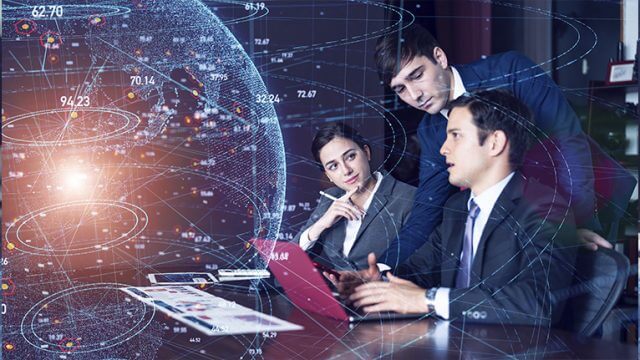
E-Invoicing and Its Geopolitical Stakes
France’s electronic invoicing reform relies on a Y-architecture, where Partner Dematerialization Providers (PDPs) play a central role in issuing and…
Generix Delivers Schematron for Electronic Invoicing to AFNOR to Ensure Interoperability Between PDPs Read the press release
In this series of blogs, our experts break down the various costs associated to a WMS’s TCO and offer some advice to help manufacturers maximize their ROI. In this blog, we focus on the costs of purchasing and deploying a new WMS.
The first item on the menu is obviously the WMS itself or, more precisely, the type of features offered by the solution and the deployment model you’ll favor. With Industry 4.0 and the IoT, manufacturers have far more options when it comes to finding a solution adapted to their reality. The most important thing to keep in mind, here, is that your initial expenditures and on-going annual costs will be distributed very differently whether you opt for a perpetual license or a subscription-based model.
A large pharmaceutical company with global outreach that runs complex production facilities all over the world, for example, may elect to purchase and deploy a WMS on-premises. This deployment method will afford them the liberty to radically customize their WMS to meet their complex production and security requirements. Note, however, that the initial expenditure for the system’s acquisition and implementation will be very high, especially if the servers and hardware necessary to run the WMS must also be purchased.
Meanwhile, a shoemaker that operates from a handful of factories and distribution centers may fare better by opting to deploy the WMS in SaaS mode. Because the solution is hosted on the provider’s servers, the grocer avoids the high initial expenditure to acquire the solution and necessary hardware. Instead, the grocer only needs to pay subscription fees to access the services and functionalities online.
With time, the TCO of an on-premise WMS usually breaks even with the same solution deployed in SaaS mode, around year 7 or 8. It’s important to keep in mind, however, that the average lifecycle of a given WMS version tends to be about 5 to 7 years. In other words, manufacturing companies that opt for an on-premise solution and want to maximize their ROI must also factor in the costs of acquiring the license to their system’s new version as well as the necessary upgrading fees. Choosing a WMS in a SaaS mode, avoids these extra fees altogether: a subscription-based WMS covers all upgrades, which are periodically performed by the solution provider on their own servers.
To get a better sense of how different implementation models might affect the solution’s TCO, take a look at this blog.
Regardless of the deployment model one opts for, manufacturers looking to implement a new WMS will have to account for the following expenses.
Onboarding/Training Fees
Manufacturing companies implementing their first WMS must prepare for a culture shock. To some extent, the same will be true for companies that are upgrading their current WMS to a far more complex solution. In every case, a WMS’s success at a manufacturing company will heavily depend on how well employees were guided through the changes.
To ensure that the system delivers ROI from the moment it goes live, manufacturers cannot skimp on onboarding and training efforts throughout the implementation process. Stakeholders should consequently make sure they ask their WMS vendor or implementation partner to schedule and clearly budget the necessary workshops and training sessions. As much as possible, companies must avoid making the all-too-common mistake of trying to save on implementation fees by cutting down on training.
You can read more about the common WMS implementation mistakes manufacturers must avoid here.
Data Migration Costs
The SOLOCHAIN WMS/MES achieves inventory data accuracy at rates well above 99%. It’s precisely for those levels of accuracy, the improved inventory management, and the processing efficiencies thereby unlocked that manufacturing companies implement a WMS.
However, to benefit from these capabilities from Go Live and to maximize ROI, companies must successfully migrate their data from their old systems to the new one. To that end, it generally proves profitable to hire – and budget for – a dedicated analyst.
Support, Maintenance, and Continuous Development Fees
Companies that deploy their WMS on-premises normally have to plan for the costs of on-going support and maintenance services once the solution goes live. Such fees include an SLA with the solution provider as well as wages for an expert inhouse IT team that can support and develop the solution.
With a subscription/SaaS model, SLAs are usually included in the subscription fees. However, it’s important to keep in mind that different solution providers offer different service levels. Premium SLAs may come at a premium price – buyer beware!
As your company grows its business thanks to the new WMS, scaling might present challenges and bring about new requirements.
To the costs of acquiring and implementing a WMS, manufacturers must yet add the investments required to integrate the solution with their technological and physical infrastructure.
Learn more about SOLOCHAIN WMS
Generix Group provides a series of solutions within our Supply Chain Hub product suite to create efficiencies across an entire supply chain. Our solutions are in use around the world and our experience is second-to-none. We invite you to contact us to learn more.
France’s electronic invoicing reform relies on a Y-architecture, where Partner Dematerialization Providers (PDPs) play a central role in issuing and…
The B2B mandate in Germany, set to take effect on January 1, 2025, marks a crucial step in the European…
Following the October 15 announcement regarding the abandonment of the PPF development, the DGFIP and its partner AIFE are ramping…
Work with our team to build your ideal supply chain software stack and tailor it to your unique business needs.