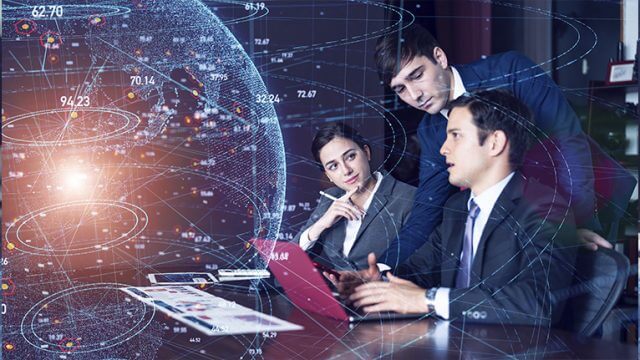
E-Invoicing and Its Geopolitical Stakes
France’s electronic invoicing reform relies on a Y-architecture, where Partner Dematerialization Providers (PDPs) play a central role in issuing and…
Generix Announces the Appointment of Olivier Vaillancourt as General Manager for North America View the press release
Although mechanization offers a plethora of advantages from an operational standpoint, it can be quite limiting for warehouse managers. This should be kept in mind when gauging the return on investment of a warehouse automation system.
A major advantage of automated warehouses is their capacity to improve productivity, counter hiring difficulties during activity peaks and reduce arduous working conditions by eliminating some low value-added tasks. Mechanization can also be useful when taking on cost issues and scarcity of space, since several solutions offer a storage densification feature.
The notion of rate of service is now omnipresent in logistics strategy. In today’s world, it is imperative to improve the quality of services provided by reducing the number of execution errors. This paves the way for automation by taking increasingly heavy pressure off the shoulders of supply chain operators.
Even with a tax credit, the costs for an automation project are quite high, especially when e-commerce operations are involved. Online sales often make for orders that are extremely resource-heavy. It’s why e-commerce order preparation is for the most part manual, except in some countries like China, where logistics chains generally deal with enormous volumes.
Once automated, system maintenance can also be quite complex to manage. To maintain operational capacity in the event of breakdown, companies must react quickly and consider escalation situations. Additionally, warehouse automation can reduce process flexibility. An automated system is more difficult to modify, and can prevent a company from growing.
There’s also the question of profitability during quieter periods in sectors highly subject to seasonal sales. Despite systems being sized to respond to peaks in activity, a warehouse’s equipment could be underused during such lulls. It is advisable to automate on the basis of an average period of business and to compensate for needs with alternative or temporary hiring solutions.
Whatever the case, the connection of automated devices to an information system must be an anticipated, planned event. Prior to implementation, equipment must be compatible and able to interface with the warehouse management system (WMS) in use.
Many technical solutions on the market today facilitate warehouse automation, storage, and merchandise reception during order preparation.
Generally, receiving merchandise in a warehouse offers little potential for automation. Warehouse automation solutions include the use of conveyors to route boxes at unloading time. Other conveyors can then store products automatically. This is a “basic” type of mechanization which, in some cases, does not require any interaction with the information system.
There are also several mechanization solutions to optimize storage operations. These are automated systems that move through aisles picking up and dropping off products from storage locations. Some systems manage palettes, boxes, or unitary products stored in plastic cases. They are fairly speedy and sophisticated enough to meet specific needs.
Several technologies are grouped under this umbrella:
Palette receiver cranes. A mechanized arm with forks moves palettes around. These cranes exist in either single or double depth. They can often be seen in the mass distribution sector, where a massive flow of full-range palettes are managed.
Mini-load. A shuttle equipped with pick-up arms can handle 1, 2, or 3 boxes. Several technologies are present on the market and differ in their grip techniques, the system’s ability to raise itself, and whether they are managed with or without a skid.
Multi-shuttle. Plastic case products can be handled with these shuttles. The technology is perfectly suited to low-weight and low-volume products and offers fast speeds. Such shuttles are often used in the pharmaceutical sector.
Carousel. With this device, the storage system moves as a whole to bring the right case to the pick-up/drop-off location at the head of the aisle. Cases are usually multi-reference, meaning that several product types are stored in a single one. The system implemented by the mechanic can select products that differ visually, in such a way to prevent picking errors before they reach the production line.
France’s electronic invoicing reform relies on a Y-architecture, where Partner Dematerialization Providers (PDPs) play a central role in issuing and…
The B2B mandate in Germany, set to take effect on January 1, 2025, marks a crucial step in the European…
Following the October 15 announcement regarding the abandonment of the PPF development, the DGFIP and its partner AIFE are ramping…
Work with our team to build your ideal supply chain software stack and tailor it to your unique business needs.