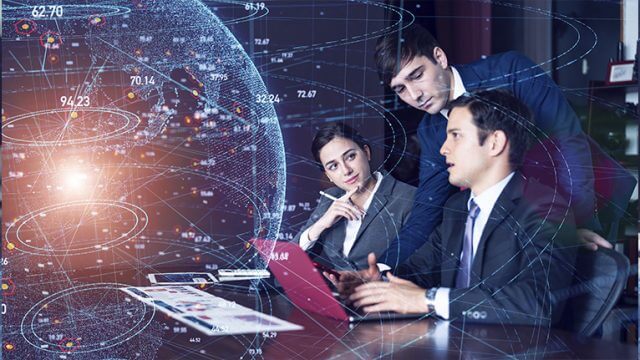
E-Invoicing and Its Geopolitical Stakes
France’s electronic invoicing reform relies on a Y-architecture, where Partner Dematerialization Providers (PDPs) play a central role in issuing and…
Medial International Chooses Generix Warehouse Management System (WMS) to Digitalize Its Logistics Operations Read the press release
Inventory should be consistently measured in several areas: turnover, carrying cost, and accuracy. Products that tend to stick around the warehouse longer than others are likely costing you more money than they are making you. If you have an accurate measurement of product turnover and how long items are being carried, then you can reevaluate your stocktaking and maintain a more efficient warehouse. The idea is to evaluate your customers’ preferences and habits, and stock accordingly.
In addition, integrating an automated way to measure your inventory’s accuracy, as opposed to the more traditional manual fashion, will help avoid unnecessary costs and maintain a more error-free and accurate stock in place.
This is an area that is often considered in hindsight, or at least second to higher profile areas such as the warehouse picking and shipping areas. However, receiving area inefficiencies can be felt all the way through the supply chain. It is an absolutely vital area of a warehouse and important measurements include cost per line item received, volume per man-hour, truck time at the dock, and accurate receipts.
Not the easiest area to measure, but it is possible. Put-away KPIs include cycle time or accuracy rate, cost per item put away, time from receiving to pick location, and put-away hourly labor rates.
Not surprisingly, the emphasis of accurately measuring order picking and packing KPIs is of utmost importance to most businesses. This is the most labor-intense and diverse area in the warehouse, and the one where performance directly relating to customer satisfaction can be evaluated. This is also the area which costs businesses the most, and inefficiencies cause a direct loss in profit. Important measurements include cost per line item picked, orders picked per hour, picking labor costs, consumable usage (such as packing materials and boxes), and cycle times per order. Also good to add is the percentage of perfect pick lines, with the aim of constantly increasing it. This area directly impacts the customer, as inaccurate picking and packing lead to errors in shipping and delivery, which should of course be avoided as much as possible.
Storage facilities may be operated via manual or automated systems, and both can be measured accurately via your WMS. Whether your system measures by block stacking or rack storage, or by unit, mini load, or carousel storage, good measurement indicators include storage cost per item, inventory storage per square foot, and days-on-hand.
The word “shipping” doesn’t convey all of the importance that it should, as this area comprises a lot more than just packing trucks and sending them off to customers or other areas of the chain. Excellent shipping metrics include cost per item shipped, cost per shipped order, labor hours consumed per order, percentage of perfect shipments, shipping dock utilization, and time from picked order to departure.
While the KPIs listed above are important measurements, this is not an exhaustive list. Other indicators that your WMS and TMS can measure include areas such as security, safety, employee satisfaction, carrier performance, and DOE fuel index. All in all, your KPIs are going to be an accurate measurement of your supply chain as a whole. Don’t neglect them!
France’s electronic invoicing reform relies on a Y-architecture, where Partner Dematerialization Providers (PDPs) play a central role in issuing and…
The B2B mandate in Germany, set to take effect on January 1, 2025, marks a crucial step in the European…
Following the October 15 announcement regarding the abandonment of the PPF development, the DGFIP and its partner AIFE are ramping…
Work with our team to build your ideal supply chain software stack and tailor it to your unique business needs.