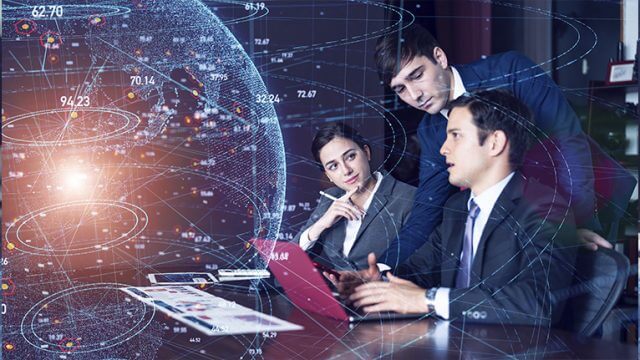
E-Invoicing and Its Geopolitical Stakes
France’s electronic invoicing reform relies on a Y-architecture, where Partner Dematerialization Providers (PDPs) play a central role in issuing and…
Generix Delivers Schematron for Electronic Invoicing to AFNOR to Ensure Interoperability Between PDPs Read the press release
Warehouse Management Systems (WMS) are software solutions designed to optimize warehouse operations. In the context of manufacturing, a WMS is used to manage and streamline the flow of raw materials, work-in-progress items, and finished goods within the production facility. It provides real-time visibility and control over inventory, ensuring that materials are available where and when they are needed, thus preventing production delays and optimizing workflow.
A WMS in manufacturing is critical for maintaining the efficiency and productivity of production lines. By automating inventory management and providing real-time data, a WMS helps manufacturers maintain optimal stock levels, reduce waste, and ensure timely delivery of materials to the production floor. This capability is essential for just-in-time (JIT) manufacturing environments where the precise timing of material delivery can significantly impact production efficiency and cost management.
Inventory management is one of the core functions of a WMS in manufacturing. It tracks the movement and storage of raw materials, work-in-progress items, and finished products, ensuring accurate inventory levels. This function includes:
Order management in a WMS involves managing orders for raw materials and scheduling their delivery to the production line. This function includes:
Production support involves providing materials to the production line just-in-time, reducing wait times, and maintaining continuous production. This function includes:
Quality control ensures that materials meet quality standards before they are used in production. This function includes:
Traceability tracks the usage of materials in production, enabling full traceability from raw material to finished product. This function includes:
WMS significantly enhances operational efficiency by automating key warehouse functions. Automated processes reduce the need for manual intervention, minimizing errors and speeding up operations. For example, barcode scanning and RFID tagging streamline inventory tracking and order processing, ensuring that materials are correctly identified and placed in the right locations. This automation not only saves time but also reduces the risk of human error.
By leveraging real-time data, WMS ensures that inventory records are accurate and up-to-date. This accuracy is critical for maintaining optimal stock levels and preventing production delays caused by material shortages. Automated systems reduce the likelihood of mistakes in data entry and inventory tracking, thereby improving the reliability of inventory information.
WMS helps in reducing operational costs by optimizing inventory levels and improving order accuracy. By preventing overstocking and stockouts, businesses can lower storage costs and avoid the expenses associated with rush orders. Additionally, the automation of warehouse tasks reduces labor costs and enhances productivity.
A WMS provides comprehensive reporting and analytics tools that offer insights into warehouse operations. Managers can access real-time data on inventory levels, order status, and production schedules, enabling better decision-making and financial planning. This visibility helps in identifying inefficiencies and implementing corrective measures to improve overall performance.
WMS systems incorporate advanced security features to protect sensitive data and ensure compliance with industry regulations. Secure access controls and audit trails help in monitoring user activity and preventing unauthorized access to critical information. These security measures are essential for safeguarding company assets and maintaining regulatory compliance.
Integrating WMS with manufacturing automation systems ensures seamless synchronization between production schedules and inventory management. This integration allows for real-time updates on inventory usage and production status, enabling just-in-time delivery of materials to the production line. By aligning production with inventory levels, businesses can minimize downtime and enhance production efficiency.
The combination of WMS and manufacturing automation provides access to real-time data and analytics. This approach enables manufacturers to monitor key performance indicators (KPIs) and identify trends and patterns that impact production efficiency. Advanced analytics tools can provide actionable insights for optimizing production processes and improving overall operational performance.
A robust WMS provides end-to-end traceability of materials and products throughout the production cycle. This traceability is crucial for quality control and regulatory compliance. By tracking materials from receipt to final production, manufacturers can ensure that all products meet quality standards and can quickly identify and address any issues that arise.
Integrating WMS with quality control systems ensures that only high-quality materials are used in production. Automated quality checks at various stages of the production process help in identifying defects early and preventing defective products from reaching the customer. This integration enhances product quality and reduces the cost of rework and returns.
France’s electronic invoicing reform relies on a Y-architecture, where Partner Dematerialization Providers (PDPs) play a central role in issuing and…
The B2B mandate in Germany, set to take effect on January 1, 2025, marks a crucial step in the European…
Following the October 15 announcement regarding the abandonment of the PPF development, the DGFIP and its partner AIFE are ramping…
Work with our team to build your ideal supply chain software stack and tailor it to your unique business needs.