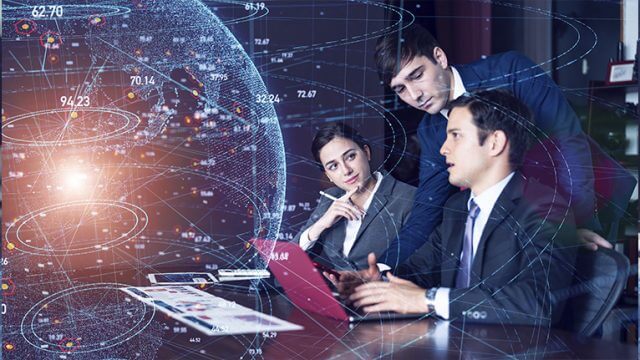
E-Invoicing and Its Geopolitical Stakes
France’s electronic invoicing reform relies on a Y-architecture, where Partner Dematerialization Providers (PDPs) play a central role in issuing and…
Medial International Chooses Generix Warehouse Management System (WMS) to Digitalize Its Logistics Operations Read the press release
Real-time inventory tracking stands as a cornerstone of effective warehouse management and is one of the most critical features of a Warehouse Management System (WMS). This feature ensures that every movement of inventory within the warehouse is accurately and instantaneously recorded, providing up-to-date information on stock levels.
The importance of real-time inventory tracking cannot be overstated. Traditional inventory management systems often rely on periodic updates, which can lead to discrepancies between actual and recorded stock levels. These discrepancies can result in costly issues such as stockouts, where demand cannot be met due to insufficient inventory, or overstocking, where excess inventory ties up capital and storage space unnecessarily.
A WMS equipped with real-time tracking uses advanced technologies like barcode scanners, RFID tags, and IoT sensors to monitor inventory as it moves through various stages—receiving, storage, picking, packing, and shipping. This immediate visibility into inventory levels helps warehouse managers make informed decisions, reducing the need for manual checks and significantly lowering the risk of human error.
Furthermore, real-time inventory tracking enhances order accuracy, a crucial factor in customer satisfaction. When a customer places an order, the system quickly verifies if the item is in stock and allocates it for fulfillment. The inventory count is instantly updated to reflect this change, ensuring that subsequent orders are processed with the most accurate data. This real-time capability also plays a vital role in preventing the common issue of “phantom inventory,” where products appear to be available in the system but are actually out of stock.
Additionally, this feature enables better demand forecasting and replenishment planning. By analyzing real-time data, businesses can identify trends and adjust their inventory levels proactively, avoiding both shortages and surpluses. This capability is particularly beneficial for businesses that deal with seasonal fluctuations or promotions, where demand can spike unexpectedly.
The automation of picking and packing processes within a WMS is pivotal for enhancing operational efficiency and accuracy in warehouse management. This feature leverages advanced technologies such as barcode scanning, voice-directed picking, and even robotics to streamline the order fulfillment process.
Manual picking and packing are traditionally labor-intensive and prone to errors. Mis-picks or incorrect packing can lead to customer dissatisfaction, increased return rates, and additional costs. Automated picking and packing minimize these risks by ensuring that the correct items are selected and packed according to predefined instructions.
For instance, barcode scanning during the picking process ensures that the picker selects the right item from the correct location. Voice-directed picking systems, which use voice commands to guide pickers to the appropriate items, further enhance accuracy by reducing reliance on manual data entry. In more advanced setups, robotics can be employed to automate the entire picking and packing process, significantly speeding up operations and reducing labor costs.
This automation not only increases order accuracy but also significantly boosts productivity. The time required to locate, pick, and pack items is reduced, allowing for faster order processing. This speed is particularly beneficial in high-volume warehouses or during peak seasons, where the demand for quick order fulfillment is critical.
Moreover, automated systems can be programmed to optimize the picking route within the warehouse, reducing travel time for workers and ensuring that orders are fulfilled as efficiently as possible. By minimizing the distance traveled and the time spent on each order, warehouses can handle a larger volume of orders without increasing labor costs.
Automation also facilitates better packaging practices. Automated packing systems can determine the optimal box size based on the dimensions of the items being packed, which reduces shipping costs and ensures that products are securely packaged, minimizing the risk of damage during transit.
Advanced reporting and analytics are indispensable WMS features that empower warehouse managers with the >supply chain management, having access to detailed analytics is crucial for maintaining a high level of operational efficiency. Advanced analytics tools within a WMS can process vast amounts of data generated by warehouse activities and present it in a format that is easy to understand and actionable.
For example, a WMS can generate reports that highlight trends in order accuracy, allowing managers to identify recurring issues and implement corrective actions. Similarly, analytics on picking times can help managers optimize labor allocation, ensuring that resources are used effectively during peak periods.
One of the key benefits of advanced reporting is the ability to forecast demand more accurately. By analyzing historical data and identifying patterns, a WMS can predict future demand trends, enabling managers to adjust inventory levels accordingly. This foresight helps prevent stockouts and overstocking, ensuring that inventory is always aligned with demand.
