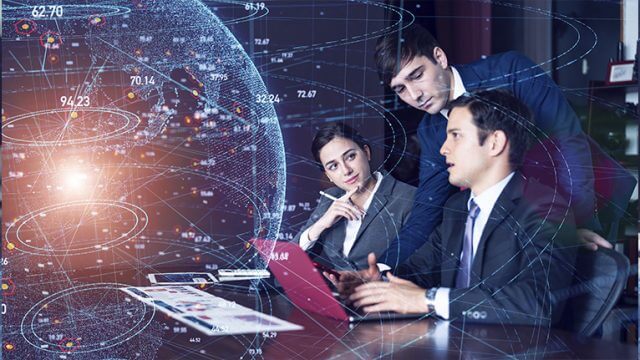
E-Invoicing and Its Geopolitical Stakes
France’s electronic invoicing reform relies on a Y-architecture, where Partner Dematerialization Providers (PDPs) play a central role in issuing and…
Generix Delivers Schematron for Electronic Invoicing to AFNOR to Ensure Interoperability Between PDPs Read the press release
In its annual barometer (FR version) based on data from 671 companies and more than 350,000 employees, Gras Savoye Willis Towers Waston confirms that absenteeism has risen sharply and steadily over the last five years, particularly in SMEs and SMIs. If the first lockdown had an obvious impact, it is far from being the only explanation. While the “transport and logistics” category now holds the second place of the sectors, most affected by this phenomenon, the study reminds us that the average cost of absenteeism in a company of 1,000 employees varies between 1.5 and 3 million euros per year. The weight of logistics activities in this loss of earnings is considerable. Given the increasing risks of delays and shutdowns in the supply chain due to lack of manpower, here are three tips for taking concrete action on absenteeism.
7,97 % is the rate of absenteeism in 2020 in the transport and logistics sector, compared with an average of 5.04% in France.
As well as remuneration or benefits offered by the company, the quest for meaning is now well known as a major lever of commitment at work. But how to motivate employees when the tasks they are assigned are by definition simple and repetitive? As a manager in the
logistics sector, taking the time to regularly explain the stakes and the purpose of your job to each employee, and being able to give them tangible and personalized feedback on the impact of their work, is a way to give meaning to low-skilled logistics functions. Knowing which customer profile is targeted at the end of the process, having details on the products handled and on the marketing promise, knowing and understanding all the other technical steps upstream and downstream of one’s intervention… This type of information will help everyone to understand their role in the supply chain and therefore to make the teams individually and collectively responsible.
Today, integrated HR tools and advanced warehouse management solutions offer a comprehensive view of ongoing operations and are likely to provide data and visibility to managers. The Resource Management module of Generix Group’s WMS, which will be launched in 2022, will also avoid repetitiveness in task allocation, encouraging employee multitasking. Powered by artificial intelligence and fed with real-time data, this type of resource management and planning tools are new allies in preventing absenteeism.
Implementing voice command devices for operators or equipping them with exo-skeletons is a way to limit strenuous movements and loads carried, thus reducing the risk of musculoskeletal disorders. Some companies are even starting to equip themselves with ‘cobots‘, these robotic collaborative assistants that help employees prepare orders and reduce their movements.
Used wisely, these tools have the dual benefit of reducing the risk of sick leave and work accidents while optimizing overall performance in the warehouse.
Sometimes alone at their workstations, with no real possibility of communicating with their colleagues for long hours, supply chain operators can legitimately feel isolated. Keeping them motivated is a daily challenge for managers and HR. Gamification is one way to encourage commitment, pride of belonging and team concentration. For example, it is a matter of organizing interactive performance contests, between peers or between teams, aiming at collecting a maximum of points to obtain symbolic or material rewards. Or measuring the quantity of plastic recycled by each person, with rewards at stake. These challenges can also encourage employees to follow professional training courses or to respond to co-optation campaigns. These initiatives contribute indirectly to the fight against dropping out of the workforce and absenteeism.
France’s electronic invoicing reform relies on a Y-architecture, where Partner Dematerialization Providers (PDPs) play a central role in issuing and…
The B2B mandate in Germany, set to take effect on January 1, 2025, marks a crucial step in the European…
Following the October 15 announcement regarding the abandonment of the PPF development, the DGFIP and its partner AIFE are ramping…
Work with our team to build your ideal supply chain software stack and tailor it to your unique business needs.