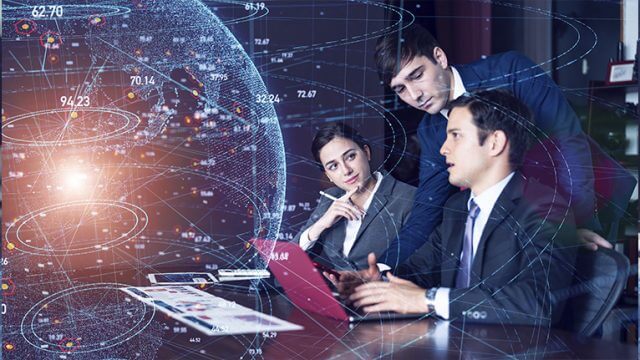
E-Invoicing and Its Geopolitical Stakes
France’s electronic invoicing reform relies on a Y-architecture, where Partner Dematerialization Providers (PDPs) play a central role in issuing and…
Generix Launches Solochain Now – Packaged Solution to Deploy a Complete SaaS WMS in as Little as 16 weeks View the press release
In charge of using a management software to plan logistic operations, managers spend a lot of time in their offices working from a computer. As such, they cannot be present in the warehouse, working side by side with their teams. This physical distance between managers and teams can result in communication problems and thus impaired warehouse productivity.
To tackle this issue, team managers need access to warehouse management tools in order to interact with their teams while managing their tasks. A mobile WMS solution does just that by placing warehouse mobility at the core of its objectives. It provides managers with a smartphone or tablet application so they can plan warehouse operations while being in closer contact with their teams.
Read also: Opt for a collaborative approach to inventory management with a VMI software
A WMS (Warehouse Management System) enhances warehouse management by supporting a growing number of product references, organizing inventory and preparing orders based on different methods. All this, while significantly cutting operation costs.
Available in smartphone/tablet app format, a WMS allows the team manager to connect to the software wherever and whenever he needs to. Goals:
At the heart of the collaborative approach, a mobile WMS repositions managers and places them by their teams’ side so they can solve any problem and provide real time solutions. It also allows managers to anticipate anomalies and maintain a constant balance between loads and logistical resources.
On the same topic: Two indicators to follow for a better managed warehouse
Generix Group developed a custom application to meet the needs of a large food distributor. The goal was to modernize processes while improving the warehouse mobility, to make the manager of operations closer to the team on the workfield. Stemming from this collaboration was the creation of a proof of concept (POC) to test the feasibility of a mobile extension for the Generix warehouse management solution. The following objectives were set:
The project ended in genuine success. By integrating all the features of a traditional WMS as well as data visualization, the mobile application developed and tested by Generix Group brought the manager of warehouse operations closer to his teams, thus enhancing the effectiveness of his actions in real time.
France’s electronic invoicing reform relies on a Y-architecture, where Partner Dematerialization Providers (PDPs) play a central role in issuing and…
The B2B mandate in Germany, set to take effect on January 1, 2025, marks a crucial step in the European…
Following the October 15 announcement regarding the abandonment of the PPF development, the DGFIP and its partner AIFE are ramping…
Work with our team to build your ideal supply chain software stack and tailor it to your unique business needs.