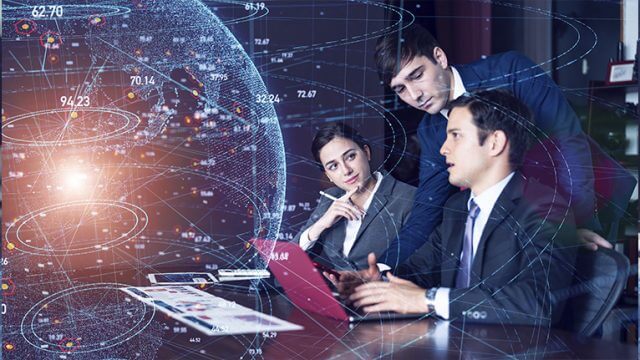
E-Invoicing and Its Geopolitical Stakes
France’s electronic invoicing reform relies on a Y-architecture, where Partner Dematerialization Providers (PDPs) play a central role in issuing and…
Generix Announces the Appointment of Olivier Vaillancourt as General Manager for North America View the press release
Warehouse Management Systems (WMS) are pivotal in the landscape of global trade, underpinning the complex web of supply chain operations. These systems act as the digital backbone of warehouses, optimizing tasks ranging from inventory management to order fulfillment, thereby ensuring the efficient movement of goods from suppliers to consumers. In an era marked by rapid e-commerce growth and global supply chains’ expansion, the role of WMS has become more critical than ever.
WMS technology provides real-time data on inventory levels, order status, and worker productivity, enabling warehouses to respond swiftly to changes in demand and operational challenges. This real-time visibility into warehouse operations helps businesses prevent stockouts, reduce excess inventory, and improve order processing times, directly contributing to customer satisfaction and operational efficiency. By leveraging sophisticated algorithms and data analytics, WMS solutions can predict demand trends, optimize inventory placement, and streamline picking routes, thereby reducing operational costs and enhancing productivity.
Warehouse Management Systems (WMS) revolutionize the management and operations of warehouses by automating and optimizing various warehousing tasks. At its core, a WMS orchestrates the flow of products through a warehouse in the most efficient manner possible, from receiving and storing to picking, packing, and shipping.
WMS starts by integrating with other business systems such as Enterprise Resource Planning (ERP) and Transportation Management Systems (TMS). This integration ensures seamless data flow and real-time visibility across the supply chain. Upon arrival, goods are registered in the WMS using barcodes or RFID tags, which immediately update inventory levels and locations. This integration allows for accurate data capture and efficient information sharing across different departments.
Real-time inventory tracking is a standout feature of WMS. The system continuously monitors stock levels, locations, and movements within the warehouse. This capability prevents stock discrepancies, enables accurate forecasting, and ensures that inventory data is always up to date. Managers can quickly identify slow-moving items, optimize inventory turnover rates, and maintain optimal inventory levels to ensure timely replenishment.
When goods arrive at the warehouse, they are registered in the WMS, which determines the optimal storage location based on predefined criteria such as product type, size, and demand. This strategic placement ensures that items are stored efficiently and are easily retrievable, reducing the time and effort required for future picking and packing processes.
WMS optimizes the order fulfillment process through several advanced features:
The WMS guides warehouse workers to the items’ locations using the most efficient routes, managing the packing processes to ensure orders are accurately consolidated for shipment. This includes selecting optimal package sizes based on product dimensions and transportation costs, enhancing packing efficiency and reducing shipping expenses.
Integration with TMS allows for the seamless creation of shipping documentation and real-time tracking of shipments. This integration enhances the accuracy and speed of the order fulfillment process, ensuring that customers receive their orders on time. The WMS organizes shipments according to departure time and fulfillment priority, optimizing the loading process and maximizing delivery efficiency.
Modern WMS leverages automation and robotics to enhance efficiency further:
Efficient labor management is crucial for warehouse operations. WMS monitors warehouse activities, identifies productivity gaps, and optimizes task allocation among workers. By balancing workloads and prioritizing tasks based on skill levels, WMS improves overall efficiency and reduces labor costs. The system tracks key performance indicators (KPIs) such as order accuracy, task completion times, and labor utilization, providing insights into labor productivity.
WMS systems collect vast amounts of data, which are analyzed to produce insights into warehouse operations. This includes tracking KPIs such as order accuracy, inventory levels, and shipping timeliness. These insights facilitate informed decision-making, helping managers optimize workflows and enhance operational efficiency. Real-time reporting provides a clear and visual overview of warehouse performance, enabling continuous improvement and strategic planning.
