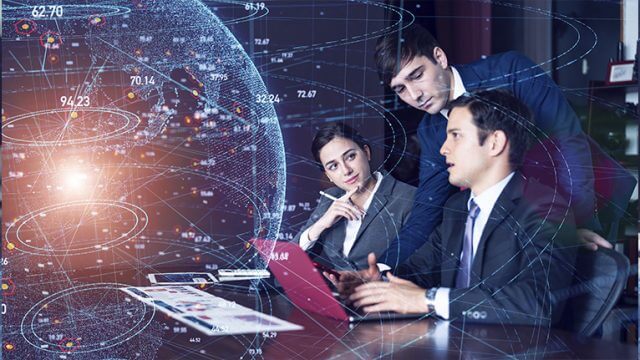
E-Invoicing and Its Geopolitical Stakes
France’s electronic invoicing reform relies on a Y-architecture, where Partner Dematerialization Providers (PDPs) play a central role in issuing and…
Generix Announces the Appointment of Olivier Vaillancourt as General Manager for North America View the press release
It is true that more than a quarter of the recruitment missions carried out by Michael Page Purchasing & Supply Chain still concern the traditional positions of operations manager and logistics site manager, which are highly penurious. However, the new challenges of the sector (digitalization, customer experience and environmental impact in particular) are leading to the appearance of functions that are rare today, but which will be democratized in the years to come.
This specialist in logistics issues explores large volumes of unexploited data and internal and external information flows in the supply chain. Thanks to his calculations, he draws conclusions, develops predictive models and formulates optimization recommendations for the company. His role consists in transforming complex statistical analyses into graphs and other data-visualization tools to make them accessible to internal teams… and thus enlighten business decision-making. For example, he can help Demand & Supply planners and sales people to refine their sales volume predictions thanks to real-time customer transaction analysis, in order to adapt inventory accordingly.
Historically, the Logistics Designer designs and models a chain according to cost, time and quality objectives. Working in a design office upstream of operational activities, they design or optimize a logistics network according to the different supply options, define flows, processes, robotization equipment, etc. The Supply Chain Architect takes on some of these traditional missions, but with a more global scope and a long-term perspective. His role: to design a network and agile platforms, taking into account :
new customer satisfaction issues (last mile delivery, return logistics);
warehouse equipment (GPS beacons, augmented reality, etc.) and information technologies (supply chain solutions) that promote real-time flows
risks of unforeseen events or incidents.
Blockchain, Internet of Things (IoT), drones, Robotic Process Automation (RPA)… all these anglicisms are at the heart of the technological revolution underway in the supply chain. The Supply chain innovation leader acts as an internal facilitator, to spread a culture of innovation, to support the adoption of new technologies and to lead the change. In addition to his or her monitoring work, he or she leads internal working groups and ideation workshops, deploys experiments and, if necessary, pilots their industrialization.
How can the supply chain be decarbonized to meet the company’s social and environmental responsibility objectives and current and future regulatory constraints? This is the question to which the Sustainable Logistics Manager must provide concrete answers. Objective: limit the environmental cost of the supply chain and implement circular economy strategies, while preserving margins and the customer experience. Energy management, waste recycling and recovery, reuse of packaging, green transport, recovery of used products: these are all areas at the heart of this emerging profession.
Blocking of the Suez Canal, the Covid-19 pandemic… these global crises have highlighted the fragility of supply chains, but also their vital/strategic importance. If this function of supply chain conductor already exists in large companies, recent events have reminded us how indispensable this role is in executive committees or management boards. Because it is the only one capable of bridging the gap between the company’s strategic vision, technological expertise and risk management. Just like the other executive functions in the famous C-suite (CFO for finance or CDO for data or digital), the CSCO is responsible for optimizing the performance of the supply chain, ensuring its transformation and above all guaranteeing its resilience.
In addition to the technical skills (finance, data, digital, risk management) that are essential for these new professions, the soft skills of employees are crucial. Among them, curiosity, the ability to self-train and to collaborate with other business expertise (marketing, R&D…) are among the key success factors for those who choose these new logistics professions.
You may also be interested in these contents:
France’s electronic invoicing reform relies on a Y-architecture, where Partner Dematerialization Providers (PDPs) play a central role in issuing and…
The B2B mandate in Germany, set to take effect on January 1, 2025, marks a crucial step in the European…
Following the October 15 announcement regarding the abandonment of the PPF development, the DGFIP and its partner AIFE are ramping…
Work with our team to build your ideal supply chain software stack and tailor it to your unique business needs.