinking about how to adapt your warehouse to accommodate this ‘new normal,’” advises Kardex Remstar, which tells companies to use automation to separate workstations and deploy touch-free order consolidation processes. “With the right design, even large consolidation areas can be managed by only one person to encourage social distancing.”
For warehouses that were already using technology, automation, and robotics before COVID reared its head, the spike in demand was somewhat easier to manage. Facilities that could continue operating with skeleton staffs, and in the midst of mandated shutdowns, proved their value on many different levels. As employees returned to work, they were immediately asked to practice social distancing—something that’s not easy to attain with a full workforce operating on a warehouse or DC floor.
This is because the need to reduce the number of touches on items, boxes, or pallets goes beyond just adhering to the new rules in our “new normal” operating environment. Borrowing a page from Toyota’s “lean” operating approach, fewer touches also reduce the risk for errors, cut down on the number of extra steps needed to complete a task, and reduce worker fatigue.
Fewer touches also means less product damage. The more times an item is handled, the better the chances that it will be damaged, misplaced, or misdirected. Using directed workflows, scheduled fulfillment plans, status notifications, and other functions, WMS and other advanced technologies can help companies significantly cut down the number of touches needed to fulfill an order.
There’s also the danger of an item being misplaced or inaccurately packed due to a misread of a label (or someone simply forgetting where to place the carton). Even one misplaced item can hold up an entire order and send a team of workers into a tailspin as they try to hunt the item down.
Improving warehouse efficiency in today’s fast-paced operational environment requires advanced technology. Software continues to play a key role in every company’s mission of working smarter, better, and faster, with warehouse management systems (WMS) leading the charge in helping companies improve efficiencies while adhering to new workplace regulations.
“Every WMS discussion comes back to improving warehouse efficiency. That’s the software’s biggest claim to fame and the greatest potential,” independent supply chain resource Explore WMS explains. “It’s where most [companies] will find their savings or even discover an ability to expand and better serve customers.” With its advanced functionalities and advanced capabilities, WMS also helps companies significantly reduce the number of touches needed before an order can be shipped out the door. This, in turn, helps to reduce fulfillment operation complexity, decrease errors, and improve efficiencies.
France’s electronic invoicing reform relies on a Y-architecture, where Partner Dematerialization Providers (PDPs) play a central role in issuing and…
The B2B mandate in Germany, set to take effect on January 1, 2025, marks a crucial step in the European…
Following the October 15 announcement regarding the abandonment of the PPF development, the DGFIP and its partner AIFE are ramping…
Work with our team to build your ideal supply chain software stack and tailor it to your unique business needs.