At its core, a WMS provides unparalleled visibility into a warehouse’s inventory, tracking the movement of goods from the moment they enter the warehouse until they’re dispatched. This real-time tracking is crucial for maintaining optimal stock levels, reducing instances of overstocking or stockouts, and ensuring that inventory is replenished in a timely manner.
By automating processes such as inventory receiving, shipping, picking, and packing orders, WMS not only accelerates these operations but also minimizes human error. Automated picklists, for example, guide warehouse staff to efficiently pick items for shipping, significantly speeding up order fulfillment.
A WMS provides critical insights into labor management, allowing for the optimization of workforce allocation and tasks. By identifying productivity gaps and analyzing trends, warehouse operations can be leaner and more efficient, directly impacting the bottom line.
Modern WMS solutions often integrate seamlessly with other key business systems, such as transportation management and logistics software. This integration fosters a cohesive supply chain ecosystem, facilitating smoother operations and improving overall efficiency.
Adherence to local regulations and standards is simplified with a WMS, thanks to its ability to record and manage real-time data, making audits more straightforward and ensuring compliance with industry standards.
Implementing and utilizing a Warehouse Management System effectively involves several key steps to ensure that it aligns with a warehouse’s operational needs and enhances its efficiency.
Utilizing a WMS effectively requires a strategic approach, starting with selecting the right system and ensuring it is configured to meet specific warehouse needs. Proper training and integration with other systems are crucial for maximizing the benefits of a WMS, as is ongoing optimization to adapt to changing operational demands.
Warehouse management systems can be broadly categorized into three main types, each offering unique benefits tailored to different operational needs and business scales:
These systems are designed to focus solely on warehouse management tasks. Standalone WMS offers deep functionality and can be highly customized to fit specific warehouse operations. They typically require significant upfront investment in software and hardware, and while they offer robust control over data and processes, they may pose challenges in terms of integration with other business systems.
Cloud solutions provide a flexible, scalable approach to warehouse management. With lower initial costs and a subscription-based pricing model, cloud-based WMS can be quickly deployed and easily scaled up or down based on business needs. These systems are maintained off-site, with the service provider handling updates and security, offering businesses the ability to access their WMS from anywhere, at any time. This model supports real-time data access and collaboration across multiple locations, making it ideal for businesses with growing or fluctuating demand.
These solutions are part of broader Enterprise Resource Planning (ERP) systems, offering seamless integration with various business processes such as finance, HR, and procurement. ERP-integrated WMS solutions can provide a unified view of the business operations, enhancing data accuracy and process efficiency. However, they may not offer the depth of features specific to standalone WMS solutions but benefit from streamlined data flow and reduced IT complexity. This integration can lead to more cohesive decision-making across the supply chain.
Each type of WMS solution presents distinct advantages and challenges. Standalone systems offer deep customization and control, making them suitable for large operations with complex needs. Cloud-based solutions are flexible and scalable, perfect for businesses seeking rapid deployment and growth adaptation. ERP-integrated systems offer comprehensive integration across business functions, ideal for organizations looking for a unified business management approach. The choice among these options depends on the specific requirements, budget, and strategic goals of a business, emphasizing the need for careful consideration to select the most appropriate WMS solution.
The evolution of WMS is tightly linked to advancements in technology. Future warehouses may incorporate Internet of Things (IoT), blockchain, and augmented reality technologies to further enhance the capabilities of WMS solutions. These technologies promise to introduce new levels of efficiency, from AI-driven decision support to real-time monitoring and predictive analytics.
As warehouses continue to evolve, the role of WMS in facilitating efficient, error-free, and compliant warehouse operations becomes increasingly indispensable. By harnessing the power of real-time data, automation, and integration, WMS stands as a cornerstone of modern warehousing, promising a future where operational efficiency is continuously optimized.
France’s electronic invoicing reform relies on a Y-architecture, where Partner Dematerialization Providers (PDPs) play a central role in issuing and…
The B2B mandate in Germany, set to take effect on January 1, 2025, marks a crucial step in the European…
Following the October 15 announcement regarding the abandonment of the PPF development, the DGFIP and its partner AIFE are ramping…
Work with our team to build your ideal supply chain software stack and tailor it to your unique business needs.