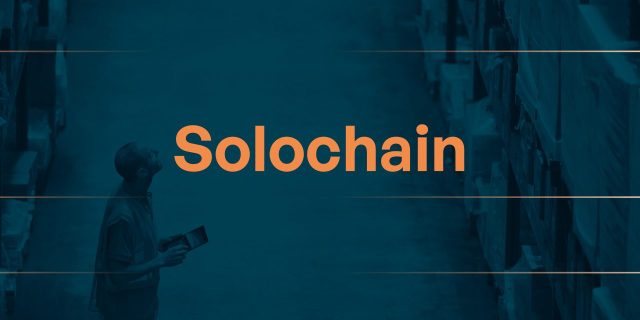
Generix Launches Solochain Now – Packaged Solution to Deploy a Complete SaaS WMS in as Little as 16 weeks
Chicago, IL, March 17, 2025 – Today, at ProMat 2025, Generix Group, a global business software company offering an expansive…
Generix Launches Solochain Now – Packaged Solution to Deploy a Complete SaaS WMS in as Little as 16 weeks View the press release
1) Performance, costs and risks: the three priorities of the Supply Chain Unsurprisingly, performance improvement (62%) and cost reduction (54%) came top of the list in terms of the major priorities facing logistics managers. Risk reduction (52%) was the third most common concern. The survey found differences in emphasis, depending on the sector and geographical coverage of the company in question. On the one hand, companies that conduct a significant proportion of their operations abroad (accounting for more than 50% of their total business) see greater flexibility as a major concern. On the other hand, performance improvement is a common priority across all sectors (distribution, consumer goods and services), with only the manufacturing and electronics sectors bucking this trend. Risk management, meanwhile, is the second most pressing concern in the distribution and service sectors, as well as for businesses with a lower level of international operations (less than 10%).
2) Logistics risk management: a concern for 8 out of 10 businesses Some 8 out of 10 businesses see operational risk management as a key concern. The survey found that it was a major concern for 49% of logistics managers and a medium-level concern for 30%. One of the most pressing risks for French companies is information system unavailability (46%). This was cited as the highest-impact risk across all sectors, closely followed by the one-off failure of a supplier (37.6%) and unexpected volume peaks (37.1%).
1) Risk prevention: Supply Chain Managers on the front line Some 65% of respondents to the survey stated that Supply Chain Managers were on the front line when it came to logistics risk management within their organization. This was the case for all companies operating in the distribution and consumer goods sectors.
2) Collaborative working: the poor relation of logistics risk management Only a minority of the companies questioned stated that they made full use of their ecosystem as part of their logistics risk management efforts. Less than one-third of respondents (31%) indicated that they had an external partner alert system in place, and barely 19% stated that they made proactive efforts to organize the ecosystem surrounding their business. When looking to handle logistics risks, the vast majority of companies focus on internal aspects. For example, almost two-thirds of the businesses questioned (65%) see the reporting of internal events as a priority. The survey results indicate that this is a key priority for businesses of all types, irrespective of their international operations or sector (distribution, consumer goods, manufacturing).
3) No collaborative working without visibility Opacity remains one of the dominating features of the logistics chain, i.e. the company, its freight forwarders, its carriers, its customers, and its suppliers. The results show that 58% of businesses have almost no visibility over potential risks involving their freight forwarders, 49% over risks impacting their suppliers, and 46% over risks affecting their carriers. Conversely, this figure falls to 37% when it comes to risks relating to its customers. Due to this lack of visibility, companies are almost certainly unable to implement an effective, collaborative risk management process.
4) Some 16% of respondents are playing with fire In total, 11% of the companies that responded to the survey admitted that they did not have a risk management policy. Worryingly, 5% had no idea how to approach this subject. This combination of naivety and incompetence is particularly concerning, especially where businesses are unaware of the potential impacts (both major and minor) of ineffective risk management. These impacts include indirect costs (disorganization, disputes) (61%), direct costs (credit notes, penalties) (58.7%), damage to the company’s reputation (45%), and even the loss of customers (31%).
“The findings of this survey show that Supply Chain Managers are fully aware of the importance of effective logistics chain oversight, particularly when it comes to boosting customer satisfaction. Yet the results also demonstrate that, in many cases, businesses have failed to implement an effective risk management system capable of safeguarding the entire logistics chain. It is important to stress that Supply Chain Managers cannot be expected to eliminate all risks since each stakeholder in the chain poses its own specific risks. Their job is to mitigate these risks. How can they achieve this aim? Through visibility and information. In other words, Supply Chain Managers must be able to identify an unexpected event quickly when it occurs in the logistics chain, including events occurring outside their own organization. They must also have access to the information they need to make informed decisions and mitigate the impact of this event on customer activities.
This is one of the main reasons why Generix Group has developed Easy Order Tracking – an innovative new solution designed to provide greater risk visibility and enhance collaborative risk management,” explains Isabelle Badoc, Supply Chain Product Marketing Manager at Generix Group.
Access the document
Chicago, IL, March 17, 2025 – Today, at ProMat 2025, Generix Group, a global business software company offering an expansive…
Generix is proud to announce that it has partnered with VISEO, a global technology and digital consulting company, to support…
Generix —a global business software company offering an expansive portfolio of SaaS solutions for supply chain, finance, commerce, and B2B…
Work with our team to build your ideal supply chain software stack and tailor it to your unique business needs.