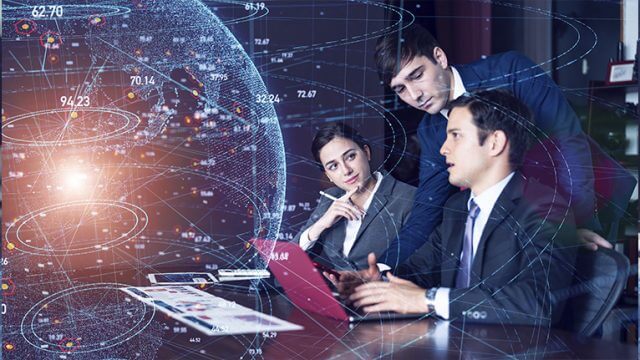
E-Invoicing and Its Geopolitical Stakes
France’s electronic invoicing reform relies on a Y-architecture, where Partner Dematerialization Providers (PDPs) play a central role in issuing and…
Generix Announces New AI-Powered Resource Management System (RMS) to Intelligently Optimize All Warehouse Resources Read the press release
EDI is a foundational element of VMI programs which allow trading partners to share inventory data and create a “push” or demand-driven supply chain with lean inventory levels. VMI programs also require careful management of the supply chain, aided by frequent deliveries and demand forecasting with some degree of accuracy.
The concept of collaborative replenishment takes VMI to the next level with advanced technologies such as cloud, mobility, big data analytics, and even AI. This means that trading partners have more flexibility and greater communication capabilities via data sharing to truly collaborate, even empowering a partner to suggest or recommend an order.
Collaborative replenishment tools allow suppliers and their sales channels to meet two critical challenges of peak season:
Stock coverage is a key KPI to monitor in any shared procurement management environment. Suppliers and their trading partners need to manage disruptions during peaks, often in real-time. Suppliers need to limit excess inventory in their channels while preparing for unexpected surges in sales or disruptions that can cause early shortages.
Features of collaborative replenishment systems may include truck building and the ability to pool resources like warehouses and trucks among suppliers to optimize inventories and reduce transport costs. Trading partners may also have access to inventory allocation and available to promise (ATP) planning features to further optimize inventory levels.
The Generix Collaborative Replenishment smart platform enables automatic calculation of PO quantities to cover the customer’s consumption (sales out from the DC to stores) until the next possible delivery date. Suppliers can easily experiment with different scenarios to optimize stock levels against demand. Logistics providers often use the solution for pooling capabilities to simulate stock-out analysis via a powerful computation engine.
Consumption forecasting, also known as demand planning, is another critical KPI in co-managed environment. Going beyond just accurately identifying inventory levels, a replenishment solution must provide reliable consumption forecasting in order to make future supply calculations.
Forecast calculations are typically based on sales history, and must take into account past shortages, while integrating any new information from trading partners as well as available external information, such as weather or consumer-related data. Advanced collaborative replenishment systems can draw from various types of demand signals with enhanced analytics tools which may even incorporate external information from third-party data sources like weather and Census-demographic information to sharpen demand planning accuracy at the regional, city, store or SKU level.
As a result, when demand changes due to marketplace events, promotions or supply chain disruptions, suppliers can build better forecasts and then proactively manage the supply chain. They can head off stock-outs and respond to disruptions (whether anticipated or unexpected), or prepare for changes in demand patterns from happenings such as trends, sporting events, cultural events and holidays.
Reduced inventory levels, optimized transportation, improved customer service and increased sales volumes are among the many benefits of using collaborative supply management. Worldwide, Generix customers using our stock replenishment-collaborative replenishment EDI-based solution have reduced shortages by 30% while lowering transportation costs by 15% on average, thereby increasing sales by more than 10% to 24% on average.
France’s electronic invoicing reform relies on a Y-architecture, where Partner Dematerialization Providers (PDPs) play a central role in issuing and…
The B2B mandate in Germany, set to take effect on January 1, 2025, marks a crucial step in the European…
Following the October 15 announcement regarding the abandonment of the PPF development, the DGFIP and its partner AIFE are ramping…
Work with our team to build your ideal supply chain software stack and tailor it to your unique business needs.