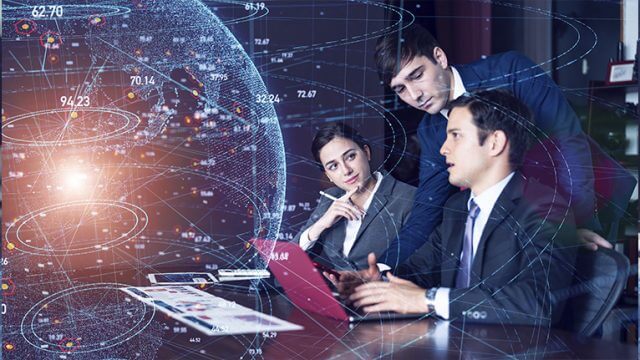
E-Invoicing and Its Geopolitical Stakes
France’s electronic invoicing reform relies on a Y-architecture, where Partner Dematerialization Providers (PDPs) play a central role in issuing and…
Generix Delivers Schematron for Electronic Invoicing to AFNOR to Ensure Interoperability Between PDPs Read the press release
Assisting the operator with a robotic arm to avoid repetitive movements in assembly tasks; improving working conditions and reducing ergonomic risks during pick and place operations (moving parts or goods); optimizing and securing palletization… these are some of the advantages of collaborative robotics in the logistics sector. However, in practice, this collaboration between a human and a robot is far from being innate. Let’s take a closer look at four good practices.
In a HPC approach, the human and the robot do not just work side by side: they work together, in the same space, with physical contact. How to define and allocate the tasks of each, in complete safety for the operator, is the first big challenge. Organizing and documenting the allocation of tasks and subtasks in human-robot collaboration is essential, but not sufficient. To ensure a sustainable and resilient collaboration, many variables and assumptions must be foreseen from the start to allow flexibility in the system and prevent risks. For example, identify potential dangerous or inefficient movements; take into account cognitive and psychological factors of the collaborators (inattention, de-motivation..), etc.
In 1996, Barbara J. Grosz, a leading Harvard computer science researcher, was already working on collaborative systems. She pointed out that collaboration between a human and a machine implies both interaction between the two parties, i.e. two-way communication, and also a sharing of intentions. In other words, the ability to understand each other in order to achieve a common goal. In the logistics sector, good collaboration is based on the one hand on the training of operators in the use of digital tools and human-machine interfaces. On the other hand, it depends on the robot’s ability to anticipate unforeseen behaviors and intentions of the human, in order to adapt accordingly. This means taking into account objective indicators, such as time or quality. Equipping operators with wireless sensors is another way to feed the robot with useful data, to avoid collusion risks, for example. Numerous experiments based on voice recognition are underway, allowing robots to understand the natural language of operators to adjust their actions.
The implementation of a human-robot collaboration system requires a complete overhaul of the warehouse organization. The risk is to impose the use of cobots without a solid strategy. The role of a CRO, for Chief Robotics Officer, is to act as a conductor at the crossroads of engineering, HR and business. It is no longer just about managing employees, but hybrid teams, composed of humans and robots. This profile is still under-represented. “Many organizations do not have the internal expertise in robotics and automation (…) to make informed and strategic decisions,” says Dwight Klappich, VP analyst at Gartner Supply Chain.
96% of logistics professionals surveyed by Gartner are using or considering cyber-physical automation in warehouses or production facilities.1
Definition of cyber-physical system: a set of IT tools that work together to control physical entities, such as cobots or exoskeletons…
In the context of logistics warehouses, effective human-robot collaboration is not based on a duo but on a trio of players, as the WMS also plays a key role. Indeed, cobots must be able to exchange in real time with the global management system. Thus, the ability of the WMS to interface quickly and easily with all the automation tools and services to which the robots are connected is crucial.
Moreover, no matter how intelligent a robot is, it is not immune to technical failure. In a HPC model, the tasks allocated to the cobots must always be physically and technically accessible to the operators, so that they can take over in case of a problem. If necessary, the WMS must also be able to switch immediately to manual mode to avoid production stoppages.
Generix’s integrated warehouse management solutions meet these key issues of interfacing and reversibility. They also facilitate the adoption (and acceptability) of robots by teams, thanks to user-friendly interfaces boosted by gamification.
1 According to Gartner Supply Chain Practice, September 2021
You may also be interested in these contents:
France’s electronic invoicing reform relies on a Y-architecture, where Partner Dematerialization Providers (PDPs) play a central role in issuing and…
The B2B mandate in Germany, set to take effect on January 1, 2025, marks a crucial step in the European…
Following the October 15 announcement regarding the abandonment of the PPF development, the DGFIP and its partner AIFE are ramping…
Work with our team to build your ideal supply chain software stack and tailor it to your unique business needs.