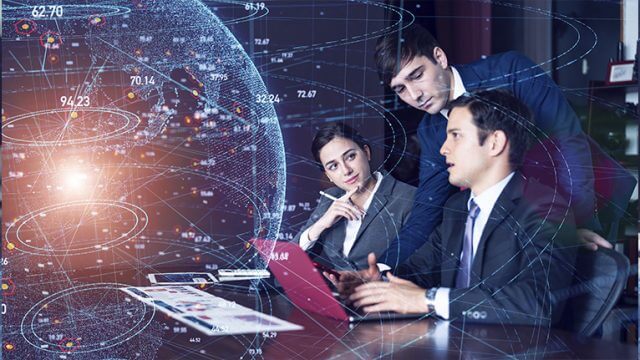
E-Invoicing and Its Geopolitical Stakes
France’s electronic invoicing reform relies on a Y-architecture, where Partner Dematerialization Providers (PDPs) play a central role in issuing and…
Medial International Chooses Generix Warehouse Management System (WMS) to Digitalize Its Logistics Operations Read the press release
The transport sector has been deeply impacted by the Covid-19 pandemic. In 2020, we had to deal with border closures and the various restrictions imposed by each country, which caused an increase in the overall lead time of all goods. Many production sites, factories, warehouses and stores were forced to close, which automatically dealt a heavy blow to carriers, whose own operations are so closely aligned with these companies’ activities. In addition, as a consequence of the health situation, the supply of products and the means of transport became scarce – with a particular shortage of maritime containers – while demand remained high. At the same time, the massive growth of e-commerce and omnichannel distribution changed the expectations of B2B customers, who are now looking for a quality of service identical to that of B2C. The Covid-19 crisis therefore shook the very foundations of logistics organizations and imposed major transformations. In such a context, thinking about how to optimize transport costs is clearly essential. But we can wonder, where to start ?
Walter Vittori: The first cause of unnecessary expenses is the use of a service or a carrier unsuitable for customer needs. It is on this disparity between the real need and the purchased service that we must focus as a priority. Arnaud Pausé: We must also take into account the organizational dimension. The way in which stocks and orders are processed will be decisive in optimizing the handling and distribution of goods, and therefore in reducing the associated costs.
Isabelle Badoc: At the present time it is generally considered in Europe that we are still transporting at only 50% of capacity. It is therefore essential to work on the one hand to densify containers, which a WMS1 (Warehouse Management System) can help to achieve, and on the other hand to optimize loading plans so as to transport the maximum of goods in a minimum of vehicles. This is exactly the role of a TMS (Transport Management System), which receives a portfolio of orders and calculates the best possible combinations of these orders in the most suitable means of transport, according to the characteristics of the products to be delivered, the commitment made to the recipient (time and place of delivery). The TMS will dig into its database of referenced carriers to choose, for each journey, which carrier to request in priority. Replacing an Excel-based system with a well-configured TMS represents potential savings of over 30% on transport bills.
Walter Vittori: The crisis has shown the limit of in-house management tools that relied on Excel tables, emails and phone calls to rearrange things as needed. However, it is difficult to make these adjustments when you can no longer access your workplace, without visibility of the reality on the ground. The lack of shared tools and connectivity between the different actors in the logistics chain, whether shippers, carriers or customers, was therefore exacerbated by the pandemic. Without exploitable data, without serious management tools and/or automated processes, it is very difficult to have the global vision necessary to make the right decision when a problem arises. This is undoubtedly why digitization projects have increased sharply in 2020. Be careful, however: digitization should not be seen as an end in itself, but as a way of deploying a given strategy effectively. Arnaud Pausé: Digitization makes it possible to go faster, further, to optimize not only data management but also the management of the flow of goods and information between the different actors of the ecosystem. A well-configured and well-managed system will enable customers to save time in the implementation of their strategic vision and in the achievement of their objectives.
Isabelle Badoc: In addition to optimizing routes and loads, AI can be very useful in two key areas: hazard analysis and invoice matching. AI is indeed able to identify what is outside “normalcy”, such as, for example, the sudden increase in the cost of transporting a category of products, and the need to issue an alert so that we can take action as soon as possible. With regard to invoice matching (i.e., the line-to-line verification that what has been invoiced is faithful to the initial order), this is an extremely time-consuming activity because there is no standard model: each carrier has its own method of setting prices. Currently still mainly carried out manually, this operation will become more and more automatable thanks to AI.
Isabelle Badoc: Document management in transport can be an ordeal if you have to do everything by hand. Fortunately, it can be automated by digital tools. It is also true for communications with carriers, who can manage their reservations online. This represents a huge time saving for both the loader and the transporter. As for invoicing, the TMS can contribute both to the cost breakdown (i.e., the distribution of the costs of a single transport invoice between the entities of the relevant company) and to the monitoring of carriers’ invoices.
Arnaud Pausé: Understanding the details of transport costs and the way in which we are invoiced by carriers, is a clear lever for optimization. In transport, there are various taxes, miscellaneous costs, additional charges or penalties related to contingencies. Monitoring this analytical dimension makes it possible to match the final carrier invoices with the price initially announced.
Walter Vittori: The customer has everything to win by doing so, since our fees are entirely calculated on any savings made. I am also convinced that our activities, which are highly operational in nature, are complementary to those linked to information systems. I believe in the effectiveness of combining the capacities of business solutions with our own discerning expert vision.
Isabelle Badoc: There is indeed a real complementarity between us. Our job is to offer supply chain execution, to implement our customers’ strategic and operational decisions. For this, it is necessary to define upstream the levers of potential savings, the strategy and the organization required to maximize the efficiency of the transport service and the desired nature of the target information system. These are precisely the prerequisites for which the consulting firms can provide our customers with the support and assistance they require.
1 Warehouse Management System : Système de gestion d’entrepôt
France’s electronic invoicing reform relies on a Y-architecture, where Partner Dematerialization Providers (PDPs) play a central role in issuing and…
The B2B mandate in Germany, set to take effect on January 1, 2025, marks a crucial step in the European…
Following the October 15 announcement regarding the abandonment of the PPF development, the DGFIP and its partner AIFE are ramping…
Work with our team to build your ideal supply chain software stack and tailor it to your unique business needs.