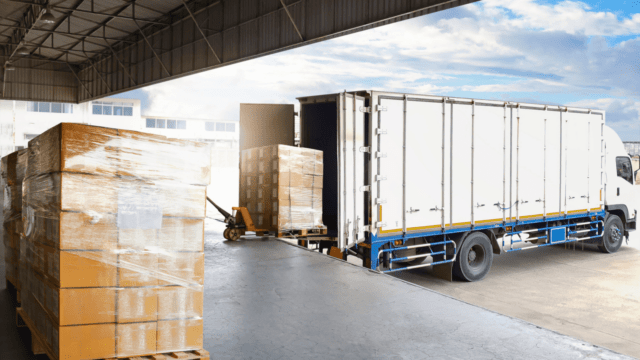
Quali sono i vantaggi di un TMS (Transport Management System)?
L’uso di un TMS (Transport Management System) consente di gestire tutte le operazioni di trasporto di un sito logistico. Dalla…
Replay Webinar | La logistica dell’e-commerce Vai al replay
Una recente missione del DataLab di Generix Group presso uno dei clienti del gruppo ha mostrato come le rotture di stock durante la fase di preparazione siano il primo fattore responsabile del calo di produttività. È quindi fondamentale che il preparatore non si ritrovi mai davanti a un’ubicazione vuota o sguarnita, poiché gli impedirebbe di predisporre l’ordine da servire.
In casi come questo, per completare il suo compito, l’operatore dovrebbe fare richiesta urgente di riapprovvigionamento (un’opzione che resta, tuttavia, sempre possibile) e aspettare che un pallet venga “fatto scendere” dalla riserva. Se il preparatore può comunque passare a gestire un altro ordine, il flusso di processo non si svolge di certo in maniera ottimale.
Per evitare situazioni di questo tipo, è possibile mettere in campo due strategie preventive: la regolazione dei livelli soglia di riapprovvigionamento e la previsione in funzione dei calcoli effettuati a monte (con un giorno di anticipo, ad esempio).
Le soglie di riapprovvigionamento permettono di evitare le rotture di stock. Impostando determinati parametri, infatti, verrà attivata una missione di riapprovvigionamento non appena si raggiungerà una quantità minima o “soglia di riapprovvigionamento” in un’ubicazione di picking.
Si tratta di un lavoro accurato, poiché dovrà tener conto della capacità dell’ubicazione di stoccaggio. In parole povere, non è possibile collocare due pallet in un’ubicazione concepita per uno solo, ma con buona probabilità sarà plausibile sistemare un pallet e uno strato di scatole di cartone. Dopo aver inserito nel sistema le dimensioni delle ubicazioni, dei pallet e dei cartoni, il calcolo verrà effettuato automaticamente grazie a semplici algoritmi che sommano le misure degli oggetti con un certo grado di tolleranza.
Per elaborare le previsioni è possibile utilizzare uno strumento di simulazione basato anch’esso su un algoritmo, che avrà il compito di simulare l’onda di preparazione in base al portafoglio degli ordini da servire. L’algoritmo ricava il numero totale necessario per ciascuna referenza, verifica le quantità residue nell’ubicazione di picking e lancia in maniera automatica una raffica di missioni di riapprovvigionamento, mirate sulle richieste da servire nel più breve tempo possibile.
Questa operazione può essere calcolata a partire dal portafoglio degli ordini già ricevuti nel software gestione magazzino WMS, ma può essere basata anche sui dati previsionali trasmessi dall’ERP al WMS sotto forma di messaggio dedicato. Ad esempio, si possono utilizzare i consumi di magazzino dell’ultima settimana in un periodo di riferimento ritenuto rilevante per tener conto della stagionalità o di qualsiasi modello di business ciclico.
È anche possibile completare tutti i picking con un giorno di anticipo, il problema di questa strategia, però, è che funziona soltanto quando si hanno a disposizione tempo e risorse. In caso di processi just-in-time, la selezione dei riapprovvigionamenti effettivamente utili rimane, senza ombra di dubbio, l’approccio migliore.
