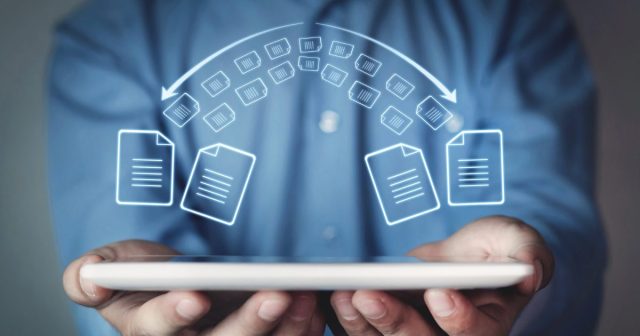
Cas d’usage et PDP : un enjeu clé pour l’interopérabilité de la facturation électronique
Avec l’ouverture imminente du service annuaire et la publication des spécifications techniques axées sur les flux de déclaration, les cas…
Generix lance Solochain Now – Une solution packagée pour déployer un WMS SaaS complet en seulement 16 semaines Lire le communiqué
La logique de la phase de stockage s’applique également à celle de préparation. Dans des entrepôts ou zones d’entrepôts traditionnels, on pratique la préparation en bas de palettier : les emplacements de réserve sont situés en hauteur avec des palettes complètes, tandis que les emplacements bas sont occupés par des palettes à prélever à l’unité ou au colis.
Pour maximiser la performance de la préparation, la corrélation entre demande et organisation est fondamentale dans le WMS. Et la gestion des pickings doit être entièrement adaptée à la typologie des ventes.
Pour cela, le WMS va donc proposer de gérer les emplacements de préparation picking de façon « fixe » ou « éphémère ». Dans tous les cas, ces modes de gestion demeurent complémentaires afin d’adapter les opérations aux besoins du marché. C’est pourquoi un picking « éphémère » peut devenir « fixe », par exemple lorsque la demande associée au produit décroît au fil des jours ou des saisons.
Le picking fixe, d’autant plus pertinent dans une organisation dite linéaire, est associé à un chemin de préparation correspondant à la logique de circulation dans les allées. Objectif : optimiser les déplacements ou la constitution du support de préparation, ou l’agencement dans le bac ou le colis.
Cela permet, in fine, d’éviter une rupture de charge en fin de préparation ou à l’arrivée chez le client. En clair, on privilégie dès le départ la préparation d’une commande en un seul colis dans la mesure du possible. On évite ainsi d’avoir à les emballer à nouveau en fin de préparation ou de les expédier en deux colis alors qu’un seul aurait pu suffire.
La création des circuits est définie par le gestionnaire des stocks en fonction des besoins des clients. Elle respecte des règles liées aux produits : catégorie, famille, poids / volume, rotation, etc. Il existe toutefois une multitude de combinaisons possibles afin d’optimiser leur constitution et de favoriser leur complémentarité. Les algorithmes sont alors importants dans le WMS pour donner au gestionnaire de la visibilité sur le duo stratégique charge / capacité.
Dernière étape : un chemin est établi sur analyse des données relatives à la vie de l’entrepôt en combinant espace disponible et typologie des produits, en fonction de la demande. Au moment du stockage des produits en réception, on va utiliser d’autres calculs pour proposer des emplacements de réserve au plus près des pickings correspondants à chaque référence.
Avec le picking éphémère ou « sous contrainte », on recalcule l’implantation des pickings de façon dynamique lors du traitement de la vague de préparation en fonction des contraintes :
Des algorithmes vont alors être mis en place pour implanter des pickings correspondant à chaque référence de la manière la plus pertinente. Cette approche s’avère très efficace pour gérer les groupes de références relativement restreints, qui sont soumis à une très forte demande pendant une période limitée. C’est par exemple le cas lors du lancement d’une nouvelle collection ou d’une promotion.
Le « batch picking », ou « massification », est une méthode de préparation de commandes qui se caractérise par le prélèvement simultané de plusieurs unités d’un même code SKU pour différentes commandes.
Concrètement, le préparateur utilise un chariot de préparation sur lequel seront disposés n contenants correspondant à n commandes différentes. Il pourra alors distribuer la même référence sur plusieurs commandes au même point de prélèvement, minimisant ainsi ses déplacements. Pour aider le préparateur, un algorithme va calculer le découpage des missions pour les regrouper de façon optimale.
