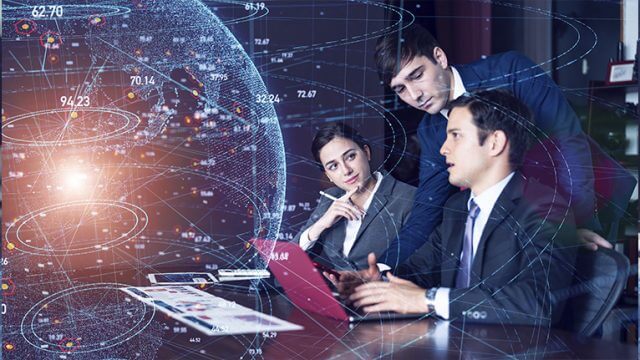
E-Invoicing and Its Geopolitical Stakes
France’s electronic invoicing reform relies on a Y-architecture, where Partner Dematerialization Providers (PDPs) play a central role in issuing and…
Generix Delivers Schematron for Electronic Invoicing to AFNOR to Ensure Interoperability Between PDPs Read the press release
A Warehouse Management System is specialized software that helps manage and control various warehouse functions. These systems provide real-time insights into inventory levels, order status, and the movement of goods. They also help in planning the use of resources, such as labor and space, and optimize the flow of goods from receiving to shipping.
At its core, a WMS handles the day-to-day operations of a warehouse. It coordinates key processes like inventory tracking, picking and packing orders, shipping, and returns management. Depending on the complexity of the warehouse, a WMS can range from a simple inventory control system to a comprehensive suite that handles multiple warehouses and integrates with other enterprise resource planning (ERP) software.
A Warehouse Management System performs several essential functions that help streamline operations and enhance productivity. These core functions ensure that every aspect of warehouse activity, from receiving to shipping, is optimized for efficiency. Here are the main functions of a WMS:
These functions combine to ensure a smooth flow of operations, enabling businesses to scale effectively and maintain high levels of customer satisfaction.
A WMS coordinates multiple processes that are critical to warehouse operations. Each process has specific features that make warehouse management more efficient. Below are the key processes and their corresponding features:
One of the most important roles of a Warehouse Management System is inventory management. Accurate inventory tracking is vital to avoid stockouts or overstocking. WMS software uses real-time data to track inventory as it enters, moves through, and leaves the warehouse. This ensures that the exact location of every product is known at all times, reducing errors and improving fulfillment speed.
By using technologies such as barcoding, RFID, and QR codes, WMS systems can track individual items or batches. This level of tracking minimizes human error, allowing businesses to maintain accurate stock counts and easily identify discrepancies.
When new inventory arrives at the warehouse, it must be efficiently received and stored. A WMS streamlines this process by guiding workers through the receiving and putaway process. It verifies that incoming goods match the purchase order and suggests optimal storage locations based on factors like product type, size, and demand.
The system may even automate the assignment of storage space, ensuring that products are placed where they are most accessible for future use. By automating this process, a WMS can reduce the time spent receiving and storing items, leading to more efficient use of warehouse space and labor.
Order picking is a critical component of fulfilling customer orders, and a WMS ensures that this process is accurate and efficient. The system can generate picking lists and direct workers to the exact location of items in the warehouse. Depending on the type of WMS, it may support different picking methods, such as wave picking, batch picking, or zone picking, to further optimize the process.
The accuracy provided by a WMS reduces the risk of picking errors, leading to higher customer satisfaction and fewer returns. Moreover, by guiding workers on the most efficient routes through the warehouse, the system helps reduce the time it takes to complete orders.
Once an order is picked, the packing process begins. A WMS ensures that the right items are packed in the correct packaging to prevent damage during shipping. It may also help calculate the optimal packing configuration to save on shipping costs.
For shipping, the WMS often integrates with carrier systems to automate label generation and tracking. This ensures that the correct shipping labels are applied, and customers receive their orders as quickly and cost-effectively as possible.
Returns are an inevitable part of any retail or distribution operation. A robust WMS simplifies returns management by automating the process of receiving, inspecting, and restocking returned items. The system can flag returned products for quality checks and ensure they are either returned to inventory or discarded based on their condition.
By efficiently managing returns, a WMS reduces the labor costs associated with handling returned items and helps maintain accurate inventory levels.
A WMS works by automating and coordinating all warehouse activities to ensure smooth operations. It interacts with hardware such as barcode scanners, RFID tags, and mobile devices to track products as they move through the warehouse. A WMS is configured to manage tasks such as receiving inventory, directing putaway, generating picking lists for orders, packing, and managing shipments.
By utilizing real-time data, a WMS ensures accurate inventory control and order fulfillment. The system operates continuously to keep warehouse managers informed of any delays, discrepancies, or issues, allowing them to make quick adjustments.
A WMS is most effective when integrated with other systems, such as Enterprise Resource Planning (ERP) and Transportation Management Systems (TMS). Integration allows for better coordination across the supply chain, improving overall operational efficiency.
By automating many manual processes, a WMS boosts warehouse efficiency. Workers spend less time searching for inventory or figuring out the next task, and more time fulfilling orders. This leads to faster turnaround times and reduced labor costs.
A WMS improves accuracy at every stage of warehouse operations. From inventory tracking to order picking, the system minimizes errors, which can lead to increased customer satisfaction and fewer costly mistakes.
Real-time visibility into inventory levels is one of the most important advantages of using a WMS. By having up-to-date information on stock levels, businesses can avoid overstocking or running out of products, both of which can negatively impact profitability.
A WMS helps optimize the use of warehouse space by recommending the most efficient storage locations for items. This reduces the likelihood of wasted space and makes it easier to locate products when needed.
As a business grows, its warehousing needs become more complex. A scalable WMS can grow alongside the company, supporting new processes, additional warehouses, and higher volumes of inventory without a decline in performance.
When selecting a WMS, it’s important to consider the specific needs of your business. Factors like the size of your operation, the complexity of your supply chain, and the types of products you manage will all influence your decision. Additionally, ease of integration with existing systems and the ability to scale as your business grows are key considerations.
A cloud-based WMS may be particularly attractive for businesses looking for flexibility and lower upfront costs. These systems offer the advantage of easy scalability and remote accessibility, making them a great option for businesses with multiple locations or those that anticipate future growth.
A Warehouse Management System (WMS) is crucial for businesses aiming to streamline operations, boost inventory accuracy, and enhance overall efficiency. By automating core processes like order fulfillment, inventory tracking, and shipping, a WMS ensures smoother workflows, reduces errors, and enables scalability as your business grows. Implementing the right WMS can transform your warehouse, unlocking new levels of productivity and positioning your company for sustained success in a competitive market. For those seeking a comprehensive, advanced solution, the Generix Solochain WMS offers a flexible, cutting-edge platform that optimizes warehouse management while integrating seamlessly with your broader supply chain strategies.
France’s electronic invoicing reform relies on a Y-architecture, where Partner Dematerialization Providers (PDPs) play a central role in issuing and…
The B2B mandate in Germany, set to take effect on January 1, 2025, marks a crucial step in the European…
Following the October 15 announcement regarding the abandonment of the PPF development, the DGFIP and its partner AIFE are ramping…
Work with our team to build your ideal supply chain software stack and tailor it to your unique business needs.