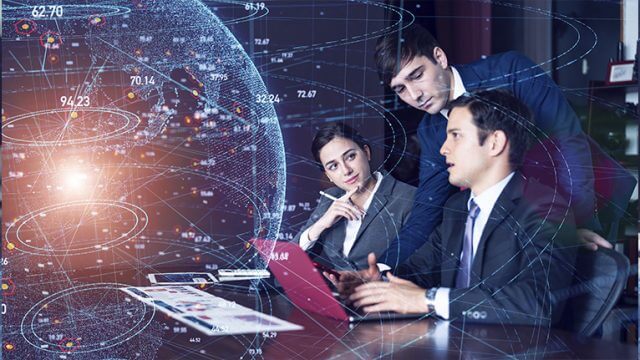
E-Invoicing and Its Geopolitical Stakes
France’s electronic invoicing reform relies on a Y-architecture, where Partner Dematerialization Providers (PDPs) play a central role in issuing and…
Generix Delivers Schematron for Electronic Invoicing to AFNOR to Ensure Interoperability Between PDPs Read the press release
Generix Group’s Langlois opened the session with an overview of the factors influencing the push for greater flexibility and use of technology in warehouses and distribution centers (DCs) today, including ongoing labor shortages, greater demand for regional distribution and hyper-local fulfillment, and continued supply chain disruptions. Langlois cited research by Gartner that found that through the next few years, WMS solutions will continue to incorporate more capabilities and technologies, bringing more advances in a period of several years than in the last 25 years. “Through 2025, technical architecture will equal functionality in importance for new WMS buyers seeking flexibility, adaptability, composability, usability and affordability,” Langlois said.
As warehouse operations become more fluid, this means that systems will need to be more modular (composable) and adaptable, allowing for continuous changes within the WMS solution. Functionality of systems are expanding to incorporate a constellation of activities under the broad warehouse operations management (WOM) umbrella, such as labor management, execution, planning and analytics as well as warehouse control and execution systems.
Next, a compelling case study followed from TLS, Inc., a Canadian buy-sell distributor in the CPG and food industry, with operations in the U.S. and Canada, and its subsidiary Emblem Logistics Inc. a third-party logistics company serving a variety of retailers, manufacturers and distributors from its DC in Brampton, Ontario. Both companies went from mostly manual processes—relying on inefficient transfer of data from the companies’ ERP systems and paper-based methods to run their warehousing and distribution operations—to a successful implementation of Generix Solochain WMS.
From the warehouse management perspective, the companies’ operations are highly complex in the regulated food industry requiring elements such as detailed batch management and code dating, with different shelf life periods by retailer, for example. TLS’ Leblanc said the onset of the pandemic in 2020 delayed its long-planned go-live implementation of Generix solution. “In January 2021, we went live with our new WMS from pen and paper to a fully functional RF all-directed system. At the time, we didn’t know what was going to happen (with the remote implementation).” With Generix representatives unable to work on site during the go-live event due to the pandemic, Leblanc said the TLS and Emblem Logistics set up a war room with its own staff and had greater reliance on its own technical specialists who had familiarity with the solution (dubbed “super-duper users”). Combined with close communication with the Generix help desk, the TLS advanced users could begin the work of the live testing, trial and error, and the training that would be required as the companies got up to speed with Generix Solochain WMS. “We powered through it. We knew what we were ready to do and the Generix team was there to help us do it on a 24/7, on-call remote basis,” Leblanc said. One example of the functionality of the Generix Solochain WMS in action was during the inventory conversion process. Under the new system, workers printed 50,000 LPN (license plate labels) using scannable barcode sequences that ultimately allow the tracking of product through every stage of the supply chain. The labels were printed and applied over the go-live weekend event.
Finally, Emblem Logistics’ Kumar outlined the many challenges of the process in the early weeks of the implementation which he described as dramatic in going from manual processes to automated. “Even though we have done the training, we knew at the start we couldn’t handle a lot of volumes (with the new system), so we reduced our inbound volumes and talked to our customers to understand what the rush and priorities shipments were. We reduced our inbound receiving (volumes) but we knew we couldn’t control our outbound as orders are needed in stores,” Kumar said.
Managing all the changes presented many challenges. The supply chain imbalances created by COVID-19 restrictions added more complexity as Emblem strove to manage its slowed operations during the early period of the implementation, while many stores were sold out of inventory as a result of the stay-at-home orders of the pandemic. Absences due to COVID added more wrinkles as back-up users needed to be added quickly.
Emblem’s advanced users of the Generix WMS solution became trainers of other DC staff. Kumar described the varying comfort levels with such systems, and sometimes trainers bypassed official procedures, improvising as they familiarized workers in the DC with how to use the system.
Kumar also noted ongoing communication with company departments and its customers were critical elements of the successful implementation. “We learned that change management is really hard, no matter what system you use, no matter how much you convey to people, whether internal or external customers. We also learned not to micromanage people,” Kumar said.
TLS and Emblem Logistics take a continuous improvement approach to how it uses and further adapts the Generix WMS solution to its operations. For example, it was able to further customize reporting parameters by client. Other benefits include the scheduling and management of its inbound transportation carriers on the Generix Solochain WMS for easier operations and performance management. One dramatic example is prior to implementing Generix Solochain WMS, Emblem Logistics was producing 350,000 to 370,000 volume case picks per week, but within about six months after the go-live start, the company had greatly increased its volumes to 550,000 to 575,000 case picks per week.
Emblem’s Kumar also cited labor savings as employees were taken off manual and paper-based methods to work more efficiently. Generix Group North America provides a series of solutions within our Supply Chain Hub product suite to create efficiencies across an entire supply chain. Our solutions are in use around the world and our experience is second-to-none. We invite you to contact us to learn more.
France’s electronic invoicing reform relies on a Y-architecture, where Partner Dematerialization Providers (PDPs) play a central role in issuing and…
The B2B mandate in Germany, set to take effect on January 1, 2025, marks a crucial step in the European…
Following the October 15 announcement regarding the abandonment of the PPF development, the DGFIP and its partner AIFE are ramping…
Work with our team to build your ideal supply chain software stack and tailor it to your unique business needs.