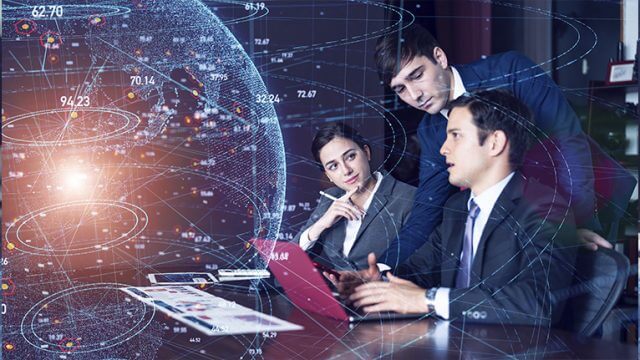
E-Invoicing and Its Geopolitical Stakes
France’s electronic invoicing reform relies on a Y-architecture, where Partner Dematerialization Providers (PDPs) play a central role in issuing and…
Medial International Chooses Generix Warehouse Management System (WMS) to Digitalize Its Logistics Operations Read the press release
Short of deploying an army of robots in their facilities – a solution that remains out of reach for most, to say the least, manufacturers will have to be creative to meet their business objectives. In a world of labor scarcity, it’s the companies that will find and implement the means to reduce their dependence on a large workforce that will gain competitive advantage.
While a fully automated manufacturing environment is beyond most manufacturers’ means, solutions to implement advanced productivity practices that maximize resource utilization are not. SOLOCHAIN WMS software, for instance, enables manufacturers to implement task interleaving in their operation.
Task interleaving is a best practice operating strategy that minimizes deadheading, that is, the time employees spend moving about the facility without accomplishing any useful task along the way. Through task interleaving, operators can effectively weave together, so to speak, activities that traditionally were separated threads – e.g., receiving, put away, picking, staging, loading, or cycle counts. Ultimately, task interleaving makes it possible for a manufacturer to:
On average, employees in manufacturing environments tasked with selecting and fulfilling orders spend about half their time walking. Let that sink in: nearly half the investment you make in your workforce is spent on employees walking around the warehouse. Consider that labor expenses typically account for 35% to 65% of a manufacturer’s distribution and fulfilment costs, and you quickly realize that this is a lot of your capital wasted on unproductive walking! In large facilities where the layout is not optimized and the levels of technological maturity are low, that amount can quickly reach catastrophic heights.
The lesson to draw from this is simple: cut on the time employees spend walking from task to task, optimize and streamline their movements across your operation, and not only do you maximize resource utilization, but you also stand to make significant savings on operating costs.
Say, for example, that an employee has just finished picking items from a SKU location adjacent to another location that has not been cycle counted in some time. Should it not interfere with other priorities, it makes sense for that employee to perform said count: it avoids travel time at a later moment and maximizes the value of their current location in the warehouse.
That’s exactly what task interleaving does. As soon as an employee completes a task, they’re assigned a new one based on their current location in the warehouse, the type of equipment they were using, and/or the company’s current operational priorities.
Of course, the trick to task interleaving is being able to identify the most valuable task an employee can perform once their current assignment has been carried out. To that end, manufacturers need accurate operational intelligence—the kind of intelligence only a WMS like SOLOCHAIN can provide.
Task interleaving requires a powerful warehouse management task management engine. Run of the mill WMS solutions adequately support tasks in a distribution center so long as different activities remain siloed. A more powerful system is necessary, however, to weave these activities together. Among other things, the WMS must be able to locate employees as they progress through their activities and to intelligently determine the next task they should be assigned.
In manufacturing environments, efficient task interleaving should also leverage a manufacturing execution system. The better a WMS and an MES are integrated, the more efficiently task interleaving optimizes a manufacturer’s operation. SOLOCHAIN is a powerful WMS with native MES capabilities. Thanks to such levels of integration, it effectively unlocks task interleaving capabilities in a manufacturing environment beyond what other WMS of its category can achieve.
Through proper configuration, the SOLOCHAIN WMS/MES generates task queues that consider production and distribution priorities to help manufacturers meet their KPIs. SOLOCHAIN then intelligently assigns the queued tasks to employees taking into account these priorities as well as employee location and/or the material handling equipment they were using or that is available nearby.
Employees receive their task assignment on SOLOCHAIN enabled handheld mobile devices, the same one that normally supports their activities. Once a task is completed, employees use their device to scan the appropriate barcode and inform SOLOCHAIN of their current status. The WMS then assigns a new task that optimizes and streamlines their movements on the warehouse floor.
To a certain extent, SOLOCHAIN also anticipates changing operating conditions. For example: the WMS can be configured to distinguish between temporary and permanent employees in task attribution. Given that temporary task forces often don’t have a forklift license, being able to make that difference leads to more intelligent task assignments. This is useful to manufacturers who are particularly affected by seasonality or susceptible to sudden peaks in demand.
As with any other significant improvement to a manufacturer’s operation, the implementation of task interleaving can be a bit of a challenge at first. Employees must be trained to perform a larger set of tasks; managers must get acquainted with the new system and adapt to a new flow of activities; task schedules may need to be adjusted; etc.
The impacts of such challenges can be attenuated, however, through close collaboration with the WMS ’s implementation team. By setting up a rich feedback loop with the solution provider, user acceptance comes faster and SOLOCHAIN’s configuration is even more finely attuned to your requirements.
Manufacturers should also keep in mind that their facility’s physical layout and MHE will impact their ROI. Take dock configurations, for example: task interleaving is much more efficiently implemented where receiving and shipping docks are close together. An implementation team that has deep sector expertise will help manufacturers gain valuable insights on available solutions that maximize the benefits they will draw from task interleaving.
To learn more about what eCommerce-specific capabilities can do in a WMS, visit the Generix Group SOLOCHAIN WMS page, or download the SOLOCHAIN WMS Product Sheet.
France’s electronic invoicing reform relies on a Y-architecture, where Partner Dematerialization Providers (PDPs) play a central role in issuing and…
The B2B mandate in Germany, set to take effect on January 1, 2025, marks a crucial step in the European…
Following the October 15 announcement regarding the abandonment of the PPF development, the DGFIP and its partner AIFE are ramping…
Work with our team to build your ideal supply chain software stack and tailor it to your unique business needs.