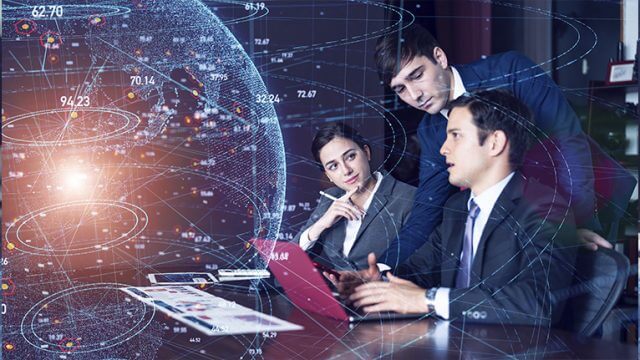
E-Invoicing and Its Geopolitical Stakes
France’s electronic invoicing reform relies on a Y-architecture, where Partner Dematerialization Providers (PDPs) play a central role in issuing and…
Generix Launches Solochain Now – Packaged Solution to Deploy a Complete SaaS WMS in as Little as 16 weeks View the press release
If you’re operating a small business with a very limited number of SKUs, it’s possible that spreadsheets can still be used to keep track of stock in the warehouse. The fact remains, however, that spreadsheets are inconvenient to update and simply cannot give you an accurate indication of current inventory numbers. With a warehouse management system you can automate inventory management and do away with spreadsheets. A WMS allows you to keep on top of quantities and maintain visibility on all items, down to location, in real-time.
When items begin to outgrow their location and crowd the aisles, companies are often inclined to think it’s time to relocate to a larger facility. However, moving is expensive and the process can slow down operations to a grind, affecting revenues and customer satisfaction. By implementing warehouse management best practices, companies can augment their distribution center’s capacity without having to relocate. A WMS can, for instance, optimize item locations and streamline workflows to help companies improve their throughput without the need for additional space.
A cluttered environment threatens more than the efficiency of your workflows. When items and equipment clog the aisles, inventory is at risk of being destroyed or misplaced and your workers’ safety is jeopardized. To avoid these dangers and prevent bottlenecks, employees must be accurately informed of every product’s location and able to take the optimal pick path. A WMS will assist you in arranging your inventory in the safest and most efficient manner possible and in optimizing picking tasks.
It’s impossible for your distribution center to meet demand if your organization is unable to forecast sales. When customers are repeatedly frustrated because items are out-of-stock, this reflects poorly on your company’s reputation. And when items finally come in, employees are so busy trying to catch up that productivity suffers: everyone is dealing with backlog orders instead of working with the flow of new orders. Warehouse management systems are an essential tool to accurately forecast sales and optimize channel management.
A chaotic distribution center leads to slower order fulfillment. When picking and packing activities take longer than they should, either orders fail to be shipped on time, or your organization has to throw more labor at the task to make sure products are delivered to customers as promised—which of course comes with a hefty financial penalty. A WMS will help you simplify your operations, streamline workflows, and fulfill orders on time so that you may keep your promises and increase customer satisfaction.
Your distribution center must grow in tandem with the rest of your company. Any warehousing delays prevent your company from expanding its market reach and earnings. Remember that during peak seasons, when the potential for maximum earnings is at its greatest, even the smallest warehouse management issue will become a real thorn in your side. If one of the telltale signs listed above sounds familiar, do not delay; implement solutions to ensure your company’s productivity when it matters most.
France’s electronic invoicing reform relies on a Y-architecture, where Partner Dematerialization Providers (PDPs) play a central role in issuing and…
The B2B mandate in Germany, set to take effect on January 1, 2025, marks a crucial step in the European…
Following the October 15 announcement regarding the abandonment of the PPF development, the DGFIP and its partner AIFE are ramping…
Work with our team to build your ideal supply chain software stack and tailor it to your unique business needs.