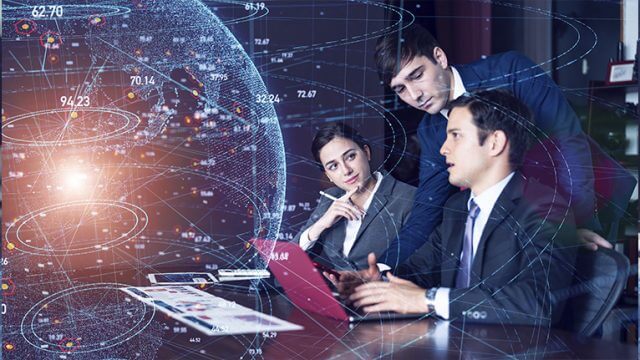
E-Invoicing and Its Geopolitical Stakes
France’s electronic invoicing reform relies on a Y-architecture, where Partner Dematerialization Providers (PDPs) play a central role in issuing and…
Medial International Chooses Generix Warehouse Management System (WMS) to Digitalize Its Logistics Operations Read the press release
4PL Category Management Collaborative Planning Forecasting and Replenishment (CPFR) Consolidation and Collaboration Center Consigned Stock Cross-docking Deported Stock Multidrop Multipick Pooling Retailer Managed Inventory (RMI) Shared Supply Management (SSM) Vendor Managed Inventory (VMI) Working Capital Requirement (WCR)
Managing all the players involved throughout the Supply Chain represents a real challenge for some companies. Therefore, they prefer to entrust this coordination mission to a 4PL (or “fourth-party logistics”) provider. In addition to the storage, order preparation and transport operations usually carried out by a 3PL, the 4PL also assumes the responsibility of independently managing supplies for its customer.
Another component of an ECR approach, Category Management is a distribution strategy consisting of optimizing sales by categories, rather than by product families, from a customer satisfaction perspective. Thanks to SSM, Category Management can improve efficiency: product organizations work together more closely, customer knowledge is refined, and dashboards are more easily shared. In fact, market placement and product assortments can be executed more precisely. Since the manufacturer has an in-depth knowledge of its products and their potential, it decides which quantities to put on the market. The distributor therefore benefits from better management of its product assortment, and the manufacturer can direct its production lines accordingly.
Based on SSM, this collaborative practice pushes cooperation further upstream by integrating planning and forecasting. The aim is to improve the Supply Chain through increased collaboration between manufacturers, distributors and logistics providers. Under this approach, sales and production forecasts are developed jointly, promotions are managed in a more participative manner, and there is a greater dialogue surrounding new products’ marketing.
On a principle similar to that of deported stocks, this time the consigned stock is stored by the logistics provider. These stocks remain the property of the supplier for as long as they remain at the provider’s location. Once the goods leave the warehouses, they become the responsibility of the distributor, who must then pay for them. Very often adopted by small manufacturers with low storage capacity, this solution also allows distributors to reduce the immobilization of their capital.
Often initiated by distributors, this solution allows small and medium-sized enterprises (SMEs) without large logistical means to meet the challenging demands of their customers by organizing fast and frequent deliveries, shipment of packages and not whole pallets, and optimizing the filling of trucks without increasing logistical costs. Therefore, 3Cs are generally aimed at suppliers who cannot access pooling, multidrop or cross-docking.
In this tight-flow supply management process, goods are delivered to a grouping/unbundling warehouse and shipped directly to the final point of sale, without intermediate storage. The aim is to allow the distributor to reduce its inventory by increasing the frequency of delivery to points of sale, but also to improve the filling rate of trucks by shipping potentially heterogeneous products.
Deported stocks are stocks established at the customer’s site, but that remain the property of the supplier. Through this consignment technique, the distributor can increase its inventory levels and improve its working capital requirements (WCR). The supplier gains visibility through the dispersal of its products and can adjust its production accordingly. For the manufacturer, it also assures better in-store availability of its products, and indirectly, a guarantee of satisfaction for the final customer. The practice of deported stock is similar to that of 3C (Center for Consolidation and Collaboration).
In this supply management model, resources are pooled between several manufacturers with customers in common. Like cross-docking, multidrop aims to optimize truck filling and increase delivery frequencies. However, to be beneficial, this mode of operation requires a geographical approximation of the delivery points, whether they belong to the same brand or not.
In this variant of pooling, goods addressed to the same delivery point are collected in different industrial warehouses. To be effective, warehouses must be located within 30 minutes of one another. Multipick, however, remains a complex process to coordinate without a mediator. It requires a good understanding of the different players in order to organize the loads in a coordinated and functional way.
Complementary to the SSM, pooling is another model of collaboration, this time established between several manufacturers. Also known as Mutual Supply Management, this way of organizing allows manufacturers to pool their resources. The goals are to reduce logistics costs, increase delivery frequencies and make supply flows more reliable, all to ensure better availability of products in stores while maintaining a lower carbon footprint.
In this organizational model, supplies are managed directly by the distributor in the form of firm orders to the supplier. By transmitting information about its inventory movements, the distributor allows the manufacturer to anticipate its production needs and optimize its inventory management.
Considered a tool of the Efficient Consumer Response (ECR), SSM is a method of supply management whose responsibility is shared between the manufacturer and the distributor. In this collaborative organization model, the supplier is tasked by the distributor to supply the products as closely as possible to the needs. The inventory and/or sales data provided by the distributor allow it to adapt its production and logistics resources, and to calculate the quantities of products to be supplied according to those needs.
Derived from the SSM, VMI relies on the provider supplying the optimal inventory to the distributor, without prior approval. Since the order has to be accepted and shipped by the distributor, VMI requires a great deal of trust in the customer/supplier relationship. Primarily practiced in the United States, this method is becoming more widespread in France via the impetus of a few distributors.
A key indicator of business performance, the working capital requirement is directly impacted by inventory levels that generate delays in cash flow. But with SSM and pooling, it is possible to have a better overall view of supplies, and thus to better control this cash flow. The level of WCR then becomes an indicator allowing the company to know if it deviates from its objectives, but also to measure the logistical and financial consequences of doing so. With projections of 3 months or 6 months, it becomes possible to anticipate the costs associated with the intervention of a logistics provider in case of shortages and seek to reduce these penalties.
France’s electronic invoicing reform relies on a Y-architecture, where Partner Dematerialization Providers (PDPs) play a central role in issuing and…
The B2B mandate in Germany, set to take effect on January 1, 2025, marks a crucial step in the European…
Following the October 15 announcement regarding the abandonment of the PPF development, the DGFIP and its partner AIFE are ramping…
Work with our team to build your ideal supply chain software stack and tailor it to your unique business needs.