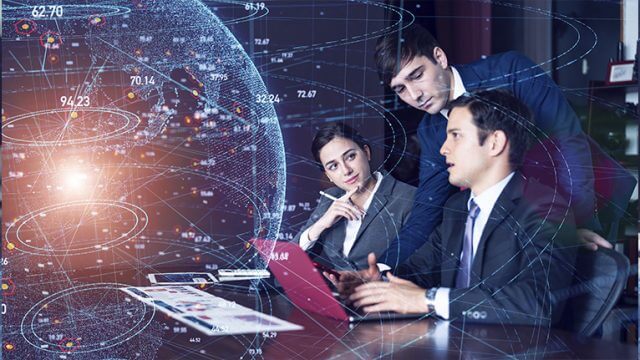
E-Invoicing and Its Geopolitical Stakes
France’s electronic invoicing reform relies on a Y-architecture, where Partner Dematerialization Providers (PDPs) play a central role in issuing and…
Generix Delivers Schematron for Electronic Invoicing to AFNOR to Ensure Interoperability Between PDPs Read the press release
Volkswagen Group Spain Distribution hit the ground running when it launched its PRO Service platform on the spare part distribution market, soaring past direct sale competitors that provide parts to professionals in the automobile repair sector.
The company considers service deployment to be a growth driver and a way to stand out from competition, with the main goal of ensuring the traceability of parts distributed on the automobile market. A tight grasp on spare part destination is essential in the event of product recall, and helps strengthen a brand’s professional image among clients, not to mention increasing perceived quality of service.
Volkswagen Group Spain Distribution had no logistics department when the PRO Service project was launched in 2016, and the German manufacturer called on Generix Group to assist it in coming up with a new distribution strategy. Generix Group worked with Volkswagen Group Spain Distribution teams to custom tailor its warehouse management system (WMS), working with teams to redesign logistics flows and optimize them. This work included receiving and storing merchandise according to size and product turnover, preparing orders according to urgency and cross-docking, among other exchanges.
According to the PRO Service distribution model, it must be possible to ship every part in the catalogue—which includes 845,000 references—to repair shops within two hours, with a target of four daily deliveries. This sales strategy also includes a “zero error” objective likely to offer clients full satisfaction.
The optimization of logistics flows done by Generix Group and project teams according to Agile methods proved crucial when responding to this ambitious logistics promise. In order to reach its PRO Service deployment objectives, Volkswagen Group Spain Distribution plans to hire 400 professionals, including about 15 engineers who will act as repairmen.
PRO Service was launched in 2017 in four distribution centers located in Zaragoza, Lleida, Gerona and Tarragona. Today, it is operational in Barcelona, Madrid, and the north and east of Spain. All in all, 41 interconnected warehouses handle spare part orders for the brand, which are shipped out all over Spain. Today, Generix Group is working on continually improving project processes.
The logistics chain deployed for the PRO Service Project is actually quite similar to an e-commerce model. In this case, it’s all about meeting very quick preparation deadlines, contrary to the more common B2B orders, which require a longer preparation time and include several palettes to send to the same client.
Similar to an e-commerce, PRO Service handles retail sale operations, prepared on one or two lines, in order to multiply the number of orders. When it enters into the operational circuit, a single preparer handles several lines at a time and uses picking to accelerate preparation flows. Distribution greatly resembles the provisioning methods used with last-mile delivery.
The logistics system developed using Generix Group’s WMS offers teams a plethora of features that are useful for the service and optimization of warehouse flows. These include:
The ERP-based WMS used by Volkswagen Group Spain Distribution lets teams handle all kinds of PRO Service orders quickly and effectively. Its connectivity also enables real-time sales order confirmation and helps directly adjust stocks shop-side.
A WMS system offers many benefits for automobile manufacturers. These include:
France’s electronic invoicing reform relies on a Y-architecture, where Partner Dematerialization Providers (PDPs) play a central role in issuing and…
The B2B mandate in Germany, set to take effect on January 1, 2025, marks a crucial step in the European…
Following the October 15 announcement regarding the abandonment of the PPF development, the DGFIP and its partner AIFE are ramping…
Work with our team to build your ideal supply chain software stack and tailor it to your unique business needs.