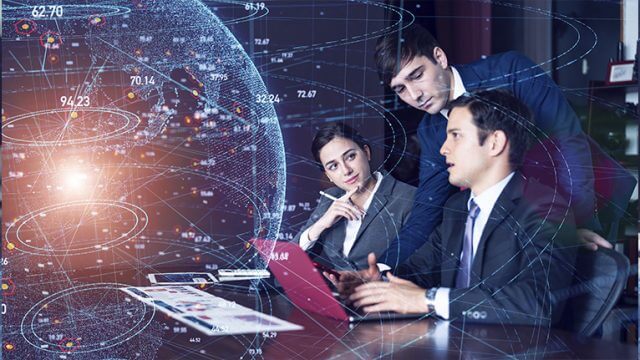
E-Invoicing and Its Geopolitical Stakes
France’s electronic invoicing reform relies on a Y-architecture, where Partner Dematerialization Providers (PDPs) play a central role in issuing and…
Generix Delivers Schematron for Electronic Invoicing to AFNOR to Ensure Interoperability Between PDPs Read the press release
Warehouse automation refers to the use of technology to streamline and automate the movement of inventory into, within, and out of warehouses to customers with minimal human intervention. This process involves implementing machines, software, and technology to perform tasks traditionally executed by human workers, thus reducing labor-intensive duties and minimizing errors.
Automated systems track the movement and storage of goods, ensuring accurate and up-to-date inventory records. This reduces the likelihood of stockouts or overstock situations, which can disrupt operations and increase costs.
Automation streamlines the process of receiving, processing, and fulfilling orders. Systems like AS/RS and AGVs ensure that goods are picked, packed, and shipped efficiently, reducing order processing time and increasing throughput.
Automated quality checks at various stages of the warehouse process help in identifying defects early and preventing defective products from reaching customers. This ensures that all products meet quality standards before they are shipped.
Automation provides end-to-end traceability of materials and products throughout the warehouse, enhancing the ability to track and recall items as needed. This is crucial for maintaining quality control and compliance with industry regulations.
Automated systems collect and analyze data in real-time, providing insights into operational performance. This approach helps businesses identify inefficiencies, optimize processes, and make informed decisions to improve overall performance.
Automation significantly enhances operational efficiency by reducing the need for manual intervention. Technologies like barcode scanning, RFID tagging, and conveyor systems streamline inventory tracking and order processing, ensuring that tasks are completed faster and more accurately.
By leveraging real-time data, warehouse automation ensures that inventory records are accurate and up-to-date. This accuracy is critical for maintaining optimal stock levels and preventing production delays caused by material shortages. Automated systems reduce the likelihood of mistakes in data entry and inventory tracking, thereby improving the reliability of inventory information.
Automation helps in reducing operational costs by optimizing inventory levels and improving order accuracy. By preventing overstocking and stockouts, businesses can lower storage costs and avoid the expenses associated with rush orders. Additionally, the automation of warehouse tasks reduces labor costs and enhances productivity.
Automated systems provide comprehensive reporting and analytics tools that offer insights into warehouse operations. Managers can access real-time data on inventory levels, order status, and production schedules, enabling better decision-making and financial planning. This visibility helps in identifying inefficiencies and implementing corrective measures to improve overall performance.
Warehouse automation systems incorporate advanced security features to protect sensitive data and ensure compliance with industry regulations. Secure access controls and audit trails help in monitoring user activity and preventing unauthorized access to critical information. These security measures are essential for safeguarding company assets and maintaining regulatory compliance.
Warehouse automation can significantly enhance operational efficiency, reduce costs, and improve accuracy. Implementing automation, however, requires a strategic approach to ensure that the transition is smooth and effective. Here’s a detailed guide on how to automate a warehouse, focusing on evaluating needs, researching technologies, selecting the right solutions, developing a change management plan, implementing in phases, and continuous improvement.
The first step in automating a warehouse is to evaluate current operations to identify areas where automation can provide the most benefit. This involves a thorough analysis of the existing processes, workflows, and pain points.
Explore the latest warehouse automation technologies and solutions available in the market. This research phase is crucial to understanding what technologies can address your specific needs and how they can be integrated into your operations.
Choosing the right technologies is critical for a successful automation implementation. The solutions you select should be flexible, scalable, and capable of growing with your business.
A comprehensive change management plan is essential to ensure a smooth transition to automated processes. This involves preparing the organization for the changes and managing the impact on employees.
Implementing warehouse automation in phases allows for a controlled and manageable transition. Start with core tasks and gradually expand automation to more complex processes.
Regularly assess and optimize the performance of automated systems to ensure they continue to meet business needs and deliver expected benefits.
By following these steps, businesses can effectively automate their warehouses, resulting in enhanced operational efficiency, reduced costs, and improved accuracy. Implementing warehouse automation is a strategic investment that can deliver significant long-term benefits.
France’s electronic invoicing reform relies on a Y-architecture, where Partner Dematerialization Providers (PDPs) play a central role in issuing and…
The B2B mandate in Germany, set to take effect on January 1, 2025, marks a crucial step in the European…
Following the October 15 announcement regarding the abandonment of the PPF development, the DGFIP and its partner AIFE are ramping…
Work with our team to build your ideal supply chain software stack and tailor it to your unique business needs.