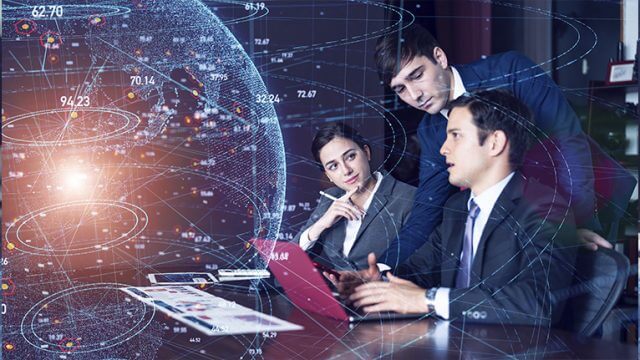
E-Invoicing and Its Geopolitical Stakes
France’s electronic invoicing reform relies on a Y-architecture, where Partner Dematerialization Providers (PDPs) play a central role in issuing and…
Generix Announces New AI-Powered Resource Management System (RMS) to Intelligently Optimize All Warehouse Resources Read the press release
In other words: Santa now runs a multichannel operation, and a highly seasonal multichannel operation at that.
To make sure that everyone keeps getting exactly what they want and that gifts are delivered on time, Santa has had to scale. We have it on good authority that, among other things, Santa has implemented Supply Chain Execution (SCE) solutions in his workshop and warehouse to better support the elves in their work and to ensure that no item or component is out-of-stock that would make it impossible to fulfill every kid’s wish list.
Of all his new SCE solutions, Santa is most thankful for his Warehouse Management System (WMS). A wise man, Santa has opted for a WMS that comes equipped with Manufacturing Execution System (MES) capabilities. The WMS/MES solution enables him to streamline activities across his workshop and warehouse. Now, he can rely on accurate visibility into his inventory in real time and benefit from efficient workflows across his entire operation.
Of course, Santa’s not the only supply chain operator out there who has to contend with the season’s logistics challenges. But, if a WMS can help Santa deliver his gifts on time, surely it should also be helpful to distribution center operators during their peak season, right?
Let’s take a closer look.
There’s a lot of magic to what Santa does. Nevertheless, his capacity to make kids happy around the world ultimately revolves around something far simpler: being prepared and anticipating demand. Turns out that the data provided by his WMS makes that possible to achieve without any Christmas magic.
Thanks to his WMS, Santa obtains a detailed and accurate picture of the toys and components that are still available on his shelves; of wish-list trends; of the items that were most in demand last year (and the years before); etc. No stranger to Pareto’s Law, Santa uses that data to identify the 20% of items that will appear on 80% of the kids’ wish-lists and prepares his inventory accordingly.
Now, it’s important to keep in mind that Santa’s ability to make accurate forecasts also comes from years and years of data, unrivaled experience, and a magical je ne sais quoi. Supply chain operators know all too well that perfect forecast accuracy is beyond the means of non-magical warehouse managers. That being said, by integrating their WMS with an AI application and relying on warehouse management best practices, companies can achieve levels of forecast accuracy that may just rival Santa’s.
The U.N. recently announced that human population has reached 8 billion. That’s a whole lot more kids than 20 years ago! To such an extent that elves in the warehouse had serious doubts that Santa’s workshop and warehouse would be large enough to meet the rising demand. Thanks to his WMS, however, Santa was able to optimize his warehouse’s capacity and now has all the space he needs to get the job done.
The inventory data provided by his WMS has helped him find the optimal locations for all the toys and components relative to their size, quantity, fragility, popularity, etc.
The data has also helped him determine the right quantity of safety stock to maintain in order to make sure that he doesn’t run out of popular items or that shelves aren’t overflowing with toys that would then crowd the aisles and make it difficult for the elves to fulfill the wish-lists.
