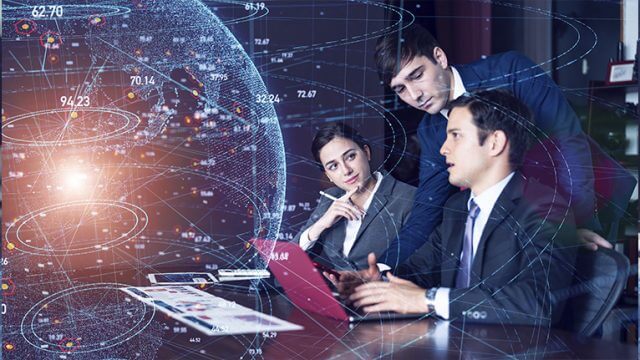
E-Invoicing and Its Geopolitical Stakes
France’s electronic invoicing reform relies on a Y-architecture, where Partner Dematerialization Providers (PDPs) play a central role in issuing and…
Generix Delivers Schematron for Electronic Invoicing to AFNOR to Ensure Interoperability Between PDPs Read the press release
At its core, WMS inventory management involves utilizing advanced software tools to monitor, control, and optimize the flow and storage of goods within a warehouse. This includes tasks from receiving goods to their eventual shipment, while ensuring accurate tracking and management of stock levels throughout the process.
The process starts with the receipt of goods into the warehouse. A WMS system facilitates the swift and accurate recording of incoming inventory, including details such as quantity, type, and storage requirements. This ensures a smooth transition of goods into the warehouse, maintaining a real-time overview of stock levels.
Once goods are received, determining their optimal placement within the warehouse is crucial. WMS inventory management systems employ algorithms to suggest the best storage locations based on various factors, including the frequency of access, size, weight, and compatibility with other items. This strategic placement significantly enhances retrieval efficiency and maximizes the use of available space.
Picking, packing, and preparing orders for shipment are streamlined through a WMS. The system generates optimized pick lists that guide warehouse staff through the most efficient routes, reducing picking errors and speeding up the order fulfillment process. Advanced systems can also automate parts of this process through robotics and conveyor systems, further enhancing efficiency.
One of the cornerstone features of WMS inventory management is its ability to maintain rigorous control and tracking of stock levels in real-time. Through the use of barcodes, RFID tags, and other tracking technologies, a WMS provides visibility into the exact location and quantity of every item within the warehouse. This capability is instrumental in preventing stockouts, reducing excess inventory, and enabling accurate forecasting.
WMS solutions come equipped with powerful analytics and reporting tools that offer insights into warehouse operations. By analyzing data on inventory turnover, order fulfillment times, worker productivity, and more, businesses can identify areas for improvement, forecast future needs, and make informed decisions to optimize warehouse operations.
For maximum operational efficiency, WMS inventory management systems often integrate with other business management systems such as Enterprise Resource Planning (ERP) systems, Transportation Management Systems (TMS), and Customer Relationship Management (CRM) platforms. This integration ensures seamless data flow across different business functions, enhancing coordination and strategic planning.
Inventory Management and Warehouse Management Systems (WMS) are crucial components of supply chain management, but they focus on different aspects of storage and distribution. Understanding the distinctions between them is essential for optimizing operations within a warehouse or distribution center.
Inventory Management focuses on tracking and managing the quantities of goods a company has in stock. Its primary goal is to ensure that there is enough inventory to meet demand without resulting in surplus. Key functions include:
Warehouse Management System (WMS), on the other hand, offers a broader range of functionalities aimed at optimizing the entire operations within a warehouse or distribution centers. While it includes inventory management capabilities, it also extends to areas such as:
Deciding whether to implement an inventory management system or a WMS depends on the complexity of your warehouse operations, the size of your operation, and specific business needs. Smaller businesses with simpler operations might find that inventory management software meets their needs. In contrast, larger enterprises with complex warehousing operations could benefit significantly from the comprehensive features offered by a WMS.
Incorporating WMS into inventory management practices offers unparalleled advantages, from elevating inventory accuracy to streamlining warehouse operations and improving customer satisfaction. As the logistics and supply chain landscape continues to evolve, leveraging advanced WMS technology will remain central to achieving operational excellence and competitive advantage.
France’s electronic invoicing reform relies on a Y-architecture, where Partner Dematerialization Providers (PDPs) play a central role in issuing and…
The B2B mandate in Germany, set to take effect on January 1, 2025, marks a crucial step in the European…
Following the October 15 announcement regarding the abandonment of the PPF development, the DGFIP and its partner AIFE are ramping…
Work with our team to build your ideal supply chain software stack and tailor it to your unique business needs.