Moreover, these reports can be customized to meet the specific needs of different stakeholders within the organization. For example, a warehouse manager might focus on operational metrics, while an executive might be more interested in financial performance indicators. The flexibility to tailor reports ensures that everyone in the organization has the information they need to make informed decisions.
Analytics also play a crucial role in continuous improvement initiatives. By regularly reviewing performance data, managers can identify areas for improvement and track the effectiveness of changes over time. This iterative approach to optimization ensures that the warehouse remains agile and responsive to changing business needs.
Warehouse layout optimization is a strategic WMS feature that directly impacts the efficiency and productivity of warehouse operations. This functionality helps design and maintain the most efficient layout for a warehouse, taking into consideration factors such as physical space constraints, product dimensions, and movement patterns within the warehouse.
The layout of a warehouse plays a critical role in determining how quickly and efficiently items can be picked, packed, and shipped. A poorly designed layout can lead to increased travel time for workers, congestion in high-traffic areas, and delays in order fulfillment. Conversely, an optimized layout minimizes these issues, resulting in faster processing times and reduced operational costs.
A WMS with layout optimization capabilities uses algorithms to analyze the flow of goods through the warehouse and recommends the best placement for inventory based on factors such as picking frequency, size, and weight. For instance, fast-moving items might be placed closer to the packing stations, while bulkier items might be stored in areas that are easily accessible by forklifts. This optimization also considers the ergonomics of workers, ensuring that heavy or frequently picked items are stored at heights that minimize strain and reduce the risk of injury. By improving the overall layout, warehouses can enhance worker productivity, reduce fatigue, and improve safety.
Additionally, layout optimization can help warehouses maximize the use of their available space. By strategically placing shelving units and storage racks, a WMS can ensure that every square foot of the warehouse is utilized effectively. This is particularly important in warehouses with limited space, where efficient use of available space can delay or eliminate the need for costly expansions.
Furthermore, an optimized layout supports smoother workflows and reduces bottlenecks, ensuring that multiple processes—such as receiving, picking, packing, and shipping—can occur simultaneously without interfering with each other. This holistic approach to layout design enhances the overall efficiency of the warehouse and contributes to faster order fulfillment.
For a WMS to fully realize its potential in improving warehouse operations, it must integrate seamlessly with other critical systems within the organization, particularly Enterprise Resource Planning (ERP) systems. This integration ensures that all departments, from procurement to sales, have access to consistent, accurate, and real-time data, enabling better coordination and decision-making.
Integration with an ERP system allows the WMS to pull and push data between the warehouse and other business functions. For instance, when inventory levels are updated in the WMS after an order is fulfilled, this information is automatically reflected in the ERP system, ensuring that procurement is aware of stock levels and can reorder products as necessary.
This seamless data exchange eliminates the risk of data silos, where different departments operate based on outdated or inconsistent information. It also reduces the need for manual data entry, minimizing the potential for errors and ensuring that business decisions are based on the most accurate data available.
Moreover, integration with other systems such as Transportation Management Systems (TMS) and Customer Relationship Management (CRM) tools further enhances the efficiency of warehouse operations. For example, integration with a TMS allows the WMS to coordinate with transportation schedules, ensuring that shipments are prepared and loaded according to carrier timelines. Similarly, integration with CRM systems ensures that customer order history and preferences are taken into account during the fulfillment process, leading to better customer service.
This level of integration also facilitates end-to-end visibility across the supply chain. With all systems connected, managers can track an order from the moment it is placed to the time it is delivered to the customer. This visibility not only improves operational efficiency but also enhances the ability to respond to issues such as delays or inventory shortages in real-time.
Finally, a well-integrated WMS contributes to more effective financial management. By providing accurate, real-time data on inventory levels, labor costs, and other key metrics, it supports better budgeting, forecasting, and financial reporting. This integration ensures that the warehouse not only operates efficiently but also contributes positively to the overall financial health of the organization.
Task management and prioritization features in a WMS allow you to assign and manage tasks efficiently within your warehouse. This functionality enables warehouse managers to prioritize tasks based on urgency, order deadlines, or customer importance. It also provides real-time visibility into task progress, allowing for better resource allocation and time management. By ensuring that the most critical tasks are completed first, you can enhance overall productivity and meet customer expectations more effectively.
Labor management is a crucial aspect of warehouse operations that directly impacts productivity, efficiency, and cost-effectiveness. A WMS with robust labor management features enables warehouse managers to monitor workforce performance, optimize labor allocation, and ensure that the right resources are in place to meet operational demands.
One of the primary benefits of labor management within a WMS is the ability to track employee activities in real-time. This feature allows managers to monitor tasks such as picking, packing, and inventory replenishment, providing insights into how long each task takes and where inefficiencies may exist. By analyzing this data, managers can identify opportunities for improvement, such as streamlining workflows or providing additional training to employees who may be struggling with certain tasks.