Ce principe est particulièrement utilisé dans les secteurs du e-commerce et du textile qui gèrent énormément de petites commandes (entre 1 et 3 pièces en général).
On peut distinguer quatre grands types de missions pour un cariste :
Ces missions peuvent être combinées ou croisées. On utilise alors le terme anglais d’interleaving.
Un grand gisement de productivité réside dans la combinaison de missions de stockage avec des missions de déstockage. Le plus fréquemment, on va combiner deux missions dont les points de dépose et de ramasse se trouvent dans la même allée. Ces stratégies sont particulièrement efficaces dans les aires de stockage dites « ailes étroites » (VNA pour very narrow aisle) car les chariots « tridi » (turret truck) sont plus lents. Elles sont également cruciales dans le cas de l’utilisation de chariots de type AGV (Automated Guided Vehicle), dont les vitesses de déplacement sont particulièrement lentes.
Il est aussi possible de calculer la constitution des missions en fonction d’un algorithme de calcul des distances. Cette fonctionnalité se met en œuvre grâce au paramétrage d’un distancier. Celui-ci consiste à mettre en place des points de repère et des liens entre allées de stockage de façon à calculer la longueur du trajet entre deux points de stockage, qui peuvent être situés dans des allées différentes.
La triangulation est une méthode utilisée pour la mesure des distances à l’échelle humaine. Il s’agit d’un processus permettant de déterminer une distance en calculant la longueur de l’un des côtés d’un triangle, et en mesurant deux angles de ce triangle grâce à des entités trigonométriques. Le WMS s’en inspire pour l’appliquer à la gestion d’entrepôt et ainsi optimiser les déplacements en appliquant les chemins les plus directs possibles.
La triangulation s’avère optimale dans un contexte en radiofréquence. En effet, des scénarios assurent la génération automatique de missions par triangulation pour les caristes ou les achemineurs. Dans ce cas, les algorithmes du WMS vont travailler à partir de plusieurs éléments :
Le WMS sait aussi calculer une attribution intelligente des quais à deux moments clés.
Avec ce mode de fonctionnement, le WMS va pouvoir synchroniser des flux de différentes natures (mono ou multi-commandes, etc). Cela va lui permettre d’affecter dynamiquement un quai de chargement final au moment de la validation des supports en fin de préparation. L’algorithme tiendra alors compte de l’état d’encombrement des quais tout en vérifiant les critères de cohérence (client, date de livraison, commande).
On utilise également des méthodes à base d’algorithmes permettant de remplir au maximum les camions. Ce travail s’effectue la plupart du temps en collaboration avec le TMS.
Le concept de cross-docking consiste à redistribuer des supports en réception directement vers un quai d’expédition sans passer par une étape de stockage. Les algorithmes du WMS peuvent jouer sur deux tableaux. Dans le cas des entrepôts de grande longueur qui ne sont pas conçus comme des plateformes de cross-docking, on privilégiera une affectation intelligente des quais de réception et / ou d’expédition, de façon à les rapprocher et à minimiser ainsi les distances de déplacement.
Dans le cas de références en réception qui sont aussi en stock, le WMS peut mettre en œuvre des algorithmes plus sophistiqués qui vont tenir compte de plusieurs paramètres. À savoir : on peut servir un besoin « en vague » avec une palette réceptionnée à quai. Le système est aussi autorisé à servir sur le quai afin d’éviter des transferts successifs (le but est de minimiser les « ruptures de charge »). Dans ce cas, on peut décider de ne pas respecter le FIFO (First In First Out). Le système vérifie le respect des dates de péremption et des « contrats date ».
Avec l’ouverture imminente du service annuaire et la publication des spécifications techniques axées sur les flux de déclaration, les cas…
Toutes les Plateformes de Dématérialisation Partenaires (PDP) ne proposent pas les mêmes services, et cette diversité peut impacter votre conformité…
La réforme de la facture électronique en France repose sur une architecture en Y, où des Prestataires de Dématérialisation Partenaire…
Travaillez avec nos équipes pour concevoir et mettre en œuvre la Supply Chain qui accompagnera votre croissance, adaptée à vos spécificités métier.