In his efforts to keep a lean inventory, Santa has integrated his WMS with his ERP. Now, new toy parts are ordered as soon as quantities reach a specified threshold. And, of course, Santa is able to adjust these thresholds to factor in longer lead times when needed. Seasonal peaks will almost always test a warehouse’s capacity. In some cases, companies have to resort to external solutions, such as 3PLs, to augment their storage capacity for a time. But in many cases, a WMS spares companies the extra expenses that threaten their margins by helping them optimize the use of their space.
Elves are efficient and tireless workers—and cheap labor, the Grinch might add! They are not, however, perfect. Some elves are more productive than others, and newcomers always take a while to bring up to speed. In recent years, Santa’s also had to contend with fewer elves in the shop and has had troubles recruiting new ones; apparently, younger elves aren’t keen to work in his workshop anymore.
Santa has integrated his WMS with mobile handheld devices that resemble the mobile phones and platforms younger elves love so much. The WMS’s intuitive interfaces guide and support elves in their activities, making workflows far more efficient. The handheld devices and WMS also facilitate the onboarding of the new elves joining Santa’s workforce at the peak of the season.
Labor shortages have been plaguing supply chain operators for years now. A WMS reduces an operator’s reliance on a large workforce by optimizing movements in the warehouse. It also helps to train seasonal workers faster, which helps companies save on training costs and minimize operational penalties caused by an inexperienced workforce.
The elves are making and picking toys for every kid in the world. The thing is, not every country celebrates Christmas exactly in the same way—or at the same time, for that matter. Consequently, Santa’s elves have to deal with many different types of wish lists and meet a variety of wrapping requirements. They also have to get packages out of the warehouse and onto Santa’s sled at the right time to make sure that they are delivered on time, whether that’s in a store or right under the tree. That requires a very well-coordinated shipping dock!
Santa’s WMS has been configured to instruct his elves on how to fulfill the different wish lists and ensure conformity with national requirements and regulations. In order to assign more efficient picking tasks, the system also groups together wish lists that share similar properties.
Meanwhile, Santa’s WMS keeps workers and management informed in real time as items are being moved across Santa’s warehouse. This helps coordinate all the different activities on the floor to avoid bottlenecks and guarantee that every package, every pallet, makes it to the dock and onto Santa’s sled in time.
Even if they are nowhere near the size of Santa’s operation, multichannel businesses can no longer hope to remain competitive without the support of a WMS. The warehouse management strategies that lead to omnichannel efficacy require far more than spreadsheets and an ERP system. To succeed, companies need accurate real time visibility on inventory and a system that supports fulfillment strategies that are adapted to the requirements of each customer and every channel. This is especially true during peak season, as the surge in demand leads to a constant influx of orders and increased inventory velocity.
Rumor has it that Santa begins preparations for next Christmas on the 26th of December. Most companies don’t have that luxury, with business running year-long. Nevertheless, early and rigorous preparations remain the key to maximizing profits during peak season.
Thanks to the Industrial Internet of Things (IIoT), technology solutions are now far more accessible than before that help companies gather the data they need and communicate that information with their suppliers, manufacturing partners, and 3PLs. As the season ramps up and things get more hectic, the ability to communicate key information across your entire supply chain is a formidable advantage. However, breaking down communication silos won’t achieve much if you rely on faulty data.
A robust and well-adapted Warehouse Management System is the foundation on which all efficient software architectures are built. And if Santa’s story tells us anything, it’s that a WMS may just be the thing to make your next Christmas season the most profitable yet.
To learn more about how a Warehouse Management System can help your company make the best of seasonal peaks, visit the Generix Group SOLOCHAIN WMS page or download the SOLOCHAIN WMS Product Sheet.
Download our Guide to the Warehouse of the Future.
France’s electronic invoicing reform relies on a Y-architecture, where Partner Dematerialization Providers (PDPs) play a central role in issuing and…
The B2B mandate in Germany, set to take effect on January 1, 2025, marks a crucial step in the European…
Following the October 15 announcement regarding the abandonment of the PPF development, the DGFIP and its partner AIFE are ramping…
Work with our team to build your ideal supply chain software stack and tailor it to your unique business needs.