Labor management features also support better labor forecasting and scheduling. By analyzing historical data and current demand levels, a WMS can predict future labor needs, ensuring that the warehouse is adequately staffed during peak periods and that labor costs are minimized during slower times. This predictive capability helps warehouses avoid the costly mistakes of overstaffing or understaffing, both of which can negatively impact productivity and profitability.
Additionally, labor management tools often include performance metrics that allow managers to evaluate individual and team performance. These metrics can be used to set benchmarks, reward high-performing employees, and identify areas where additional support may be needed. By fostering a culture of continuous improvement, labor management features contribute to higher levels of employee engagement and satisfaction.
Moreover, effective labor management within a WMS helps reduce operational costs. By optimizing labor allocation and minimizing downtime, warehouses can achieve higher levels of productivity without increasing labor costs. This efficiency is particularly important in industries with tight margins, where even small improvements in labor utilization can have a significant impact on the bottom line.
Cycle counting is a critical WMS feature that helps maintain high levels of inventory accuracy without the need for full-scale physical inventory counts. This process involves counting a small subset of inventory items on a regular, rotating basis, allowing discrepancies to be identified and corrected quickly.
Inventory accuracy is essential for efficient warehouse operations. Inaccurate inventory counts can lead to stockouts, overstocking, and errors in order fulfillment, all of which can negatively impact customer satisfaction and profitability. Cycle counting provides a proactive approach to inventory management, ensuring that discrepancies are identified and addressed before they become major issues.
A WMS with cycle counting capabilities can automate the entire process, selecting which items to count based on factors such as turnover rates, value, and historical accuracy. This automation reduces the burden on warehouse staff, allowing them to focus on other tasks while still maintaining high levels of inventory accuracy.
Moreover, cycle counting allows warehouses to maintain accurate inventory records without the need for disruptive full-scale physical counts. Full physical counts often require warehouses to shut down operations temporarily, leading to lost productivity and potential delays in order fulfillment. Cycle counting, on the other hand, can be performed continuously without interrupting normal warehouse operations, ensuring that inventory accuracy is maintained at all times.
Cycle counting also provides valuable data that can be used to improve other aspects of warehouse management. For example, if certain items are consistently found to have discrepancies, this may indicate issues with the receiving process, storage conditions, or picking accuracy. By analyzing cycle counting data, warehouses can identify and address these underlying issues, leading to overall improvements in inventory management.
Returns management is a critical feature in any WMS, especially given the increasing prevalence of e-commerce, where returns are a significant part of the customer experience. Effective returns management ensures that returned goods are processed efficiently, minimizing the impact on inventory levels and reducing the potential for revenue loss.
Handling returns can be a complex and resource-intensive process. Without a robust WMS in place, returns can lead to errors in inventory records, delays in processing, and customer dissatisfaction. A WMS with returns management capabilities streamlines this process, ensuring that returned items are quickly received, inspected, and either restocked or disposed of according to predefined criteria.
For instance, when a return is initiated, the WMS can automatically generate a return authorization and guide the warehouse staff through the steps required to process the return. This includes updating inventory records, inspecting the returned items for damage, and determining whether the items can be restocked or need to be sent to a secondary market or disposed of.
Effective returns management also enhances customer satisfaction by ensuring that returns are processed quickly and accurately. Customers who receive timely refunds or replacements are more likely to return for future purchases, making returns management a key component of customer retention strategies.
Moreover, a WMS with returns management capabilities can provide valuable insights into return trends. By analyzing return data, businesses can identify common reasons for returns, such as product defects, incorrect orders, or issues with packaging. This information can be used to address underlying problems, reduce the rate of returns, and improve overall product quality and customer satisfaction.
Scalability and flexibility are crucial features of a WMS that ensure your warehouse management system can grow and adapt as your business evolves. These features allow a WMS to handle increased inventory, additional warehouses, and more complex processes without requiring a complete system overhaul.
As businesses expand, their warehouse operations often become more complex. New products, increased order volumes, and additional distribution channels can all strain existing systems. A WMS with scalability ensures that your system can handle these increased demands without sacrificing performance. For example, a scalable WMS can easily accommodate the addition of new warehouses, allowing you to manage multiple locations from a single system.
Flexibility, on the other hand, allows your WMS to adapt to changing business needs and industry standards. This includes integrating with new technologies, such as robotics or AI-driven analytics, and supporting new processes, such as omnichannel fulfillment. A flexible WMS can also easily adapt to changes in order volumes, seasonal fluctuations, and evolving customer expectations.
Moreover, scalability and flexibility are essential for businesses that operate in dynamic markets. As customer demands and industry trends shift, a flexible WMS allows you to respond quickly and efficiently, maintaining a competitive edge. This adaptability is particularly important for businesses that experience rapid growth or operate in highly competitive industries.
France’s electronic invoicing reform relies on a Y-architecture, where Partner Dematerialization Providers (PDPs) play a central role in issuing and…
The B2B mandate in Germany, set to take effect on January 1, 2025, marks a crucial step in the European…
Following the October 15 announcement regarding the abandonment of the PPF development, the DGFIP and its partner AIFE are ramping…
Work with our team to build your ideal supply chain software stack and tailor it to your unique business needs.