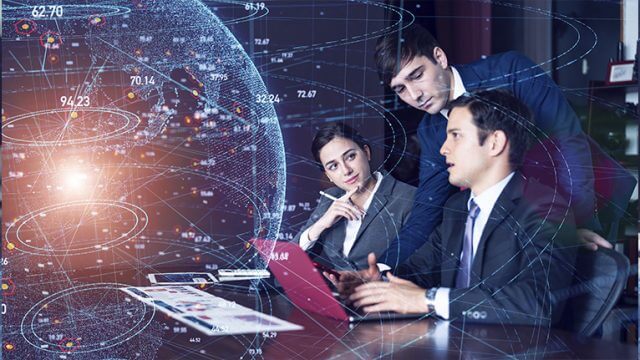
E-Invoicing and Its Geopolitical Stakes
France’s electronic invoicing reform relies on a Y-architecture, where Partner Dematerialization Providers (PDPs) play a central role in issuing and…
Generix Launches Solochain Now – Packaged Solution to Deploy a Complete SaaS WMS in as Little as 16 weeks View the press release
To assess whether or not your warehouse or DC is meeting your storage capacity requirements, you need to define what those requirements are and determine your operating storage capacity.
Any supply chain operator knows that the answer to that question will vary from week to week, season to season. So, what you need is to establish a representative baseline that notably includes a description of your active SKU base (dimensions, crushability, storage medium, etc.), quantities shipped, and average inventory levels.
To calculate your baseline, take an average week during a peak period of activity. This will ensure that your calculations are valid for most of the year without falling into the trap of undersizing or oversizing your operation.
As much as possible, try to include considerations for projected growth: estimate as best you can what your baseline might look like 5 to 7 years down the road. If you have to invest in infrastructure or technology solutions to address your capacity problems, you’ll want to maximize your ROI and avoid further investments in the near future as much as possible.
We’re not talking about your facility’s sheer volume. What’s at stake, here, is your storage space and, more specifically, your operating storage capacity (OSC). To define your OSC, you first need to figure out your gross storage capacity, that is, the total capacity of all storage locations if they were full to the brim.
If your SKU locations were completely full, it would prove nearly impossible for employees to move goods around. Similarly, if you store items in every location, you lose the operational flexibility you need to adapt to unforeseen circumstances, seasonal peaks, and sudden surges in demand. For that reason, you should aim to keep a percentage of your reserve slots (±15%) and pick slots (up to 50%) open. That explains why your OSC is more or less 85% of your gross storage capacity.
Once you’ve figured out your operating baseline and your OSC, you’re in a position to determine if you’ve indeed run out of space. If you have, it’s important that you figure out the cause(s) to ensure you implement the right solution(s). Here are some of the usual suspects:
So, you’re operating beyond what your OSC allows. Now, you need solutions. Moving your operation to a bigger facility is a possibility, but an expensive and disruptive one. Depending on the cause of your capacity problems, you may be able to avoid it. Let’s look at some of your options.
Before you consider moving to another location, make sure you’ve made the best of what the current one has to offer. Evaluate your current racking system to see if it’s adapted to your requirements. As your business grows and your SKU base evolves, it’s not uncommon to find that current location dimensions do not fit your needs.
Should you invest in a new racking system, take the opportunity to increase your storage capacity by extending it vertically or horizontally (single or double deep). Keep in mind, however, that you will then need to invest in adapted MHE to reach the new locations. Consider implementing new storage methods, such as flow racks or dynamic storage systems.
To maximize your OSC, you can also look into reducing aisle width to make room for more racks. Be careful, however, not to make them so narrow as to hinder the movement of MHE: anything less than 10 feet wide risks creating new bottlenecks, regardless of what your MHE vendor might have to say about it.
Your racking system may be adequate, but it may not be optimally laid out. Analyze your layout and available space to see if you can reorganize your racks to better fit your operation and maximize your use of available space.
Take this opportunity to assess whether your slotting strategy could be optimized. Are SKUs assigned to locations adapted to their dimensions? Are fast-movers and slow-movers well located? Is your pick-line adapted to your order profiles? Etc.
Most supply chain operators are well aware of the advantages a WMS provides when it comes to automating and streamlining warehouse operations. But did you know that it can also help improve your storage capacity?
A best-of-breed WMS, like the SOLOCHAIN WMS/MES by Generix Group North America, delivers a wealth of data that enables you to better manage your inventory. A well configured WMS can assist you in your efforts to optimize storage allocation. If integrated with your ERP system, a WMS can help you maintain a leaner inventory by automating replenishment processes, which then reduces the amount of space you need to operate.
There’s a lot a WMS can do to help you maximize your OSC and meet your KPIs with the space you have. For example, the next two solutions to maximize your OSC are somewhat dependent on having a WMS implemented in your DC.
Obsolete and slow-moving inventory that crowd your shelves are eating away at the storage space you have. Uncontrolled SKU proliferation is often to blame for that.
Identify and remove as many of your slow-movers, obsolete inventory, and redundancies as possible to make more room for your big sellers. Keep in mind that, on average, 80% of your business comes from 20% of your SKUs. With a WMS in your tech stack, you will have the necessary data to identify those fast-movers, rationalize your SKU base, and make the changes you need to maximize your OSC.
Inventory that never makes it to your shelves doesn’t take up any space! Whenever possible, implement cross-docking processes to reduce the number of items that require long-term storage and optimize space utilization in your warehouse.
Cross-docking does add a level of complexity to receiving and shipping processes. To ensure that your operation keeps running smoothly, you’ll want cross-docking processes to be streamlined and avoid crowding the docks with stock in transit. With a WMS to automate these processes and support employees in their tasks, you unlock the ability to achieve efficient cross-docking operations.
If you’ve already explored all options but remain short of sufficient storage space, it may be worthwhile to look into expanding your facility. Although adding space to your facility can make for a significant investment, it won’t be as expensive and disruptive as moving into a new facility.
The attentive reader will have noticed a trend in this paper: whether it’s a matter of calculating your baseline, determining your operating storage capacity, or maximizing your storage space, it all comes down to being able to rely on a comprehensive set of accurate inventory data.
The more data, the better!
A Warehouse Management System is a precious, if not necessary tool when it comes to addressing your storage capacity problems. The information it provides on inventory and the movement of goods across your supply chain is essential to identifying and implementing the solutions that will help you maximize storage capacity in your warehouse or DC. Take a look at Gartner’s 2022 Magic Quadrant for WMS to explore what’s on the market or reach out to WMS experts at Generix Group North America.
France’s electronic invoicing reform relies on a Y-architecture, where Partner Dematerialization Providers (PDPs) play a central role in issuing and…
The B2B mandate in Germany, set to take effect on January 1, 2025, marks a crucial step in the European…
Following the October 15 announcement regarding the abandonment of the PPF development, the DGFIP and its partner AIFE are ramping…
Work with our team to build your ideal supply chain software stack and tailor it to your unique business needs.