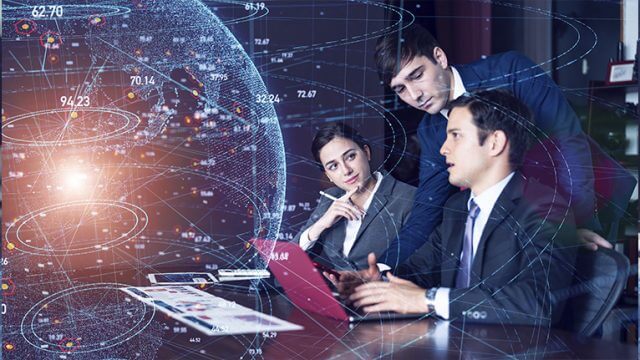
E-Invoicing and Its Geopolitical Stakes
France’s electronic invoicing reform relies on a Y-architecture, where Partner Dematerialization Providers (PDPs) play a central role in issuing and…
Medial International Chooses Generix Warehouse Management System (WMS) to Digitalize Its Logistics Operations Read the press release
While risk management is a very large component of supply chain management, there are also other factors to take into account, such as client specific needs and requirements, evolving digital technology, increasing competition, and other logistics such as high production at lower costs, or even a company’s ecological impact. A supply chain is no longer a simple way to get a product from one place to another; it is a strategic part of any business, and one that requires a high level of optimization and forward-thinking.
At Generix Group, we are continuously developing innovative solutions to help our clients manage risk, evolve, adapt and collaborate in a way that reinforces productivity and efficiency while subsequently reducing costs. A supply chain needs to be efficient, reliable and resilient.
Just as there is no risk-free supply chain, there is also no one-size-fits-all platform or solution. When Isover approached Generix Group with a list of requirements, we jumped at the chance to work with them on creating a one-of-a-kind solution. TMS solution would not only help Isover optimize their supply chain management process, but also ensure they meet their environmental commitments amongst other items.
Isover is the world leader in thermal and acoustic insulation and fire protection, with a large global network of suppliers, distributors, and clients. A company of this size and importance requires a manageable and highly functional supply chain management system.
Isover was looking for a solution that could literally revolutionize their aging system. Their requirements were very specific and included a variety of updates, including the revamping of their transportation system, a more seamless way to manage production and storage sites, faster turn-around and processing times, improved routes and networks as well as a complete optimization of tariffs. In addition, these requirements included a system that could easily adapt to and evolve with the major changes in Isover’s transport purchasing policies and significantly reduce their carbon footprint. This was a tough challenge, especially since Isover has over 60,000 trucks on the roads every year. However, it was a challenge that Generix Group was prepared to take by the horns.
We developed an innovative solution that completely changed how the entire Isover team works from the inside out. A two-phase installation period was set up in order to integrate modules that were specifically adapted to Isover’s logistical activities. The end result is the creation of a much more highly functional, intuitive and user-friendly workflow and process, along with a rapid deployment and pain-free integration. Our super responsive customer support hotline continues to provide hands-on solutions at any level, and we also implemented an automatic pre-invoicing system. In addition to a more hospitable internal system, Isover’s entire transportation set-up has been completely overhauled, with the optimization of both vehicles and routes, including the addition of charter agreements and better tracking techniques.
France’s electronic invoicing reform relies on a Y-architecture, where Partner Dematerialization Providers (PDPs) play a central role in issuing and…
The B2B mandate in Germany, set to take effect on January 1, 2025, marks a crucial step in the European…
Following the October 15 announcement regarding the abandonment of the PPF development, the DGFIP and its partner AIFE are ramping…
Work with our team to build your ideal supply chain software stack and tailor it to your unique business needs.