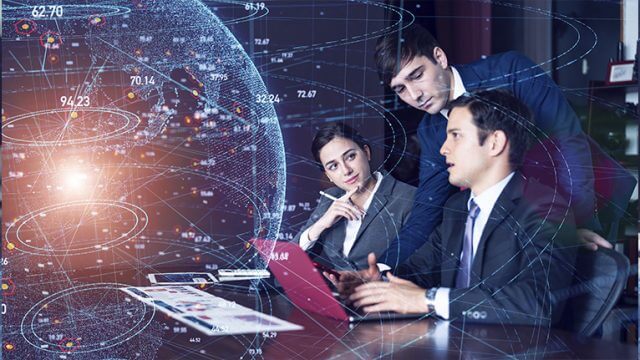
E-Invoicing and Its Geopolitical Stakes
France’s electronic invoicing reform relies on a Y-architecture, where Partner Dematerialization Providers (PDPs) play a central role in issuing and…
Generix Launches Solochain Now – Packaged Solution to Deploy a Complete SaaS WMS in as Little as 16 weeks View the press release
How holistic supply chain software platforms and digital-first approaches are helping companies manage their remote and socially-distanced workforces.
The remote work economy is booming, and the logistics, warehousing, and supply chain sector hasn’t been immune to this shift. In early-2020, about 5% of employees worked as full-time staff from home; by June, that number had jumped to about 50%. Most of the increase was due to COVID, but the trend isn’t expected to fade anytime soon. In fact, 70% of the American workforce is slated to be working remotely at least five days per month by 2025.
“The pandemic brought about the biggest work experiment in history, accelerated digital trends, and has opened up new habits, possibilities, and thinking” said Robert Garlick, Head of EMEA Equity Research at Citi, which recently published a report on the topic. “The answer is likely for employers to give their talent the choice. Let them experiment and innovate. A combination of choice and technological process means we are unlikely to go back to norms at the start of this year/decade.”
If telework is the new normal, what are the implications to sectors, corporates, and society? And, how will it ultimately affect the logistics and supply chain space, where hands-on work is the commonplace and where many operations are still running on propriety software solutions, Excel spreadsheets, and paper-based systems?
Needless to say, companies operating in the logistics sector are having some pretty deep conversations right now and figuring out new ways to take action from afar, all while preserving the health of their employees and their operations.
“The onset of the coronavirus epidemic has accelerated the supply chain digital transformation that has languished on businesses’ ‘to-do list for years,” EPS News reports, noting that COVID-19 has exposed barriers to collaboration that most companies tolerate under normal circumstances. Pre-COVID, for example, McKinsey found that 92% of companies thought their business models would need to change given digitization.
“Although management has bought in to the digital evolution,” EPS News adds, “the investment and effort necessary for the transition have been eclipsed by day-to-day business needs.”
These needs translate directly into the supply chain software space, where the physical logistics process requires, at minimum, a transportation management system (TMS), warehouse management system (WMS), and a yard management system (YMS). Those are the elements that interact with the physical movement of inbound and outbound shipments in the fulfillment center.
Now, consider how a company might orchestrate its remote workforce from a distribution and transportation perspective. Logistics workers were deemed essential from the very beginning of the outbreak because, ultimately, goods have to physically move. Fast-forward to the current landscape, and until all fulfillment and transportation activities are autonomous—a scenario that’s still off in the distant future—employees need to be onsite and engaged in the process.
This creates an interesting set of challenges for organizations, many of which have shifted to allowing as many employees as possible to work remotely. Concerned about the outbreak and social distancing rules while also getting more comfortable with the idea of allowing people to work from home, these companies are driving an entirely new workforce movement right now.
For example, Twitter’s message came through loud and clear: you can work from home forever if you want to. And with this statement, CEO Jack Dorsey basically let the company’s suddenly-remote workforce know that he was fine with it not going to a physical office every day. Google and Facebook have both told its employees to plan to work remotely until 2021, and Morgan Stanley has reportedly been considering shrinking its office footprint, according to Commercial Observer.
But where computer coders and customer service agents can fairly easily set up shop at home and be productive, the employee who makes a living picking and packing orders for an e-commerce company probably doesn’t have that luxury. Nor does the lift truck driver who moves goods around the warehouse every day, or the dock worker that loads tractor trailers for a living.
As companies shift to more remote work and come up with plans of action for their essential, onsite workers, their managers, supervisors, planners, and coordinators are tapping into technology to help them do their jobs remotely. To effectively manage these suddenly-remote workforces, more companies are turning to web-based applications versus those that involve fixed stations.
A company that relies on Tableau’s dashboards and metrics to provide actionable data, for example, can equip its mobile users with the tools they need to be able to quickly reprioritize, reshuffle demand, reallocate labor resources, or take another appropriate action. This can all be done without having to be physically out on the warehouse or DC floor, interacting with employees.
From the planning perspective, the same manager has an aggregate view of what’s going on across the entire supply chain network. This is particularly valuable in a multifacility scenario, where having that holistic view can mean the difference between making a quick decision and unknowingly allowing something to fall between the cracks.
Armed with an aggregate view, the manager or supervisor can easily see where, what, and how the demand should be distributed across the operation to ensure the maximum utilization of resources. Going a step further, he or she can see all of the inventory that’s on hand to satisfy that demand and ultimately meet the customer’s expectation.
Put simply, it’s all about creating a collaborative logistics process without necessarily having an entire workforce onsite, and standing shoulder-to-shoulder. Whether it involves a TMS, a WMS, a YMS, or a holistic supply chain platform that includes all of these applications, this tech-first approach puts the power into the hands of managers who, in turn, can transfer that power to each of their employees in a very safe and secure manner.
As logistics and transportation continue to play critical roles in getting essential and non-essential goods into customers’ hands, expect to see companies getting even more creative with their remote workforce approaches. “Having to work remotely during this crisis has moved the discussion of how to use digital tools to ensure a productive work environment forward,” Material Handling & Logistics reports.
“This is a global experiment in rapid digital transformation and a rapid conversion from on-site work to remote work,” the publication continues. “Many of the old questions about whether people could work effectively remotely and be productive is being answered. And that answer is yes.”
The coronavirus pandemic has forever changed the field of warehousing and distribution. It is threatening a logistical and transportation slowdown. It’s too early to quantify the full impact but devising backup plans is a must.
France’s electronic invoicing reform relies on a Y-architecture, where Partner Dematerialization Providers (PDPs) play a central role in issuing and…
The B2B mandate in Germany, set to take effect on January 1, 2025, marks a crucial step in the European…
Following the October 15 announcement regarding the abandonment of the PPF development, the DGFIP and its partner AIFE are ramping…
Work with our team to build your ideal supply chain software stack and tailor it to your unique business needs.