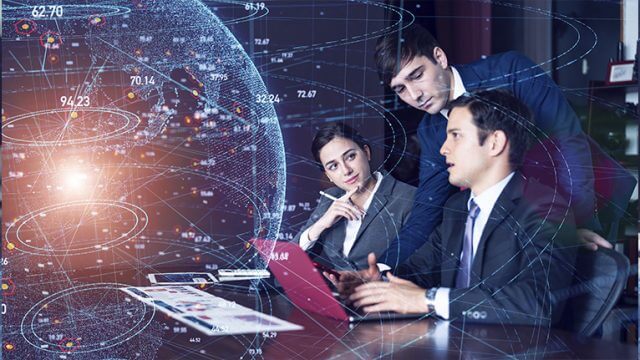
E-Invoicing and Its Geopolitical Stakes
France’s electronic invoicing reform relies on a Y-architecture, where Partner Dematerialization Providers (PDPs) play a central role in issuing and…
Generix Delivers Schematron for Electronic Invoicing to AFNOR to Ensure Interoperability Between PDPs Read the press release
It’s been argued that the main reason distribution centers (DC) suffer labor shortages more than other types of businesses is because the new generation of employees is just not inclined to work in that type of environment. Again, the Department of Labor Statistics seems to support this: data shows that the average tenure of individuals between the ages of 18 and 24 is somewhere around 1.1 years.
There’s no denying that generational differences partially explain why supply chain operators struggle to attract and retain new employees. Kids who were born the same year as the first iPhone was released are likely more foreign to a warehousing environment than previous generations. Raised in a digital world, these kids also have different expectations as to what a workplace should look like. In their efforts to attract new workers, employers would do well to be attuned to those expectations.
Having said that, no matter how “cool” companies make their DC—through gamification, for example—, one simple fact remains:
Warehousing jobs are physically demanding. Workers on the floor walk miles and miles every day—more than 9 miles in a day is not uncommon. Automated environments may cut down on walking, but then employees are often called to stand at their station for 8, 9, or 10 hours a day. What’s more: automated environments can exacerbate another pain point: task repetitiveness.
Unappealing work schedules also make it difficult to attract new employees. Distribution centers regularly run all day and all night, seven days a week. More often than not, the unpopular shifts fall to the new guys. To no one’s surprise, not everybody is willing to pull night shifts and weekends, even when the pay is a bit better.
DC operators are under constant pressure to achieve higher throughputs with fewer workers on the floor and new supply chain disruptions every other week. Unsurprisingly, some of that pressure is passed down to employees, which creates a stressful working environment. When overburdened workers are pulling more hours on the floor than they should, they become more likely to call in sick or, worse, cut corners and risk injuries, which of course leads to further shortages—DC managers working in industries that were designated as “essential” during the Covid crisis are probably having painful flashbacks at this point.
It’s no secret that the scarcity of warehouse workers has sped up the automation of DCs and fulfillment centers. Companies that can afford it have responded to labor shortages by leveraging mobile robots to shuttle goods across their facilities, robotic arms to handle goods and boxes, and intelligent tracking and conveyor systems. Amazon, to no surprise, stands out as a prime example. So does Kroger, in the F&B industry, who has recently invested in Ocado’s automated fulfilment centers in a plan to deploy 20 across the nation over the coming years.
Small- and Medium-Sized businesses (SMBs) generally do not have the capital for the high initial expenditure required to implement such solutions. Meanwhile, fast-growing companies need to prioritize operational flexibility to ensure that they can scale their processes efficiently without losing control of their budget—fully automated environments are typically very rigid.
Whether robots are on your company’s digital roadmap or not, a Warehouse Management System (WMS) is the first solution companies must implement to alleviate the pains caused by labor shortages.
A WMS is an efficient and far more affordable technology solution for companies to reduce their dependence on a large workforce. What’s more, a WMS can also help DC operators attract and retain employees by improving the quality of the working environment.
Implementing a WMS is an absolute necessity for operators looking to automate processes and implement inventory management best practices in their DC. More than a window on inventory levels, a decent WMS gives companies the means to optimize workflows and task assignments, which in turn empowers them to improve their operation’s capacity with a smaller workforce. A well configured WMS will, for instance, reduce walking distances and minimize motion waste by maximizing the value of every step taken by workers on the floor, enabling operators to augment throughput with fewer resources.
DC operators can integrate their WMS with mobile platforms, such as iPads or other handheld touchscreen devices. Workers on the floor then benefit from system support on intuitive interfaces as they perform their tasks without wasting time—and energy—having to return to a computer station.
Thanks to these features, a WMS also helps with the onboarding of new employees. Managers by and large report that it’s easier and faster (which also means: cheaper) to train new workers when leveraging a WMS that provides them clear instructions and a map to navigate the DC.
End-users generally enjoy working with electronics. The younger generation, well trained in the ways of the handheld device, sees it as a clear improvement to a DC’s working environment. A WMS not only cuts down on the time needed to complete their work, it also gives them the sense of being more independent, more accurate, and more productive.
Far more accessible than a fully automated distribution infrastructure, and a necessary condition to the implementation of warehouse management best practices, a WMS stands as a powerful solution to DC operators looking to overcome their labor shortages woes.
France’s electronic invoicing reform relies on a Y-architecture, where Partner Dematerialization Providers (PDPs) play a central role in issuing and…
The B2B mandate in Germany, set to take effect on January 1, 2025, marks a crucial step in the European…
Following the October 15 announcement regarding the abandonment of the PPF development, the DGFIP and its partner AIFE are ramping…
Work with our team to build your ideal supply chain software stack and tailor it to your unique business needs.