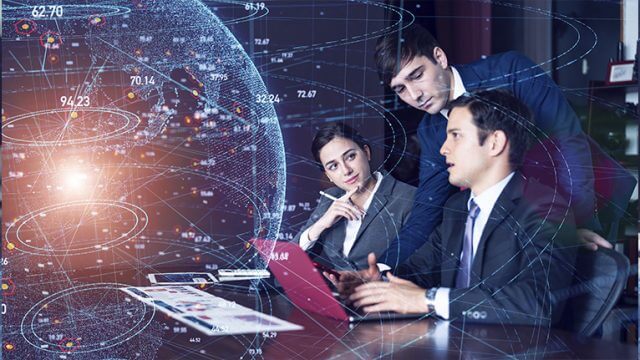
E-Invoicing and Its Geopolitical Stakes
France’s electronic invoicing reform relies on a Y-architecture, where Partner Dematerialization Providers (PDPs) play a central role in issuing and…
Generix Announces the Appointment of Olivier Vaillancourt as General Manager for North America View the press release
When choosing the right WMS for your business you should consider how a WMS will resolve your particle pain point and improve the rest of your warehouse. The right WMS should be both customizable and flexible enough to resolve any pain point in your operation now or in the future. It should also provide your business with the tools and resources to increase efficiency and expand.
An essential tool of any WMS is traceability. For inventory, QA, and recalls the ability to locate the item in real time anywhere within the warehouse whether it is in a location or with a worker is imperative. It’s also important to trace the history of your items. If an item is recalled or on QA hold the complete history of the item should be readily available, so that you can find a solution with as little interruption to the warehouse as possible.
Traceability is also the solution to minimizing incorrect and incomplete data. By tracing inventory through the warehouse in real time the WMS has many data points that the user can quickly and easily view. This provides a roadmap to quickly locate and fix any error.
The right WMS should be capable of expanding with your warehouse and growing into new areas. For example, if you are adding a new sales channel such as ecommerce, you will need a WMS capable of managing different vendors and workflows. In addition, a WMS capable of collecting and analyzing predictive data is important for any business relying on consumer demand. In turn, consumer demand drives the industry, any warehouse that can predict the consumer has an advantage over the competition.
Businesses utilizing just-in-time delivery should look for a WMS that has automated full cycle order management, along with the features listed above. Automated order management can greatly reduce any error in order fulfillment by quickly and automatically order items necessary to fulfill any order. Combine this feature with predictive analytics and your WMS can expand your business tremendously.
Natesan Andiyappillai published an article in the International Journal of Computer Applications. According to his research data analytics play a key role in optimizing logistics. He concluded that “Logistics business becomes complex due to globalization and ever-changing market and consumer behavior. And it is critical for the business not only to use the sophisticated IT WMS systems to capture the right data as much as possible but also to analyze the data extensively and optimize the logistics channel accordingly to be competitive in the market.”
As omni-channel driven demands become the norm, with resulting customer satisfaction harder to achieve, supply chain professionals need to leverage advanced WMS technology to keep their operations nimble, efficient, and scaling – especially in these volatile times.
Given Generix Group’s completeness of vision and ability to execute, as recognized once again by the Gartner analyst community, our Solochain WMS is well positioned to help companies needing a modern, flexible, and agile solution that can easily adapt to their changing needs.
We invite you to contact us to learn more.
France’s electronic invoicing reform relies on a Y-architecture, where Partner Dematerialization Providers (PDPs) play a central role in issuing and…
The B2B mandate in Germany, set to take effect on January 1, 2025, marks a crucial step in the European…
Following the October 15 announcement regarding the abandonment of the PPF development, the DGFIP and its partner AIFE are ramping…
Work with our team to build your ideal supply chain software stack and tailor it to your unique business needs.