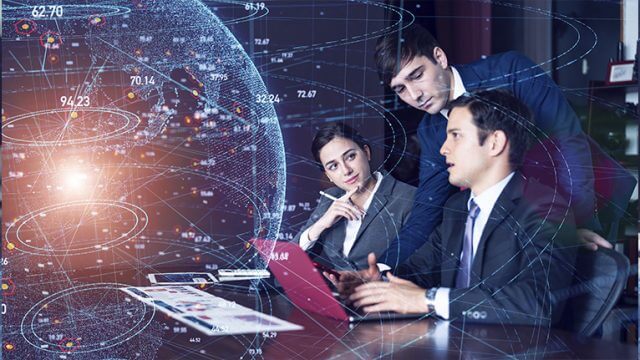
E-Invoicing and Its Geopolitical Stakes
France’s electronic invoicing reform relies on a Y-architecture, where Partner Dematerialization Providers (PDPs) play a central role in issuing and…
Generix Announces the Appointment of Olivier Vaillancourt as General Manager for North America View the press release
Battlefield commanders in the Second World War knew that a lengthy supply chain was a risky supply chain; in peacetime, some 80 years later, the world’s economies know it, too. However, while supply chains have struggled back to their feet, the enormous economic damage to the demand side of the supply/demand equation remains.
An economic recession comes on gradually and its signs and symptoms can be seen months before in declining consumer spending, reduced hiring, increased layoff notices, rising unemployment, shrinking output and so on. On the other hand, the pandemic blew in like a sudden, violent summer storm, wreaking havoc overnight.
To their credit, CSCOs (Chief Supply Chain Officers) responded as agilely as they could; they saw how the plunge in demand ran neck and neck with the plunge in supply and tried their best to adapt their organizations to seize on new demands being created for products like masks, sanitizers, ventilators and so on. Boston Consulting Group (BCG) refers to these as “rapid response” efforts. In the early days and weeks of the global health crisis, those in the supply chains worked tirelessly to pivot and perhaps even profit from these overnight demands.
Companies were taking other critical steps at the same time, part of their rapid responses; they tried to create as much transparency within supply chains as they could. They assembled lists of the vital components they needed while determining the reliability of supply and, if necessary, finding alternative suppliers in order to keep production running and customer deliveries fulfilled. McKinsey stated in a March 2020 report that several industries (automotive, consumer and mass retail) had two to three months of inventory, at best, unless steps were taken to minimize that risk.
Fortunately, six months along, many governments, corporations, public health officials and the general population know a great deal more about the virus today than in the first few weeks and have implemented coping strategies to mitigate the ongoing crisis. CSCOs are now beginning to think about what the future of their businesses will look like in a post-pandemic world and are facing many questions – some that may remain unanswered for some time. When will an effective vaccine arrive? When will the current high levels of unemployment in the U.S. and other countries come down?
A recent poll shows that nearly half of American households where a job was lost, believe the loss is permanent, meaning some 14 million jobs could be gone for good. Boston Consulting Group has laid out five areas in which efficiencies can be realized within a supply chain:
Wide open visibility means the CSCO can see cost controls, inventory, quality, lead-time, and service, all in real-time. Such a transparent supply chain can only be achieved through implementing technology solutions designed for supply chain use but Boston Consulting maintains that the value impact is considerable:
Taking this step, says BCG, means implementing new, flexible processes that would be essential to managing highly changeable demand and supply. Key to these processes would be refined Sales and Operations planning and “demand sensing”, essentially a way of spotting the first shifts in demand patterns through the use of data analysis and artificial intelligence. Boston Consulting claims companies could see at least a 10% increase in their sales forecast accuracy, something that has desirable ripple effects throughout a supply chain. Closely Integrate with Suppliers, Vendors and Customers
It makes sense in a supply chain to have as much integration as possible because that ensures that every vendor and supplier can see in real-time whether customer demand is set to tick higher or lower. This type of integration involves sales teams in the front office and S&OP teams in the back office, all with access to analyzed data from an ERP.
BCG has suggestions for the warehousing component in a supply chain: reduce low-volume SKUs and create dedicated lines for specific products while reducing the number of locations where a SKU is placed in order to simplify planning and limit inventory build-up. The payoff? A 10% to 30% savings in manufacturing-conversion cost, 5% to 10% reduction in inventory levels and increased supply chain efficiency.
There are four elements to this component:
The fastest way – indeed, the only way – to reach the cost savings outlined by Boston Control Group is through implementation of the right technology solutions. These solutions exist today and are designed specifically to meet supply chain challenges. Generix Group North America has a suite of such technologies within their Supply Chain Hub offering which can achieve these goals.
Contact us today and find out how we can boost the value within your supply chain operations.
France’s electronic invoicing reform relies on a Y-architecture, where Partner Dematerialization Providers (PDPs) play a central role in issuing and…
The B2B mandate in Germany, set to take effect on January 1, 2025, marks a crucial step in the European…
Following the October 15 announcement regarding the abandonment of the PPF development, the DGFIP and its partner AIFE are ramping…
Work with our team to build your ideal supply chain software stack and tailor it to your unique business needs.