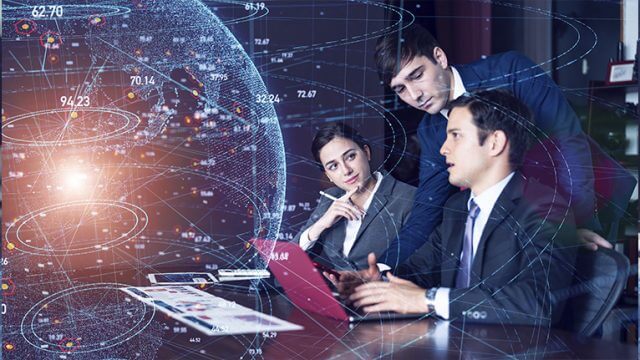
E-Invoicing and Its Geopolitical Stakes
France’s electronic invoicing reform relies on a Y-architecture, where Partner Dematerialization Providers (PDPs) play a central role in issuing and…
Generix Announces the Appointment of Olivier Vaillancourt as General Manager for North America View the press release
In a highly unpredictable year, companies were faced with a profound change in the way they worked that impacted processes, sales channels, and the entire value chain. It was a difficult year, and the learnings are ongoing in many companies. For many, adapting to pandemic times implied huge losses, transformation of the company’s core activities and a permanent uncertainty in terms of supplier reliability, distribution chains and consumer demand.
SMBs have been particularly affected by this conjuncture. Despite more flexible and agile structures – which are often true centers of innovation and resilience – smaller companies are much more exposed to the consequences of these turbulent times, with less room for protection and less capacity to respond financially to the point that many are facing bankruptcy.
2021 will be a crucial year of survival and overcoming. After the ‘shock’ of 2020, it is time to reflect on how to thrive in the current and future economic context and establish resilience strategies. Technology and the digital transformation of processes and operations are fundamental when building resilient supply chains.
The business world entered 2021 with little room for risk – especially when it comes to micro, small and medium-sized companies. It is necessary to do things differently, it is true, because the “normal” that used to guide us no longer exists – perhaps permanently – but with the care to invest in what really brings added value and ROI. Absolute focus is required to bet on the right solutions: those that will serve as leverage for a resilient performance and results onwards.
The strategy we recommend involves the implementation of solutions that streamline warehouse management, precisely because it is a way to reduce costs of logistics operations and gain profitability margins for the business. In addition to profitability and greater reliability in all processes, the adoption of specialized software allows to gain greater speed in responding to new consumer demands and new buying habits. It is worth remembering, by the way, the giant “leap” of eCommerce in 2020, which brings new challenges in terms of control and fast warehouse management and visibility throughout the value chain (including real-time tracking available to end consumers).
The management of logistics operations is particularly critical in times of pandemic, especially considering the disruptions in the value chain that we are witnessing throughout 2020. Traditional warehouse management models, which were already showing signs of inefficiency, are now proving to be obsolete and unable to respond to the new reality in which we live.
A new crisis-proof model supported by state-of-the-art digital tools is needed. A model that allows companies to automate processes and do more with less (increasing the capacity to receive, manage and send stock, and thereby accelerating sales), with fewer logistical errors (which invariably translate into costs and losses) and with a 360º vision throughout the value chain. And, what’s more, that allows to quickly adjust processes in a reality of great change and uncertainty.
For SMBs, adopting a warehouse management solution is even more of a priority. Managers of smaller companies often make the mistake of believing that this type of software only makes sense for large companies. On the contrary: it is in SMBs, usually with undersized teams and more limited resources, that every step counts towards greater efficiency and profitability. A stock error or the loss of an order due to lack of traceability or inventory visibility is a drop in the ocean for large companies. This can make all the difference in the tight treasury of a small company.
In this fight for the resilience of micro, small, and medium-sized businesses, you need to choose the right solution. A solution that is designed specifically to meet the needs and processes of an SMB – which, as we know, are very different from the logistics operations of large companies. As I mentioned before, 2021 is the time to invest and do better, but with the right strategy. Without this, the desired digital transformation will not bring the expected benefits.
Our WMS – Warehouse Management System is an example of a solution that brings added value to SMBs. With automated processes, optimization of space and resources in the preparation of orders, complete product traceability, synchronization of warehouse operations with the carriers’ timings and integration with existing production tools, this software brings new possibilities in terms of efficiency and cost savings to companies.
Generix Group North America provides a series of solutions within our Supply Chain Hub product suite to create efficiencies across an entire supply chain. From Warehouse Management Systems (WMS), Transportation Management Systems (TMS) to Manufacturing Execution Systems (MES), such platforms can deliver a wide range of benefits that ultimately flow to the warehouse operator’s bottom line. Our solutions are in use around the world and our experience is second-to-none. We invite you to contact us to learn more.
France’s electronic invoicing reform relies on a Y-architecture, where Partner Dematerialization Providers (PDPs) play a central role in issuing and…
The B2B mandate in Germany, set to take effect on January 1, 2025, marks a crucial step in the European…
Following the October 15 announcement regarding the abandonment of the PPF development, the DGFIP and its partner AIFE are ramping…
Work with our team to build your ideal supply chain software stack and tailor it to your unique business needs.