Quando ci si trova a gestire periodi di just-in-time con carichi molto elevati, gli algoritmi del WMS permettono di realizzare previsioni ancora più accurate per quanto riguarda il lancio delle missioni di riapprovvigionamento in funzione delle urgenze. Ciò garantisce un utilizzo ottimale delle risorse incentrato sui fabbisogni critici in tempo reale.
Lo strumento consente di automatizzare la gestione dei riapprovvigionamenti lasciando al sistema il compito di attivare la missione al momento più opportuno a seconda delle necessità, basandosi naturalmente sui dati teorici specifici di ciascun magazzino e sul tipo di gestione dei flussi di preparazione. Questa funzionalità ad alta intensità di calcoli algoritmici terrà conto di numerosi parametri:
A partire da questi criteri, a cui è possibile attribuire una gerarchia in base a dei parametri, il sistema ricalcola le esigenze delle preparazioni in corso e definisce un timing esatto per il lancio di una missione di riapprovvigionamento. Per illustrare la profondità di questo calcolo, si possono prendere in considerazione elementi come il tempo di presa in carico, il tempo di cambio prodotto, il tempo di cambio corsia, il tempo di previsione e persino il tempo delle pause.
È possibile combinare le date di scadenza con il rispetto dei “contratti con data garantita”, basterà aggiungere un margine di sicurezza configurabile al periodo di scadenza di un prodotto alimentare, ad esempio, al fine di rispettare un impegno assunto col cliente. Si tratta di una pratica molto diffusa nel settore della grande distribuzione, che mira a garantire una determinata shelf life, soprattutto nel caso di derrate deperibili.
Questo algoritmo di rispetto dei “contratti con data garantita” è applicabile anche a tutte le operazioni del magazzino, e rappresenta quindi uno dei punti di forza del software gestionale WMS di Generix Group.
Si tratta di una fase molto importante in un contesto di ottimizzazione della pianificazione del lavoro in funzione di un portafoglio di ordini da evadere. Si selezionano gli ordini, o determinati elementi di essi, quindi si sceglie una modalità efficace di gestione per evaderli.
Per effettuare questa operazione in maniera automatica è necessario configurare le “onde” di preparazione degli ordini. Un’onda è una selezione effettuata all’interno del portafoglio sulla base di una molteplicità di criteri, i più rappresentativi dei quali sono:
Parimenti, si possono immettere degli ordini provenienti dal Transportation Management System (TMS). In questo caso, si parla di “preparazione basata sul TMS”.
La principale dote di un responsabile di magazzino sta nel saper affinare i propri strumenti per orchestrare il lavoro in funzione delle fasce orarie gestibili e regolabili in base al carico del giorno e alle risorse disponibili. Tradizionalmente, le pianificazioni riguardano metà giornata o la giornata intera, anche se tutte le attività possono essere svolte secondo il sistema organizzativo prescelto dal responsabile. Inoltre, è anche possibile scegliere i propri modelli di onde di preparazione degli ordini in funzione delle esigenze del giorno.
L’onda, il cui risultato è un elenco di prodotti da preparare costituisce solo il primo passo del calcolo algoritmico e non è incentrata tanto sulla produttività delle attività, quanto sulla priorità degli ordini da servire. In funzione di questo elenco il sistema calcola i flussi successivi di lavoro su gruppi di ordini, generando infine quelle che vengono definite “missioni”, cioè elenchi di compiti che verranno proposti agli operatori. Si pone quindi la questione di come organizzare questi incarichi in maniera razionale per migliorare la produttività del magazzino. Entrano quindi in ballo molteplici parametri, tra cui l’ottimizzazione dei percorsi di preparazione o la triangolazione.
L’uso di un TMS (Transport Management System) consente di gestire tutte le operazioni di trasporto di un sito logistico. Dalla…
Quando le operazioni logistiche crescono e/o diventano più complesse, un software WMS (Warehouse Management System) diventa essenziale. Si tratta di…
Molte aziende sono ora impegnate in un approccio eco-compatibile.. Stanno mettendo in atto strategie per rispettare gli standard ambientali e…
Collabora con il nostro team e costruisci il software ideale per la supply chain, adattandolo alle tue esigenze aziendali.