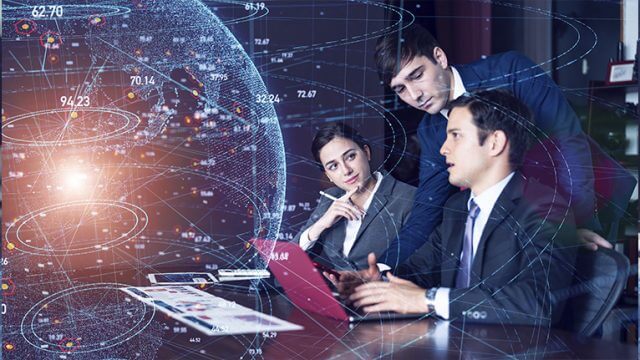
E-Invoicing and Its Geopolitical Stakes
France’s electronic invoicing reform relies on a Y-architecture, where Partner Dematerialization Providers (PDPs) play a central role in issuing and…
Generix Announces New AI-Powered Resource Management System (RMS) to Intelligently Optimize All Warehouse Resources Read the press release
The global pandemic and its subsequent impacts on the world’s supply chains have naturally brought up new conversations about reshoring and near-shoring manufacturing operations. And while offshoring still makes economic sense in many situations, companies are increasingly asking themselves whether the approach makes good long-term business sense.
Companies that relied heavily on China-based manufacturing operations to produce their goods were blindsided when the pandemic emerged in early-2020. The same thing happened once COVID made its way into the U.S., where essentials like toilet paper and disinfectant wipes quickly became scarce commodities (with some products still difficult to find on store shelves).
Right now, Thomas Insights says two in three (69%) manufacturers are looking into bringing production to North America (compared to 54% in February 2020). With the growing appetite of reshoring and onshoring, companies said that the top products they are looking to source domestically include: metals (15%), machining tools and parts (13%), fabricated materials (13%), and personal protective equipment (12%).
As they closely consider these shifts, manufacturers have a few different options at their avail. Here are some basic definitions for each from The Reshoring Institute:
Determined to create more resilient supply chains for the present and future, manufacturers are reassessing their shoring strategies and deciding on the best path forward. “Beyond multi-sourcing, some companies want to reduce geographic dependence in their global networks and shorten cycle times for finished products,” Gartner states. “Regional or local supply chains can be more expensive, because they add more players and complexity to the ecosystem, but they allow for more control over inventory and move the product closer to the end consumer.”
In the short-term, we’re seeing changes in consumer demand that are driving the need for adjustments in supply chains, warehouse operations, and inventory practices. In the medium and long-term (where the latter may be defined as little as two to three years out), reshoring and near-shoring of manufacturing could become key trends in the marketplace. The same disruptions that have impacted supply chains are also fundamentally changing the way manufacturers can find the most success in their sales and marketing efforts, Gartner reports. For example, face-to-face meetings, trade shows, and factory tours have all experienced major slowdowns or stops due to the COVID-19 pandemic.
“With the incoming growth opportunities from companies bringing their operations and supply chains back to North America, marketing and sales leaders in this space need to embrace digital transformation,” the research firm adds. “This includes taking a bottom-up approach to digital marketing that creates a strong footprint, drives qualified traffic, converts anonymous visitors to leads, and can be easily adjusted or optimized as needed.”
For example, some manufacturers are eliminating their dependency on third-party distributors and taking distribution in-house. “More businesses will see the need to start servicing customers directly, without intermediaries,” Route4Me’s Dan Khasis points out. “This leads to direct fulfillment, in effect direct drop-shipping from the manufacturer, similar to what D2C operators have achieved in recent years.” Another alternative being explored is to have suppliers deliver directly to the store. Efforts are also afoot to stage products at strategic hub stores to feed smaller stores. Finally, a variation on this is to use retail stores as “mini distribution centers” that are 1) becoming increasingly available, and 2) located in close proximity to end consumers.
A surge in reshoring could also create new opportunities for North American manufacturers. “With the ongoing COVID-19 pandemic and heightened global trade tensions, companies in North America are working to reshore and find more localized supplier partners to create resilient supply chains. “For manufacturers, service companies, and distributors in the U.S. and Canada,” Thomas Insights notes, “this means there will be an increase in the number of opportunities that become available in the form of supplier evaluations from new buyers.”
Trends that are primarily being driven by disruption, reshoring and near-shoring have come up on the radar screens of supply chain and procurement managers who are seeking out more localized supplier partners.
“These disruptions can occur in the form of an overseas factory closure due to the COVID-19 pandemic or the inability to source raw materials from nations in a cost-effective manner due to challenges from tariffs or trade restrictions,” Thomas Insights adds. “Challenges like these are creating a sense of urgency for supply chain and procurement professionals who need to ‘future proof’ their operations and create resilient supply chains.”
France’s electronic invoicing reform relies on a Y-architecture, where Partner Dematerialization Providers (PDPs) play a central role in issuing and…
The B2B mandate in Germany, set to take effect on January 1, 2025, marks a crucial step in the European…
Following the October 15 announcement regarding the abandonment of the PPF development, the DGFIP and its partner AIFE are ramping…
Work with our team to build your ideal supply chain software stack and tailor it to your unique business needs.